WRI EU 2015 Part 1: Systemic Challenges, Systemic Successes
By Jeff Tuzik
For over 20 years, the Wheel/Rail Interaction conferences have brought together railway industry professionals, researchers and suppliers to share their expertise in the field of wheel/rail interaction. Until recently, the conferences have been held only in the United States and have drawn on North American experiences. In the fall of 2015, Wheel Rail Seminars hosted its first Wheel/Rail Interaction EU conference in Derby, UK.
Of course, the principles of wheel/rail interaction are the same in North America as they are in the EU. But different conditions, different areas of research, and different approaches to managing wheel/rail interaction mean that there is information and new developments that don’t always make it across the Atlantic. But it’s important that information is shared back and forth, because regardless of differences, the end goals are the same.
And, as the experts gathered at the WRI EU Conference made clear, the fundamental challenges are the same, too. Wheel/rail interface management requires a systems-level approach in order be optimized. And a systems-level approach requires tools and techniques from every department and field of expertise. “WRI concepts remain too confined to specialists,” said Mark Dembosky, Vice President of International Engineering. “True systems optimization won’t occur until knowledge becomes endemic to the system at all levels.”
Part of what makes system-wide optimization challenging is the scope and interplay of the system itself. The ways in which one part of the WRI system affects the others isn’t always simple or intuitive. Steering forces, for example, are generated at the wheel, bogey and vehicle levels in different ways. These forces are heavily influenced by wheel and rail profiles and the resultant contact mechanics. Surface and friction conditions play a role, too. So, if poor steering is negatively affecting the system, identifying the bad actor or culprit can take some digging.
“In each case, the best solution is based upon first identifying the pertinent WRI factors and then the practical and cost considerations,” Dembosky said.
Further complicating the issue is the need for a coordinated effort involving different departments with different areas of expertise to address each part of the whole. “Knowledge of wheel/rail interaction is the key to improving decision making whether at the front line or executive levels,” Debmbosky said.
Like many European railways, London Underground has worked hard to implement a systems-approach to managing wheel/rail interaction. London Underground stands out, though, in that it has a management position dedicated to managing wheel/rail interaction. Andy Vickerstaff, Senior Wheel Rail Interface Engineer at London Underground, works with all departments in the railway to address systemic issues.
“While there are some forward-thinking people working on rail transit systems, this is a position that simply doesn’t exist in North America,” said Gordon Bachinsky, president of Advanced Rail Management and founder of the Wheel/Rail Interaction seminars.
One of the early projects that Vickerstaff and the London Underground WRI team undertook looked into issues with track-based lubricators. The investigation, which brought together the track and vehicle departments, determined that some of the cars running through the lubricators weren’t distributing the lubricant efficiently. Instead of being carried down the track, much of the grease ended up on the car undercarriages and brake actuators, causing wheel flats, high wheel/rail wear, and requiring additional cleaning and maintenance of the vehicles. The investigation determined that seasonal temperature changes were affecting the viscosity of the grease, and thus the rate of application. By adjusting application rates and switching to a less temperature-sensitive lubricant, the WRI team was able to alleviate these adverse conditions.
The WRI team has also explored the impact of worn — particularly hollow-worn — wheels. By measuring a sample of wheels on the line and modeling their behavior using VAMPIRE® software, the LU was able to identify their effect on rail wear and the combined effect of worn wheels and rail on wheel re-truing and rail maintenance and renewal. The investigation found that hollow-worn wheels generate a net 3% increase in damage into the system – a figure that ultimately translates directly into cost. “A big part of managing the wheel/rail interface is being able to make the business case for taking a systems approach,” Vickerstaff said.
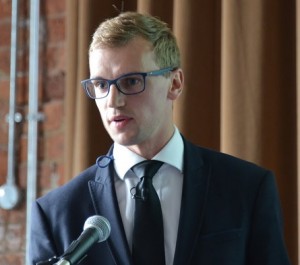
On the rail side, the team looked into rail renewal – particularly renewal as a result rolling contact fatigue (RCF) and associated defects. Like many railways, LU used to base its grinding program primarily on noise and vibration and corrugation issues. That’s no longer strictly the case. LU now also uses inspection tools like magnetic flux and ultrasonic testing to quantify the severity of RCF and to take a data-driven approach to rail grinding. “We use a magic-wear-rate-influenced maintenance regime; RCF is the life-limiting factor in a lot of our curvature,” said Dominic Trueman LU’s Principal Track Engineer and Chief Operating Officer – Engineering. LU is also beginning to use predictive modeling based on historical data to identify priority rail grinding sites.
Vickerstaff and the WRI team recently developed and applied a model that successfully “predicted” 75% of the priority RCF sites that were discovered by physical testing. “This is all part of the Predict & Prevent program on the London Underground,” Vickerstaff said. “We move millions of people a day, and if we can predict our maintenance needs, we can plan accordingly and drastically reduce lost customer hours.” LU’s 24-hour Night Tube service is currently expanding, which means track access is going to become harder to come by, making predictive and preventive maintenance strategies that much more important.
LU’s systems approach to WRI management is effective, and progressive by North American standards. But there are cultural challenges in the UK, too. “We’ve got 150 years of siloed mentality to fight through, but we’re making progress,” Vickerstaff said.
A systems approach to wheel/rail interface optimization doesn’t only benefit massive and complex systems like the London Underground. Smaller, light-rail and tram systems operate on the same principles and benefit from the same approach.
“Light-rail is a closed system, so there’s a lot of room for optimization,” said Adam Bevan, Head of Enterprise at the Institute of Railway Research, University of Huddersfield.
Light-rail comes with its own challenges as well as opportunities. The combination of characteristically tight-radius curvature and grooved rail is one such challenge. Many systems also have to contend with independently rotating wheelsets which lack the self-steering ability of standard wheelsets and add to an environment of very high wear; “we typically see wear as the limiting-factor in rail life, rather than RCF damage mechanisms,” Bevan said.
Previous studies conducted on behalf of the Office of Rail and Road and UKTram, Across the UK, show that high wear is often exacerbated by a number of suboptimal systemic conditions, including:
- A large variety of wheel profiles and no defined standard profile.
- Large variation in conicity across wheel profiles and variations in profile conicity within single systems.
- Use of both independently-rotating and standard wheelsets (see also: Flange Climb and Independently Rotating Wheels).
- Variation in grooved rail groove depth and width.
- Variation in wheel and rail maintenance limits.
Wheel/rail interaction is complex, and difficult enough to optimize under ideal conditions. These factors only make it harder. “The biggest issue here is a lack of standards and guidance,” Bevan said. Without standards, systems are often designed, built and maintained without the full benefit of hard-won knowledge regarding wheel/rail interface optimization.
In addition to the work of developing standards, UK light rail systems are also working to adopt a more proactive approach to maintenance. It’s an approach that echoes London Underground’s “Predict and Prevent” model. A preventive or proactive approach to maintenance not only benefits the efficiency of the maintenance regime, but the health of the system overall, Bevan said.
Equivalent Conicity
One of the most critical aspects of wheel/rail interaction is the geometry at the point of contact. The equivalent conicity, a figure that expresses the geometrical relationship between a given wheel profile and rail profile, forms the basis for a number of models and simulations that explore the dynamics of wheel/rail interaction, said Paul Mittermayr, Managing Director – Head of Research and Development at the Bureau of Applied Mechanics and Mathematics.
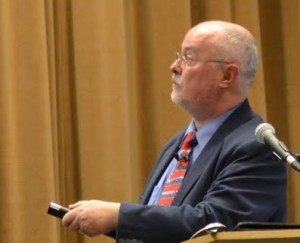
Wheel/rail contact geometry influences running behavior in many complex ways. Comprehensive analyses of these dynamics typically require cumbersome and time-consuming simulations and as such are usually limited in scope, he said.
While equivalent conicity can be calculated relatively easily for design specifications, determining in-service equivalent conicity is much more difficult, since it requires a separate calculation for every combination of wheel profile, rail profile and gauge measurement. That means significant post-processing is necessary. Another difficulty of measuring equivalent conicity in-service is the precision required. “Accuracy on the order of 0.1mm is necessary for accurate calculation,” Mittermayr said.
Despite these difficulties, Amtrak, the U.S. passenger service, which operates at speeds up to 150 mph in the Northeast Corridor, is currently in the early stages of developing a program that monitors equivalent conicity as part of a standard wheel and rail measurement cycle.
The program is driven by the need to monitor stability and truck hunting on the high-speed Acela line. “Monitoring equivalent conicity is especially critical for high-speed vehicles in either tangent track or in large radius curves at low cant deficiency,” said Steven Chrismer, Senior Mechanical Track and Vehicle Engineer at Amtrak/LTK Engineering. Amtrak hopes to use the program in part as an early-warning system for conditions approaching maximum allowable conicity thresholds. “The ultimate goal is knowing when and where this limiting conicity is approaching,” he said.
Having up-to-date equivalent conicity calculations could also allow Amtrak to manage its wheel and rail re-profiling program in a more proactive manner. The data could be used to trend rates of change in equivalent conicity and thus facilitate more targeted, scheduled wheel and rail re-profiling, he said.
Wheel Wear
The ability to accurately model and predict wheel wear is another important and challenging aspect of wheel/rail interface management. Like other aspects of the wheel/rail system, wheel wear is influenced by a number of factors that are systems unto themselves.
Wheel wear characteristics at a system level take into account:
- Suspension type
- Environmental conditions
- Lubrication, friction modification and surface contamination
- Contact conditions and geometries
- Material properties
- Route characteristics
- Traction and braking
Each of these characteristics can be further broken down; route characteristics, for example, takes into account parameters like curve radii and cant deficiencies, traction and braking forces.
Modeling wheel wear is a complex proposition. Tools such as the Wheel Profile Damage Model (WPDM) were developed to streamline the process and to provide accurate prediction of wear rates and patterns for wheels in service under a variety of conditions. The model has been shown to provide good wear predictions of both wear patterns and rates for wheels covering in excess of 150,000 miles, said Julian Stow, Assistant Director of The Institute of Railway Research, University of Huddersfield.
Using the WPDM, the Institute of Railway Research at University of Huddersfield recently undertook a study that explored wear patterns and characteristics of wheels with varying flange heights and thicknesses. The purpose of the study was to help build a case for a change in requirements for turning/re-truing thin-flange wheels. “Currently, operators aren’t able to turn wheels with thin flanges; they have to restore the wheel to a full flange thickness,” Stow said. The proscription against thin flanges means operators are unable to implement an economic tyre-turning program that makes use of modified thin-flange profiles in order to increase overall wheel life.
The IRR/Huddersfield study sought to determine if there are significant differences in wear patterns between thin-flange wheels and design patterns; the results indicated that there are not. The data showed that the wear characteristics of the thin-flange profiles in the study were very similar to the design profiles, and that tread and flange wear rates were nearly identical. “What we found adds to a significant body of evidence in support of using economic tyre-turning,” Stow said.
Simon Jarrett, Head of Technical Services at Chiltern Railways echoed the importance of investigating tyre-turning practices: “We have to minimize tyre-turning in order to maximize wheel life,” he said. Chiltern Railways uses the Atlas FO program to monitor wheel tread condition and also uses the data collected to identify wear trends and optimize tyre-turning intervals. “We estimate that the program on its own has increased overall wheel life by 20 percent; when we tyre-turn, we know we’re not taking any more metal than is necessary,” Jarrett said.
Wheel profile and wheel-turning methodology are only one piece of the wheel wear picture. Depending on the system, different parts of the wheelset can be the life-limiting factor. As a result, railways like Chiltern employ a variety of condition-monitoring equipment and techniques to take a comprehensive look at in-service wheelset health. This includes monitoring brake pads and actuators, axle bearings and suspension elements. It also includes the use of wheel impact load detectors to identify bad actors before conditions worsen.
“All elements of the wheelset have to be optimized, so all elements have to monitored,” Jarret said.
Third Body Layer
A finely tuned wheelset and profile will only perform optimally if the track is also in optimal condition. That optimal condition is largely affected not only by the wheel and rail, but also by friction and the properties of the third body layer — the various contaminants that modify friction characteristics between wheel and rail.
Use of friction modifiers and lubricants is now common in the railway industry. But the techniques for applying these materials, as well as the materials themselves, are ever-evolving.
Network Rail recently began an investigation into the use of a top of rail (TOR) friction modifier (FM) at switch points in order to reduce flange impact and the associated switch rail damage. The investigation was initiated due to abnormally high damage and wear rates at the railway’s Nuneaton Junction. Switches at this location were lasting as little as three months before requiring weld repairs, and had to be replaced after only three repairs, said Jay Benson, Senior Asset Engineer – Track at Network Rail.
Analysis determined that the damage mechanism was a very high angle of attack (AoA) leading to sustained hard flange contact. In order to alleviate the AoA issues, Benson tried a single application of a water-based TOR FM at the affected switch point. “After this single application, contact became much lighter, and more intermittent,” he said. This finding led to the installation of an FM applicator at the site.
After a year of in-service testing, the railway saw a six-fold reduction in the time required between repairs. The success at the Nuneaton Junction site led to the installation of TOR FM applicators at other high-wear switch sites. All of the sites saw benefits, some more so than others “Weld repairs that were a regular feature [at some sites] haven’t been required at all since the FM applicators were installed,” Benson said. These wear savings translate directly into cost savings. “We’re saving up to £100,000 per year, per switch in some cases,” he said.
The next step for Network Rail is to identify other switch sites that could benefit from FM installations. Network Rail is also working with LB Foster to install strain gauges at one of the FM installation sites in order to measure and quantify the effects of the FM on force reductions and AoA. Despite not yet having accumulated extensive data, it’s clear that the FM installations have greatly alleviated the problems, Benson said.
This investigation also illustrates that despite the availability of modern simulation and modeling techniques, sometimes a simple test (in this case, manually applying a film of FM and observing the results) anecdotally seems to be an effective test, Benson said. Future, and larger-scale viability tests will, however, be based on strain gauge data and vehicle/track simulation.
When it comes to the third body layer, sometimes the goal isn’t to add a friction modifier to the rail surface, but to remove a deleterious contaminant. One such contaminant that appears every fall is leaf matter. Fallen leaves stick to the rail and accrete over time, forming a caked-on layer that results in a very low coefficient of friction, which negatively affects traction and braking, leading to station overruns and service delays, which impact both operational safety and efficiency.
As a measure against these conditions the Dutch railway operator Nederlandse Spoorwegen Reizigers (NSR) recently developed, and is currently testing a water spray installation (WSI) system. The system, which in function is somewhat similar to a wayside TOR FM applicator, applies a small amount of water to the track surface as a train approaches. The water, combined with forces at wheel/rail contact patch, breaks up the leaf layer. The rail is scrubbed clean by the passing trains, leaving a surface that is difficult for leaves to adhere to before the next train passes, said Margreet Beuving, Specialist – Mechanics, Dekra Rail.
Other techniques for clearing leaf matter from the track include vehicles that apply Sandite (a kind of engineered sand solution) to the rail, or those that perform water-jet cleaning. These methods are proven effective, but are more costly and disruptive to service, Beuving said. The WSI has the benefit of operating in conjunction with the existing revenue service.
Introducing any substance onto the track naturally brings up questions about traction and adhesion. To answer these questions, a water spray installation system was tested at several on-track test sits, as well as on a laboratory twin-disc setup. Both laboratory and field test results showed that the WSI system brought braking and traction values into the same range as clean, dry test track, Beuving said.
Tests also showed that, like an FM installation, the WSI must be continuously active for optimal efficiency. “If the unit is deactivated, the leaves and the associated low adhesion, build up quickly,” she said. Further testing of the WSI system is currently underway, with expanded revenue testing to follow.
Managing Rail Life
One of the major issues facing European railway systems that doesn’t appear to be an issue in North America is the emergence of a squat-type defect, known as a “stud.” Studs were first noted roughly 15 years ago and are so-called given their superficial similarity to squats. Squats, a better known defect type, are treated aggressively due to their linkage to catastrophic rail breaks, said Stuart Grassie, Principal, Rail Measurement Ltd/Stuart Grassie Engineering Ltd.
Unlike squats, when studs began to appear, they appeared not just on high-speed lines, but on transit and freight lines, too. The London Underground is one of many railways currently wrestling with studs. Like squats, studs appear as small paired depressions or indentations in the rail head surface. The orientation of the depressions typically forms a “V” that points toward the field side of the rail. Defects often appear in a series.
Studs have historically been classified and treated as squats – in other words, treated as defects that could break rails. This approach has often led to very expensive treatment programs. But that may not be necessary, Grassie said. “It is clear now from recent work that studs are not in fact squats.”
Ultrasonic testing has shown that stud crack growth develops transversely, and that the depth of the crack stays more or less the same over time. These characteristics set them apart from squats. Additionally, studs develop very quickly, whereas the RCF mechanisms behind squat development take much longer.
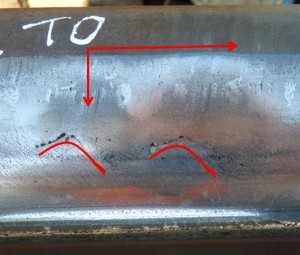
Studies by various organizations indicate that studs initiate as a result of small crack formation due to locomotive or powered-axle wheel-slip. The increase in the number of studs appearing in track has been circumstantially linked to the rise in traction demands. Furthermore, several railways have evidence of a strong correlation between software-controlled traction systems and stud development, Grassie said. Although the physical evidence is clearly visible, some of the growth mechanisms are still not understood. “There’s room for much more research here,” Grassie said.
The take-away from the current body of research is that studs are “stable” growth defects that develop at a constant depth. Studs can spall out and generate high impacts, but they don’t cause rail breaks the way squats can, Grassie said. Consequently, studs should be treated differently than squats; “If you were to treat these defects as squats, it would shut down London Underground, and it would shut down Sydney Trains,” he said.
By looking more closely at the defect and growth mechanism, railway operators can modify their approach to maintenance to ensure that their solution fits the problem. Stud growth occurs relatively quickly. Defect development has been seen to occur in as little as 28 days on the London Underground, so taking preventive action is very difficult, said LU’s Dominic Trueman. Other options, such as modifications to traction systems are very costly, and the precise traction parameters that lead to stud development haven’t been fully explored. In addition to the difficulty of treating studs, there is difficulty simply in identifying them and telling them apart from potentially catastrophic squats.
Despite the difficulty of taking preventive action against squats and studs, one of the ways they can both be addressed through the use of corrective rail grinding and milling.
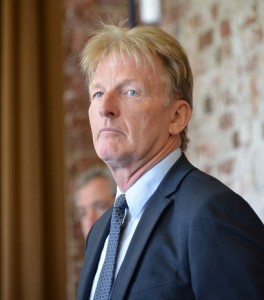
Rail grinding has been used for decades to address many of the adverse contact conditions (corrugations, profile deformation, RCF) that develop at the wheel/rail interface. Metal removal from wear or by “artificial wear” through grinding is necessary, said Wolfgang Schoech, Director of External Affairs, Speno International SA. “It’s always about metal removal.”
Corrective, or symptom, grinding, such as grinding done to remove various defects, was the first type of grinding strategy that was developed, and is still useful and heavily used today. Corrective grinding is typically done at specific intervention thresholds – based on either defect type or a fixed threshold, such as RCF crack depth, for example. Despite an overall industry shift toward prediction and prevention, corrective grinding will always be a necessary part of the tool kit, as not every defect can be predicted or prevented.
Preventive grinding is done before the defects appear, which typically means there is less metal removal overall than corrective grinding regimes, Schoech said. In these cases, grinding is planned based on both historical and projected data. “A little preventive grinding done on a regular cycle buys you a lot of time in which you have optimal surface conditions,” he said. The aim of the preventive grinding approach, often illustrated via the “magic wear rate,” is to alleviate the need for major corrective grinding down the line. This is the primary difference between corrective and preventive grinding, he said.
There are a number of specialized grinding applications, as well, such as the use of wear-reducing, fatigue-reducing, vehicle dynamic-improving profiles (see also “wear adapted profiles”: Target Profiles for Rail Grinding: A Never Ending Story). Asymmetric grinding can also be used to move or modify the contact patch. This can be done to improve equivalent conicity in curves and reduce hunting in tangent track, as in the case of the Amtrak Acela re-profiling program, for example, Schoech said.
Rail milling, a newer technology than grinding has begun to see more widespread application in Europe. Milling is typically used in tandem with grinding as part of an overall maintenance strategy.
Deutsche Bahn AG, for example, uses both milling and grinding, employing whichever method best suits the end goal. As a rule of thumb, DB has found that for operations requiring metal removal of up to 1mm, grinding is more economical, while for jobs requiring metal removal of 1.5mm or greater, milling becomes more economical, said Rene Feuler, Technical Business Unit Manager, Strabag Rail GmbH. Rail milling’s capacity for high metal removal is particularly appealing to railways that are working to correct characteristically deep defects like squats or severe RCF.
There are other considerations beyond the depth-of-cut metric — environmental impact, for example — that factor into the decision to mill, rather than grind rail. Milling has proven to work well in sensitive urban and tight-clearance-envelope type areas. This is due to the low spark stream and significantly reduced fire hazard, as well as the enclosed milling heads that prevent any rail material from being ejected outside the vehicle envelope.
Milling has its limitations, though. Milling machines and their cutting heads are more limited than grinders in terms of their ability to re-profile the gauge face of the rail. Milling machines also lack the ability to modify the target profile on the fly the way modern grinders can, Fueler said.
As the North American market has begun to discuss rail milling and its applications, there has been a sense that milling and grinding are competing technologies rather than complimentary. The various applications of milling and grinding in Europe show this not to be the case. “We see milling as the step before rail replacement. Instead of having to replace rail due to deep defects, milling can be applied to extend rail life,” Feuler said.
As more railways pivot toward a model of wear and defect prediction, and preventive maintenance, rail grinding and milling will likely continue to be among the most-used tools in the kit. Tools like these that are focused on optimizing rail geometries are a critical component of wheel/rail interface management.
It’s also clear that the wheel-side of the equation hasn’t been neglected either. Despite some differences in the challenges faced and techniques employed, it’s clear that the greatest success stories in the European Union share something fundamental in common with the success stories of North America: a systems-based approach to wheel/rail interaction.

All photos courtesy of Kordula Mittermayr.
Jeff Tuzik is Managing Editor of Interface Journal.