Running Longer Trains More Productively and Less Destructively
by David C. Lester
Dave Peltz is literally a rocket scientist. Although he is now Chief of Global Technology for GE Transportation’s (now Wabtec’s) Intelligent Control Systems Division in Melbourne, Fla., he spent time with the U.S. Air Force as a satellite communications systems engineer for the Mill Star satellite system, the military’s primary nuclear war communication system, and reinvented radio network protocols and control algorithms for nuclear missile retargeting commands. Later, he worked at the Cape Canaveral Air Force Station on the testing and launch of the space shuttle and Titan rockets. Dave has been with GE Transportation (now Wabtec) for 17 years and has worked on Wabtec’s LOCOTROL, distributed power, remote control locomotives, Trip Optimizer energy management system, and ECP brakes. Obviously, Dave is well-qualified to discuss how to run longer trains more productively and less destructively.
More Productively
One of the tenets of precision scheduled railroading is the practice of running longer freight trains. During the past 30 years or so, average freight train length on Class 1 roads has been around 5,000 to 7,000 feet, or about a mile to 1.5 miles. And, on several occasions in the past, railroads have tried to make their service more flexible and responsive to customer needs by running short, fast trains (particularly intermodal), but these trains usually lacked sufficient traffic to make them profitable, among other challenges.
Wabtec’s LOCOTROL and Trip Optimizer products have made it practical to run long trains efficiently. The idea behind running longer trains, often 10,000 ft (almost two miles), 12,000 ft (2.5 miles), or 18,000-20,000 ft (> 3 miles) is they cost less. Considering that a three-mile-long train is, essentially, three “normal” sized ones and that it can be run with one crew, the railroad has to pay only one crew instead of three. Fuel savings are realized, too, and proponents say that productivity is improved, the network is less congested (thereby increasing capacity), and disruption to communities through which trains operate is reduced.
As one can imagine, trying to run a three-mile-long train with all of the power on the front end would end in disaster. That’s where distributed power (DP) comes in. Distributed power enables a long train to run more efficiently and easily. The typical lineup for DP is two units at the front of the train, two in the middle, and two at the rear. When the engineer increases power, all of the locomotives respond, and slack action is minimal. The long train is essentially moving as a single unit, despite its length.
Regarding fuel savings, Peltz reports that LOCOTROL and distributed power enabled Canadian Pacific Railway to realize 6 percent fuel savings over four years with distributed power, while Union Pacific saw a savings of 5 percent over five years. Canadian Pacific also saw a 10 percent increase in total tonnage hauled, and an 11 percent reduction in train starts since it was able to move the same total number of cars using longer, but fewer trains.

Another significant advantage of DP is that the braking of the train is much less stressful, as each of the locomotives has an air reservoir that pumps air into the brake pipe for the cars between it and the next locomotive. Those who are opposed to equipping freight trains with costly electronically controlled pneumatic brakes (ECP) point out that the same braking effect can be achieved with DP. Peltz says, “distributed power with three remote locomotives offers the same performance as ECP braking.” Just as the entire train starts as a single unit, DP allows it to stop as a single unit, minimizing or eliminating slack bunching as the train slows.
Trip Optimizer is another Wabtec product that uses algorithms to improve train handling based on what is being optimized (i.e., fuel consumption, time, or handling characteristics). This system develops and executes a plan that considers a variety of variables to manage speed, throttle settings, slack action, and other parameters in ways that a human being cannot, according to Peltz. Upon receiving or learning new data, Trip Optimizer can rapidly calculate which variables in the plan need to be changed to accommodate this data.
For example, if Trip Optimizer learns that a meet with another train has been arranged, and the system is given a time for the meet, TO will adjust the speed to meet the opposing train at the correct location and at the correct time. This enables the opposing train to continue its journey as it passes the TO train, preventing the need to go into a passing track and stop, which saves a tremendous amount of fuel because, as most readers know, starting a train from a full stop and getting back up to track speed requires significant fuel burn.
Less Destructively
Rail wear is reduced through the use of distributed power. Peltz cited work by Jude Igwemezie on the effect of slack action and dynamic train activity on track (see Understanding Stresses in Rails Parts 1 and 2 ), and reports that in one case, in particular, a section of track in California was wearing too quickly. This section was on a superelevated curve, and both coal trains and passenger trains ran on the line, but neither was traveling at the superelevation speed. The forces from coal trains traveling at under the balance speed were wearing out the low rail, while the forces from passenger trains traveling at above the balance speed were wearing out the high rail. As a result, this section of track had to be replaced every year. Once the railroad began using distributed power over this line, they were able to operate coal trains at or near the balance speed, and by doing so, found that rail wear was reduced by 80 percent. This meant that the life of the rail on this section was extended from one year to five years.
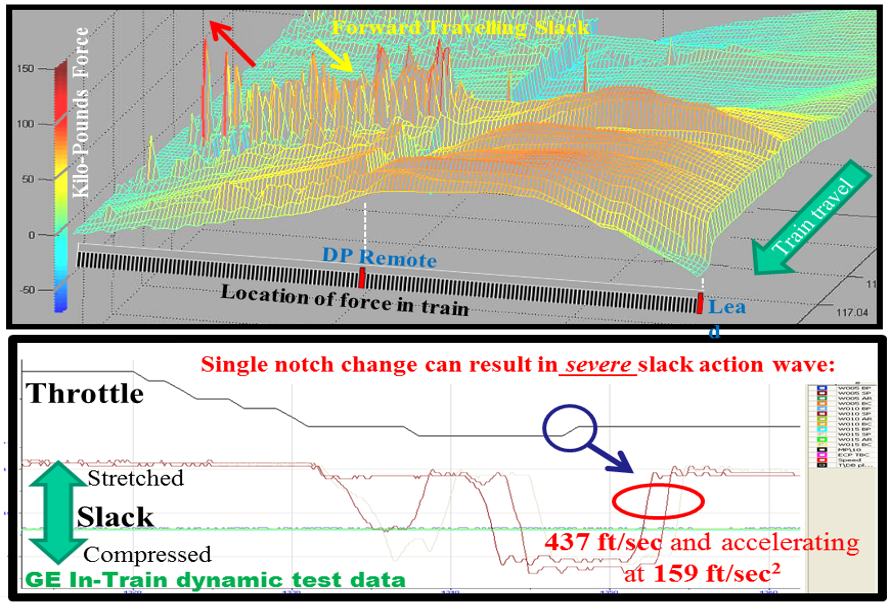
Slack action can also be significantly reduced with DP. As most readers know, locomotives have typically been placed at the front of trains. All of the pulling force on the front end can result in significant slack action. Few who have been around railroading for a long time haven’t been at the mid-point or rear of a freight train starting to move, when the engineer opens the throttle just a bit too quickly, resulting in slack action that almost sounds like a series of bombs exploding. Trains can break apart if the slack action is too heavy at start or during running.
Peltz’s research shows that if all of the power is located at the front of the train, even a single notch change of the throttle can result in severe slack action. Unconstrained slack (with no locomotive at the rear of the train) is particularly problematic.
“We measured with my data logging equipment some of the waves of slack through the train at nearly the speed of sound,” Peltz said. “Without a locomotive at the end, they were getting frequent break in twos where they were snapping the last four cars off the train.” Having multiple locomotives throughout the train will stop that slack from propagating throughout the train and causing fatigue damage to the knuckles, he said.
Distributed power effectively manages and reduces slack action if locomotives are placed on the front, in the middle, and at the end of trains. Locomotives on the rear of the train are particularly important. This is because locomotives significantly resist slack action, as they are not going to be pulled forward by the slack. Plus, since all locomotives are presumably at the same throttle setting, the entire train will be moving as a unit instead of only being “pulled” by locomotives on the front end.
Since TO has the track profile loaded into its database, it is effective in determining where to apply top-of-rail friction modifier. TO assumes that the friction modifier is dispensed from the locomotives or from somewhere on the train. Tests have shown that when TOR friction modifier is on, the top of rail is 20 to 25 degrees cooler than when it is off.
Trip Optimizer is also useful for trains running in undulating territory. The system can control the buff and draft forces throughout the train by managing the throttle settings of each DP locomotive as a train crests a hill, with part of the train going downhill, part going uphill, and part on track that is flat (i.e., little or no uphill or downhill grade).
While working with a Chinese delegation to help them determine how to use and realize the benefits of distributed power, Peltz and his team took the delegation to South Africa to demonstrate how freight rail service in that country leverages DP. They observed the operation of an ore train that had a mix of diesel and electric DP, which was able to communicate throttle settings to the diesel and the electric locomotives concurrently and individually. The train, which was actually three trains operating together, hauled 42,000 tons of iron ore. It was controlled by a single driver in the lead. “Trying to do this with multiple small trains would have required four times the crew to drive the individual trains,” Peltz said. Doing it with one train dramatically increased throughput, requiring fewer crews to run the same amount as commodity.

All images courtesy of GE Transportation / Wabtec Company.
This article is based on a presentation made at the WRI 2019 Heavy Haul Conference.
David Lester is Managing Editor of Railway Track and Structures.