Managing Slack in Trains with Cars Equipped with Hydraulic End-of-Car-Cushioning Devices
by Jeff Tuzik
Among the most significant forces that freight railroads contend with in daily operations are buff and draft (or compressive and tensile) forces between cars within train consists. These forces are mediated by various damping technologies, braking and acceleration practices, and by train make-up. When these forces aren’t managed properly, the consequences can range from damaged couplers to derailed trains.
A few technologies are used to help control buff and draft forces between cars and to mitigate the effects of yard impacts. Draft gear is designed to absorb impacts between train couplers. The earliest and simplest friction draft gear operates by pushing friction shoes against wear plates during compression to absorb energy, and then returning to neutral via spring force, Jonathan Sunde, Chief Engineer – Draft and Brake Systems at Strato, Inc., told delegates at the 2023 Wheel/Rail Interaction conference. More modern polymer draft gear works on a similar principle but uses non-metallic spring sets to return after compression. “These polymer-type springs can absorb significantly more energy than steel-type springs on the compression and release strokes,” Sunde said.
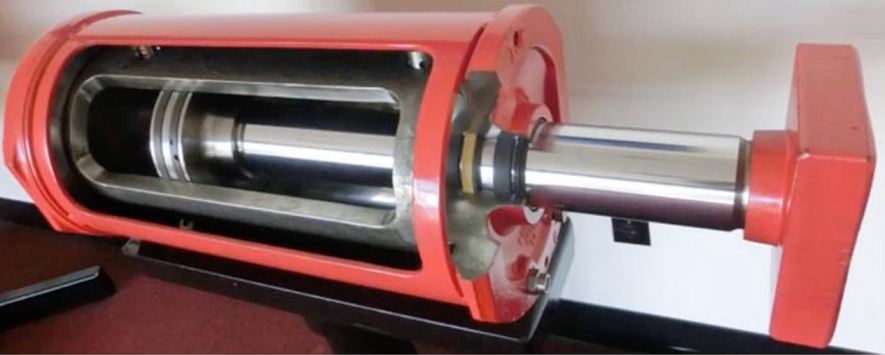
Hydraulic end-of-car-cushioning (EOCC) devices represent a more modern and versatile approach to buff-force mitigation. EOCCs are designed such that their pre-load (the force required to begin compressing the piston) can be adjusted based on their intended use. “[EOCCs] are purpose-built for yard impacts — the very long stoke allows for significant energy absorption,” Sunde said. These are installed on cars in which impacts could shift or damage lading, typically: multi-level, coil steel, center-beam and bulkhead flat cars, and boxcars.
Auto racks, or multi-levels, typically have a preload of 50,000 lbs and a stroke or compression of 10 inches. Other cars typically have a 100,000-lb preload and a 15-inch stroke, said Brad Kerchof, former Director of Research & Tests at Norfolk Southern and senior consultant to Advanced Rail Management / Global Rail Group. Because EOCCs are mounted on both ends of a given car, the effective compression between two cars is twice the piston stroke length. Among these types of cars, multi-level and coil steel cars tend to derail more frequently, Kerchof said. One reason for this is that these two car types tend to run in large blocks, and as the number of cars with EOCCs increases, so does the amount of slack available in the consist.
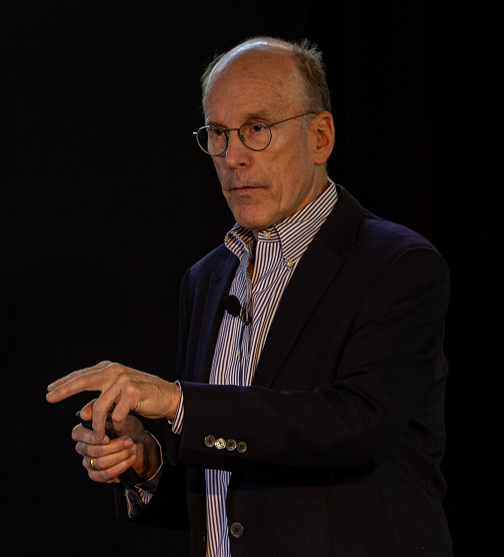
While both the compression and return strokes of an EOCC are hydraulically damped, there is also a varying amount of free slack inherent to these systems, and free slack can worsen as units age. Even couplers themselves typically have roughly ½ inch of free slack due to the nature of their design, Jonathan Sunde said.
As buff and draft forces act on the slack within a consist, be it free slack or EOCC slack, a number of adverse effects — from component failure to derailment — can result. The derailments and subsequent investigations of two specific Norfolk Southern trains (trains 18N and 22Q) illustrate how slack interacts with various operational conditions, and how such catastrophic events can be avoided.
Train 18N
Train 18N consisted of 107 multi-level cars equipped with EOCCs. Its total length was 10,331 feet and the total EOCC slack in the consist was 178 feet. “This means that the difference in this train’s length between its compressed and uncompressed state was about two car lengths,” Brad Kerchof said.
When the head end of train 18N reached the bottom of a 1.8% descending grade, the engineer released the air brakes, resulting in a gradual increase of the head-end speed. But due to the nature of air brake systems, it took some time for this increase in brake pipe pressure to travel the length of the train. A service (non-emergency) change in brake pipe pressure travels at 600 feet per second. For a 2-mile-long train, a pressure change takes 17 seconds to travel from head to rear, he said. This meant that for a number of seconds, while the head end had brakes released, the rear end had brakes still applied.
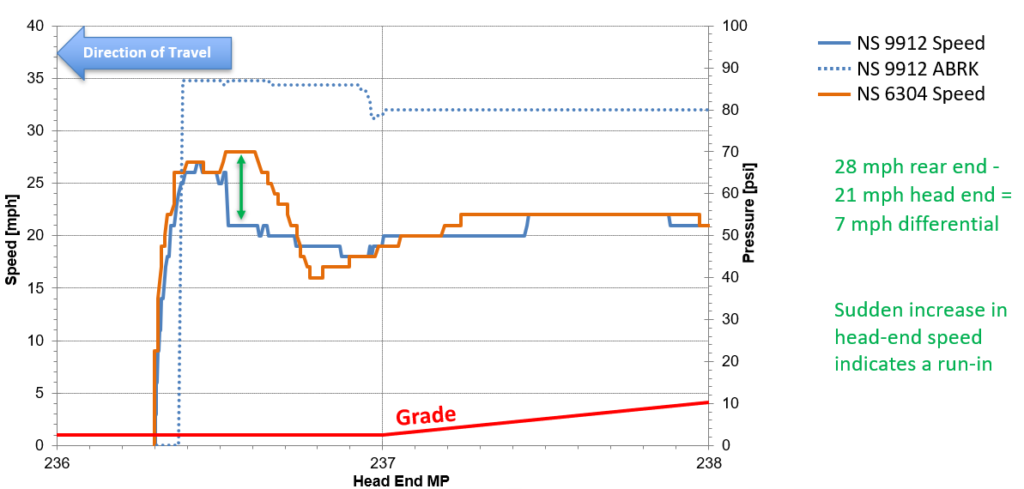
This non-uniform train operation (the head-end gradually accelerating and the rear-end helper locomotive still braking) caused the train to “stretch.” When the rear-end brakes did release, the portion of the train still on the descending grade began to accelerate quickly, an acceleration that was facilitated by a train-length of uncompressed EOCCs. As the chain of EOCCs compressed, the rear end ultimately reached a peak speed of 7 mph faster than the head-end. Once the last EOCC was compressed and there was no more slack available, this speed differential resulted in an impact force, or run-in, sufficiently large to buckle the train and derail 15 multi-levels.
The official cause of the derailment was attributed to “improper release of the air brakes on a descending grade, allowing the stretched train to run-in,” Kerchof said. In addition to determining the cause of the derailment, the investigation committee also recommended that in order to prevent future derailments of a similar type, the engineer should delay release of the air brakes until half the train is off the descending grade. “This was instituted in 2014, and there haven’t been any problems since,” he added.
Train 22Q

Train 22Q consisted of three locomotives on the head-end followed by 70 cars, including loaded double-stacks and loaded and empty multi-levels, for a total length of 10,194 feet. The tonnage profile of the consist was such that 41 multi-level cars — with a total of 68 feet of EOCC slack — were sandwiched between a group of 17 doublestacks on the head-end and 12 doublestacks on the trailing end.
The train was on an undulating grade. The bulk of the consist had crested a hill and was on a descending 1.2% grade. As the rear doublestack block crested the hill and began its descent, the weight of these trailing cars, combined with the grade, generated an 80,000-lb. compressive force against the mid-train multi-levels. With a preload of 50,000 lbs., the multi-level EEOCs compressed until there was no slack available. “Think of the EOCC-equipped cars as a slinky, and the trailing doublestacks as a bowling ball,” Kerchof said. Once the rear doublestacks started moving down the grade, the “slinky” was overcome by their combined mass. As with the 18N derailment, the resulting impact force, or run-in, was sufficiently large to buckle the train. Twenty multi-levels derailed.
The derailment investigation team modeled the in-train forces by feeding track, equipment and locomotive engineer command data into a TOES (Train Operation and Energy Simulator) simulation to pinpoint the precise coupler forces that triggered the derailment. “We concluded that this train was destined to derail,” Kerchof said, adding that the TOES modelling indicated that no accepted train-handling practices could have prevented a derailment-causing run-in.
These examples highlight the importance of considering train make-up in addition to other factors when it comes to operational best-practices; the number and placement of EOCC-equipped cars, the combined tonnage trailing a block of EOCC cars, and braking practices on a descending grade can all be directly involved in causing or preventing a derailment. And one of the key take-aways from these investigations and other buff and draft force analyses is that regardless of other variables, large blocks of hydraulic EOCC-equipped cars are inherently subject to higher buff and draft forces than cars using other draft systems, Strato’s Jonathan Sunde said.

Jeff Tuzik is Managing Editor of Interface Journal
This article is based on a presentation made at Wheel-Rail Seminars’ 2023 Wheel/Rail Interaction Conference.