Using Derailment Findings to Identify Derailment Risks
Presenters at the 2022 Wheel/Rail Interaction conference looked at heat and track configuration issues as they relate to derailment potential in heavy-grade, high-tonnage territory. They also looked at the role of Operating parameters in derailment potential, and at the findings from 20 years of investigations into derailments.
By Bob Tuzik
History has shown that the potential for track buckling represents a derailment risk in CWR territory. Longitudinal forces, which can be generated from multiple sources, but, especially, from thermal expansion, increase the risk of track buckling, particularly on hot days. If the track components designed to restrain longitudinal movement of the rail are unable to resist the dynamic longitudinal and lateral forces that are applied by passing trains, thermal misalignment or track buckles occur.
Direct sunlight and heat transferred from the wheels of braking trains are known to affect the rail temperature, although the degree to which has been speculative. After reviewing anecdotal and recorded data relating to sun kinks or track bucking incidents that occurred after multiple heavy trains on steep descending grades, CP Rail decided to measure actual rail temperatures, before, during, and after train movements to better understand the thermal effects of tonnage and braking, along with solar activity, on track-bucking potential.
The CP Rail study used 10 sensors placed in five pairs 200 feet apart in the web of the right and left rails on a 2% grade following a seven-mile descent. The sensors, which were located adjacent to a hot box detector to identify trains and provide data on the wheel temperatures, measured rail temperature every two minutes for two months through August and September. The test site also included a shaded portion beneath a highway overpass and an 8-degree curve in open sunlight.
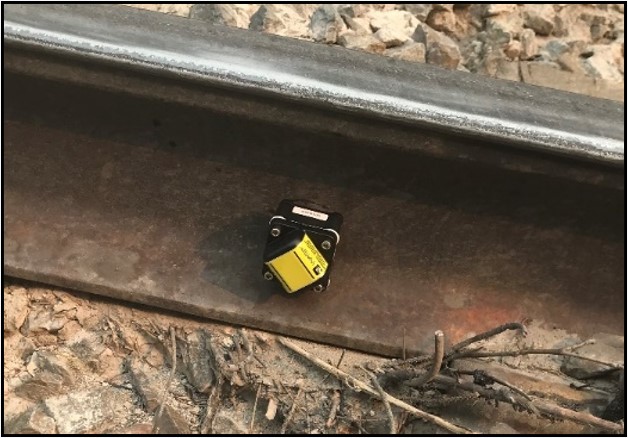
To no one’s surprise, the measurement data showed that rail temperature is influenced by sunlight and shade, that direct sunlight amplifies the heating effects and affects the time it takes the rail to “cool,” said Dylan Gareau, CP Rail’s the Manager of Track Design, Track Standards and Welding. On a day with a 98-degree F ambient air temperature, CP estimated that direct sunlight increases the track temperature by about 30 degrees. “This was verified with a rail temperature measurement of 127 degrees F,” he said.
The frequency of temperature measurement enabled CP to directly correlate spikes in rail temperature with each descending train that passed the test site. It was also able to show a direct correlation between train tonnage and increased rail temperature. Further to this, it showed that higher-tonnage trains also have higher wheel temperatures, which in turn increase rail temperatures, although not as directly as tonnage. “Heavier, descending trains brake more, which generate more heat,” Gareau said.
Back-to-back trains, in particular, generated dramatic increases in rail temperature. In one instance, three heavy potash and grain trains operating less than 30 minutes apart increased the rail temperature by 52 degrees. In another instance, two heavy potash trains 37 minutes apart also increased the rail temperature by 52 degrees. Conversely, no significant heating was noted from ascending or lower-tonnage trains. The majority of the train-generated heat dissipated within one to three hours, regardless of number of trains, Gareau said.
The highest temperate readings and increases from ambient temperatures came from the sensors exposed to sunlight. The highest rail temperature recorded during the study was 136 degrees F — more than 50 degrees higher than the 81-degree F ambient temperature. “We see that trains above 16,500 tons typically add 10 to 20 degrees of heat to the rail,” Gareau said. “These increases are typically amplified by upwards of 30 degrees by sunlight.”
On a day with a 98-degree F ambient air temperature, CP estimated that direct sunlight increases the rail temperature by about 30 degrees. “This was verified with a rail temperature measurement of 127 degrees F. Back-to-back trains added another 41 degrees of heat, pushing the rail temperature to 168 degrees F,” Gareau said. In one instance, a single train increased rail temperature 41 degrees. “These are higher orders of magnitude than we expected based on previous anecdotal experience.”
CP used the rail length, temperature differential, and the coefficient of thermal expansion to determine the extent of rail expansion in unrestrained rail. “This calculates to about 4 inches per 10 degrees of expansion within a mile, if unrestrained,” Gareau said. “This means that the track components are required to restrain up to 16 inches of thermal expansion from the trains, alone.”
The potential for track buckling in corridors in which trains operate on steep grades is compounded by two primary factors:
- Rising global temperatures: CP recorded the highest temperatures ever seen on the network in the summer of 2021.
- Increasing train tonnage: Technology and demand have led to steady increases in train tonnages on the network.
Solutions? Two of the more obvious approaches are to improve the track’s resistance to buckling by providing greater longitudinal rail restraint. Another is to increase the track’s neutral rail temperature, i.e., laying the rail at higher neutral temperatures. These are good, although costly and maintenance-intensive, options that CP is employing where appropriate. But CP is also looking at ways to mitigate risk by utilizing existing infrastructure, such as its network of 450 Hot Box Detectors to monitor ambient temperatures, and to target key parameters relating to the potential for track buckling, such as heavy grades, high ambient temperatures, and heavy back-to-back trains, and to use experience, technology, and optimized algorithms to generate alerts when warranted.
Effects of Operating Regimes on Track
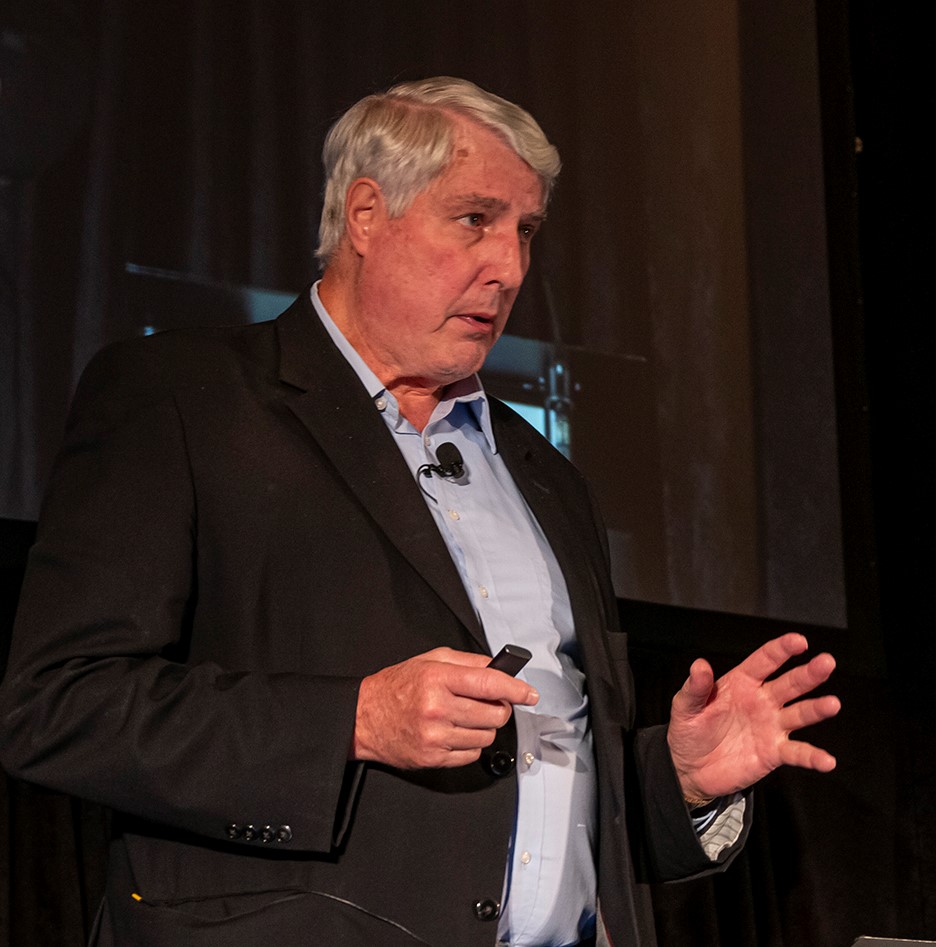
But CP Rail is not alone, when it comes to managing the unique challenges associated with operating longer, heavier, and slower trains in mountainous, heavy-grade, and high-curvature territories. Gary Wolf, President of Wolf Railway Consulting, and author of The Complete Guide to Modern Derailment Investigation, (see “The Complete Field Guide to Modern Derailment Investigation:” An insiders’ look into the definitive work by the industry’s preeminent derailment investigator), identified existing and potential issues relating to changes in operating and maintenance practices that he has observed through track inspection and derailment investigations, and provided a clinic on inspection and maintenance requirements in the current operating environment.
“The railroad system in North America has changed pretty dramatically in the past couple years,” Wolf said. Precision Scheduled Railroading (PSR) and its variants, which have been adopted by most of the Class 1 railroads, have led to a change in train lengths and speeds. In some cases, shorter and faster trains; in other cases, longer, heavier, and slower trains. In either case, one of the fundamental aspects of PSR is to do more with less — fewer cars, locomotives, yards, crews, staff, and less track, where it’s not needed. More specifically, PSR and its variants focus on:
- Fewer touches per car – less switching, more destination blocking
- Car performance; less on train performance
- Car/train velocity; less on terminal dwell
- Fewer unit trains; more complex blocking
- Optimizing network, not just single divisions/terminals
- Longer full-tonnage trains; filling out tonnage enroute
- Running on schedules; more predictability
- Less firefighting; knowing what to expect
- More flat switching; less humping
- Driving decision making to the local level; less bureaucracy
“The bottom line is that we’re doing more with less,” Wolf said. “But whenever you have higher utilization of assets, you’re going to have accelerated degradation of those assets. We have to understand that we’re putting more stress on fewer components, and that wheel and rail wear, ballast conditions, and other aspects of track are all going to change — dramatically, sometimes.”
The operational changes associated with PSR affect track maintenance, and they have the potential to affect the derailment causation. “Underscore potential, Wolf said. “I’m not saying this is happening. But I’m here to sound the warning that those of you involved in the track structure, track maintenance, or derailment prevention should be aware of these factors.”
As Bill Stephens pointed out in the November 2021 issue of Trains: “All of the Class I systems regularly operate trains that reach or exceed 12,000 feet. Systemwide averages on the big six systems range from a low of 6,900 feet at BNSF Railway to a high of 9,359 feet at Union Pacific, according to recent data. UP’s train length is up about 30% since late 2018, when it adopted a Precision Scheduled Railroading operating model. UP aims to get its average train length beyond 10,000 feet.”
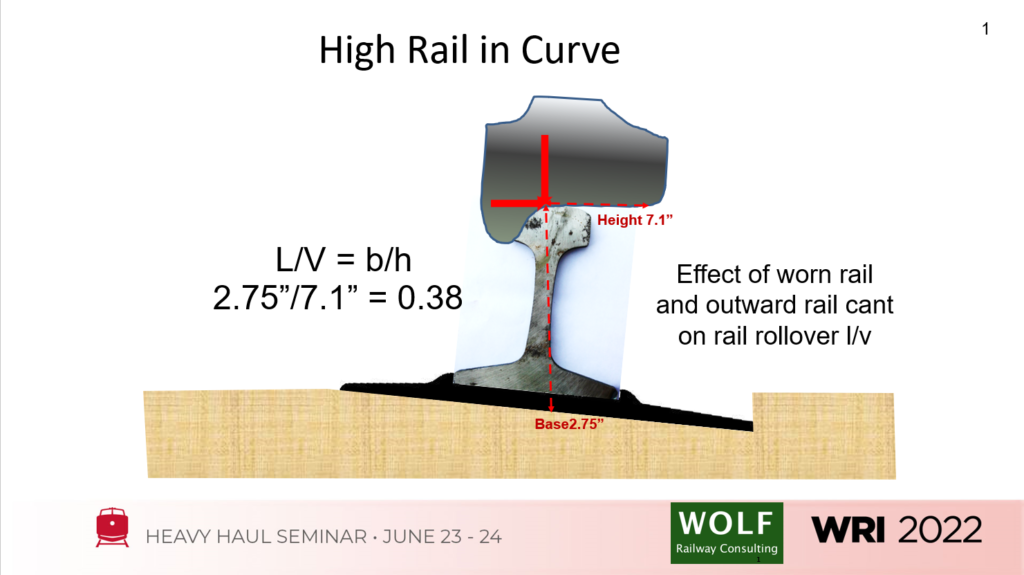
With longer trains comes higher tonnage. Concurrent with that, train speeds have declined industry-wide from an average of 25 mph to 20 mph over the past two and a half years, Wolf said. “Lowering train speeds by 5 mph can have a significant effect on lateral curving forces. As speeds decline, we may find that we have excessive elevation in curves. The superelevation that was set based on timetable speeds and operating practices 10 or 20 years ago may be dramatically different from what is required by operating parameters today.”
Improper rail cant, which can be caused by improper curve elevation due to changes in train speeds, can lead to differential plate cutting on timber ties. “This reduces the b/h ratio to initiate rail rollover, and ultimately will lead to greater risk of rail rollover, especially on the low rail side. Excessive plate cutting on the low side of the curve due to too much elevation can actually increase elevation and worsen the situation,” Wolf said.
Potential Impacts of PSR on Derailments and Track Maintenance
As CP Rail’s Dylan Gareau pointed out, longer trains put more heat into the rail, which can impact the effectiveness gauge-face lubrication and top-of-rail friction management retention rates, and factor into the potential for track buckling. Higher rail heat, along with additional wheel forces, may reduce the retentivity of greases and friction modifiers, causing less carry forward down the track. Maintenance forces need to closely monitor rail friction levels to make sure that gauge-face and TOR lubricators are properly spaced and that the material output rates are appropriate for longer, heavier trains, Wolf said.
Long, heavy trains can also generate dynamic slack effects that manifest themselves at the wheel/rail interface and are transferred into the track structure. “Braking longer, heavier trains on long downhill grades also generates more friction, which generates heat, which can increase rail temperatures,” he said. Brake pipe/trainline-related issues on longer trains can also cause sticking brakes, especially in cold weather, and wheel flats that generate high-impact loads into the rail and track structure.
Longer trains also require more horsepower, which can override the ability of rail anchors to prevent the longitudinal rail movement associated with traction and braking forces, which tend to push rail downhill on grades. “Inspectors have to pay close attention on ruling grades to see if the rail is moving through the anchors, dragging ties, or otherwise overstressing the anchor system,” Wolf said.
Research and findings from derailment investigations have provided evidence that the increased longitudinal (and lateral) loading associated with increased levels of traction have been a primary factor in broken spikes. “Investigations on Norfolk Southern, for example, showed a correlation between broken spikes and the introduction of high-adhesion AC locomotives on the territories where the spike breakage occurred,” Wolf said.
Other areas to monitor for potential effects of PSR include changing wear patterns on rail, fasteners, ballast, crossties, and changes in track geometry, as increases in drawbar forces due to bigger trains will exert higher lateral and vertical forces on the track structure.
“The bottom line is that operating precision and reliability cannot coexist with maintenance interruptions, disruptions, slow orders, signal malfunctions, derailments, and human failure,” Wolf said. “To operate a reliable, precision/scheduled network we must be vigilant and eliminate disruptions and outages.”
Findings from Derailment Investigations
But when things go south, as they invariably do at some point on every railroad regardless of the operating scheme, derailments occur. And when they do, investigators comb through the wreckage and operating and maintenance records, to identify the cause or causes. And under the right light, the findings yield lessons that can lead to operating, maintenance, or even regulatory changes. For a look into some of the lessons learned, Mike Roney, of Iron Mustache Consulting, examined two decades of derailment investigations by the Transportation Safety Board of Canada.
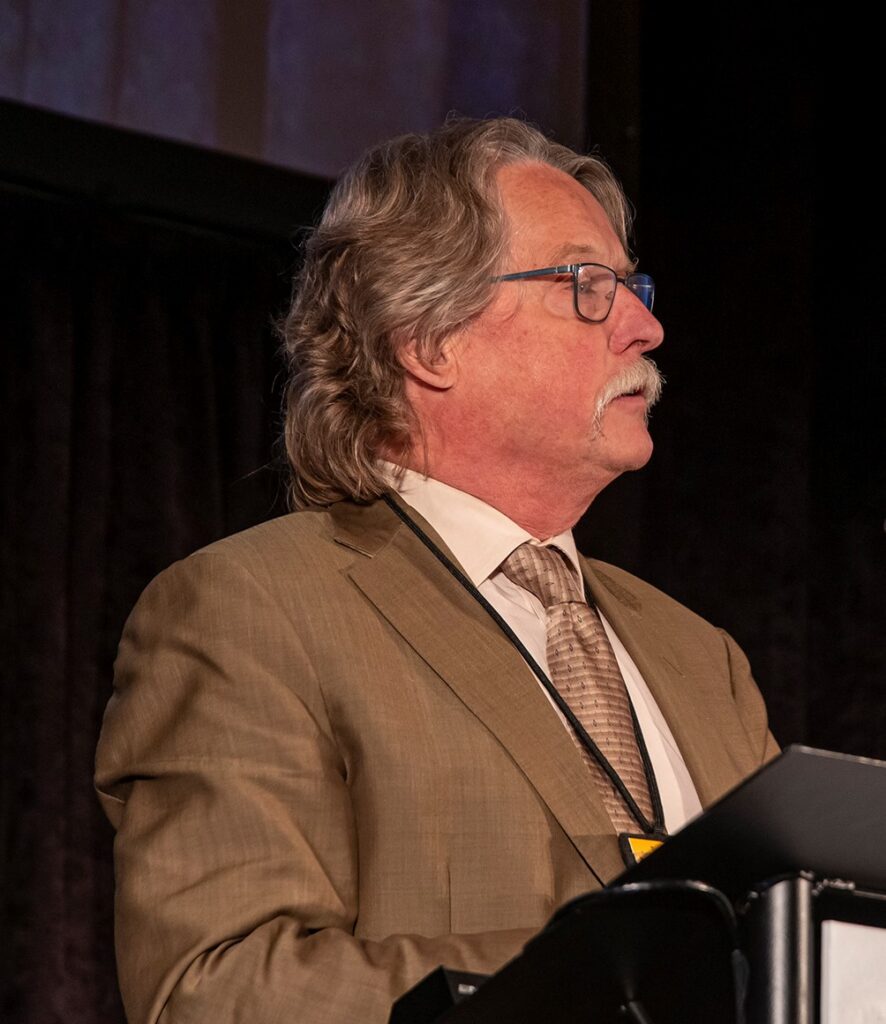
Roney, a former General Manager of Track and Structures, and Chief Engineer at CP Rail, who in 2019 was inducted into the International Heavy Haul Association’s Heavy Haul of Fame for his “lifetime vision and dedication to the advancement of heavy haul railroad technology, engineering and operations,” examined derailment incidents through the lens of the TSB investigators and through the corrective action plans that were provided in response to the TSB’s findings.
“Twenty years of derailment investigations by the Transportation Safety Board of Canada is a story about how knowledge is advancing and how we are making it work for us,” Roney said. “It’s also a story about how there has been collaboration between railways and the regulators to make things better.”
The Transportation Safety Board of Canada (TSB), like the National Transportation Safety Board (NTSB) in the U.S., is an independent federal agency that is there to advance transportation safety by investigating occurrences in air, marine pipeline, and rail. The TSB selects and investigates derailments to determine the cause of incidents that might indicate a trend or indicate a risk to the public. The TSB reports identify the factors that caused or contributed to the occurrence, and the safety deficiencies that need to be addressed. While the TSB does not have a mandate or authority to implement corrective actions, it monitors recommendations and actions of Transport Canada and the railways for mitigating actions that eliminate or reduce the so-called safety deficiencies found in these investigations.
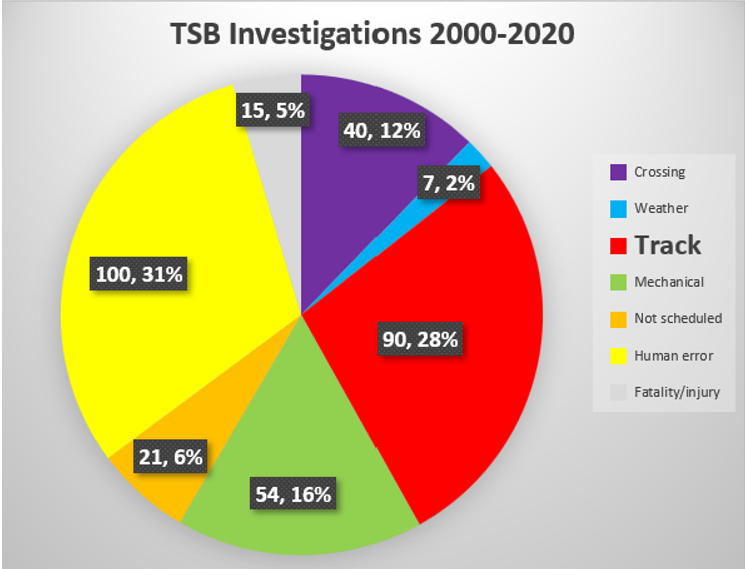
Overall, the TSB investigated 327 derailments between the 2000 and 2020; 90 derailments reflecting 28% of the total derailment costs identified a track issue as a primary cause; 100 derailments reflecting 31% of the costs were attributed to human factors; 58 derailments reflecting 16% of the costs were attributed to a mechanical-related cause.
The majority of the track-related derailments (49%) were attributed to three causes: broken rails, broken joint bars, and broken welds. The remainder were attributed to wide gauge (17%), track buckles (12%) wheel climb and rail rollover (10%), geotechnical-related (7%) and geometry defects, other than wide gauge (5%). “That’s actually a very good result for the track geometry departments,” Roney said.
Thirty five derailments in this sample identified broken rail as a primary cause; 21 of the derailments, the majority of which were prior to 2015, resulted from undetected internal flaws. The four major derailments that were investigated in 2002, for example, had defects that TSB determined should have been detected by a rail flaw detector car if it had the right instrumentation, if it had been run frequently enough, and if rail surface conditions such as rolling contact fatigue had not blocked or interfered with the ultrasonic signal.
“A lot of the early broken-rail derailments were characterized as detectable,” Roney said. In 2015, two out of the three should have been detected. In 2019, one of four should have been detectable. The positive trend, particularly since 2015, indicates that railroads have done a better job of ferreting out defects that are detectable with ultrasonic inspection.
A TSB study showed that mainline derailments as a whole decreased by a factor of three between 1980 and 1988 (although the downward trend flattened out between 1988 and 1993). The TSB attributed the reduction in derailments between 1980 and 1988 to improved installation and repair of CWR and increased use of automated rail defect detection and track geometry measurement technology. “I would add that replacement of older rail steels with cleaner steels rolled in 1985 or later also had a positive impact,” Roney said.
Rail grinding, particularly the conversion from corrective to rail profile grinding, was another important part. Joint elimination and the movement away from standard carbon rails to intermediate grade rail steels in tangents and light curves, and premium head-hardened rail in sharp curves were also important, he said. “Improved steelmaking has reduced the indications of tensile residual stresses in the rail web, and there is less clustering of transverse defects than in the past. And when they occur, rail breaks have tended to be cleaner breaks, which are picked up by the signal system before a train finds them.
“Advancements in internal rail defect detection and more frequent ultrasonic testing – moving from 25 million gross tons (MGT) to 5 MGT testing intervals , in particular, has been a big factor in reducing the number of broken rails,” he said.
The TSB identified wide gauge as a primary cause in 13 derailments over those 20 years. They also indicated that in five of those derailments, poor inspection practices missed things that should have been seen. “Granted, some of them were wintertime inspections during which inspection was difficult and there was no visible indication in the snow that the rail was spreading,” Roney said. “Nonetheless, the circumstances led us into corrective actions, such as use of gauge-restraint-measurement systems, which are very effective at finding hidden and dynamic instances of wide gauge.” The data shows that 85% of the wide-gauge derailments that were investigated occurred in 2012 or earlier. There were no major derailments between 2013 and 2016; only one in 2018 and one in 2020 — a dramatic improvement in preventing wide-gauge derailments, he said.
A revision to the track safety rules by Transport Canada in 2012 increased the requirements for track geometry testing, and spurred railways to increase light geometry testing on lighter used lines and some yard tracks. The problematic gauge areas identified as a result has also likely had an impact on the reduction in wide-gauge derailments.
During the 20-year period in question, there were 11 track buckle derailments. “Not surprisingly, track work had been performed at the time of or just prior to the derailment in seven of these cases. It’s likely that the rail had not been properly de-stressed before a tie gang moved in and disturbed the track,” Roney said. Four of the derailments noted insufficient or inadequate anchors and poor tie condition as primary factors. “The good news is that there was only one investigation (in 2019) of a major track buckle derailment.”
The TSB issued a safety recommendation in February 2003 concerning the need to de-stress continuous welded rail. Work done by the TTCI (now MxV Rail) in Pueblo showed how track reacts before and after tamping, and how neutral temperature tends to drop over time as track is disturbed. They also provided very good information on how long a rail needs to be unclipped to do a proper destressing, he said.
With a push from the Federal Railroad Administration, railroads developed common standards for CWR management, which included measuring rail temperature, measuring the gap or bypass every time rail was cut, guarding areas that were particularly at risk of track buckling, and de-stressing the rail before doing major programs or before the weather got hot. With significant portions of their networks in the U.S., Canadian National and Canadian Pacific adopted the collaborative CWR standard.
Six of the derailments that the TSB investigated cited rail rollover as a primary cause. Also identified were: poor tie condition; train handling was noted in three derailments; high l/v ratios in two derailments; and a binding truck in one derailment. Also noted was the effect of the b/h ratio in rail rollover; that the location of the primary contact band of the rail is an important factor; and that wheel/rail conditions such as flat rail heads with hollow-worn wheel treads coupled with wide gauge reduce the b/h ratio and move the contact beyond the base of the rail and start the rail rollover.
CN and CP have installed truck performance detectors to detect higher l/vs from bad actor cars as part of their corrective action plans. Both railways established programs to identify locations where the design superelevation in curves didn’t match the current operating speeds of longer, heavy trains.
Applying the Lessons Learned
“We all know that the rails speak to you,” Roney said. “When the gauge face of the high rail is wearing rapidly and the plates are cutting on the field side, the curve is under elevated. And if the low rail shows heavy, mushrooming RCF, it’s likely over-elevated. A good understanding has been developed on how to balance those.”
The TSB expressly states that it’s not its function to assign fault, so they don’t address the faults of an individual inspector’s ability. “But in looking at some of these incidents in which the issues are pretty obvious, you have to scratch your head and say, ‘what was he thinking?’ That was pretty obvious.” Roney said. (See Understanding the Role of Human Factors in Railway Inspection.)
The TSB indicated that poor training was a root cause of 12 of the 90 track-caused derailments it identified.
“After going through these derailments and looking at the training intervals versus a given derailment, we found little relationship between risk and manual inspection frequency: Roney said “But we did think there was something relating to training aptitude versus competency assurance. If we rely on a sole inspector in a critical territory to make all the right decisions, is that the right thing? Or do we need management oversight? Do we need competency assurance by having proficiency tests on that inspector?” he asked. He noted that CP had instituted a ‘ride with the inspector program,’ several years ago in which managers were required to go out with the inspectors to “see if their eyes saw the same things.” Another initiative was to establish electronic record keeping so managers could look in on inspectors to see what they were and what they were not finding.
Opportunities for improvement include the ability to:
- better identify disturbed track risks in advance of track work
- target rail neutral temperatures to strike the right balance between the frequency and consequences of track buckles vs. broken rails
- improve understanding of geotechnical and water management hazards to better anticipate extreme weather hazards
- employ mentoring and quality control of manual visual inspections, which is more effective than training
- Increase inspection frequency when tonnage rapidly increases on jointed track
- Better define combination track geometry defects
- better identify the risk of rolling contact fatigue
Some opportunities for improvement have been incorporated into Transport Canada’s latest rules respecting track safety. These include a new maximum time intervals between rail for detection tests that are defined by tonnage and track class. Track geometry test cycles are now defined for light and heavy geometry inspection vehicles. Quality assurance of track inspection and maintenance activities is now required, and a professional engineer must sign off on CWR management and rail wear management plans, Roney said.
“In the future, we’re going to have better integration of automated inspections and manual validation follow up. There’s an opportunity to get away from biweekly manual / visual inspections and replace them with more effective frequent automated inspections. The inspection regime could be better tailored to the risk profile, the combination of track condition inspection capabilities and traffic mix,” he said. “We’ll need to continue working on lowering the vehicle/track interaction stress state. And we’ll need an escalation of what we do for maintenance and renewal action, based on predictive algorithms.”

Bob Tuzik is Editor-in-Chief of Interface Journal.
This article is based on presentations made at WRI 2022.