An Introduction to Rail Grinding on the Delhi Metro
by Jeff Tuzik
Rail transit properties around the world all contend with the same general issues. The corrugation on track in San Francisco is the same as corrugation on track in New Delhi. There may be a few different details, but the physics is constant. When it comes to addressing surface defects like corrugation, rolling contact fatigue (RCF), spalling, and more, rail grinding is another constant. The Delhi Metro Rail Corporation, a relatively young transit system in India, has found recent success implementing a rail grinding program with both corrective and preventive elements.
Delhi Metro Rail Corporation (DMRC) operates 390 km of track in and around New Delhi. A joint venture between the Government India and the State of Delhi, construction began in 1998, and revenue service began in 2002. The DMRC operates 12 lines of track, four of which are broad-gage (5 ft 6 in or 1.676 m) and eight of which are standard gage. With an annual ridership of 2.37 billion, DMRC is the fourth most heavily trafficked rail transit system in the world. As is the case in many transit systems in densely populated cities (particularly older cities), DMRC track has a lot of curvature. “Across all lines, sharp curves [500 meter radius ( > 3.5 degree) or less] make up 40% to 60% of the system,” Ashwani Kumar, DMRC’s Executive Director of Track, told delegates at the WRI 2023 Rail Transit conference.
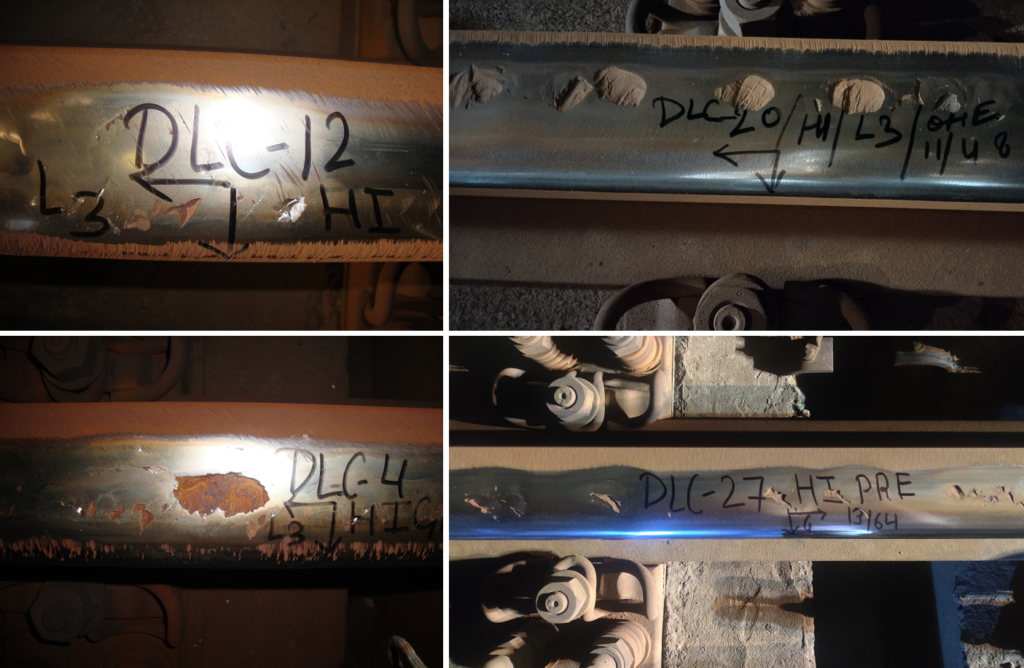
The DMRC’s 12 lines were all laid with premium head-hardened rail (UIC 60, 1080 grade) sourced globally — notably through Evraz, Voestalpine, and Nippon Steel. Despite the quality of the steel, DMRC noticed rapid accrual of surface defects including corrugation, RCF, studs, pitting, and spalling, in the first two years of operation, Kumar said. “Based on our projections, we estimated that the rail in curves would have to be replaced within 12 years, if conditions didn’t improve.” The prospect of replacing so much premium rail so early was financially and logistically untenable. To avoid this, the DMRC had to quickly develop and implement an aggressive corrective and preventive rail grinding regime.
India’s rail traffic generally operates on broad gage; (this is, coincidentally, the same track gage used on San Francisco’s Bay Area Rapid Transit) and expertise from that field influenced the design and construction of the earliest DMRC lines. These lines, in fact, once connected to freight lines at some interlockings, but no longer do. Ease of procurement and wide international support for standard gage led DMRC to switch to standard for the rest of the metro construction, Kumar said.
Because they operate both broad and standard gage lines, the DMRC needed a grinder that could move between the two with relative ease. This led them to Loram Maintenance of Way, from whom they purchased a 16-stone grinder and a four-year operations and maintenance support contract (provided by Loram’s partner Vandhana International Pvt Ltd, India). This operations and maintenance partnership has been extended several times and exists in this configuration today, he said.
The DMRC also worked with Loram to determine optimal grinding frequency for their tangent track and mild/sharp curves, based on MGT. This worked out to every 27 months on tangent, 18 months on mild curves, and 9 months on sharp curves for lines with less than 25 MGT annually. For lines with higher MGT, the determined frequency was 18 months tangent, 12 months on mild curves, and six months on sharp curves, Kumar said.
Like most transit systems, the DMRC has very limited maintenance windows — typically four hours per night — which, due to travel time and logistics, can often mean a grinder only gets only 60 to 100 minutes of actual spark time. Rather than focus on heavy corrective spot grinding, the DMRC initially aimed to use their maintenance windows to cover the system broadly, with a focus on corrugation and RCF removal, trusting that subsequent cycles would bring the rail profile closer to the target. Kumar also noted that the broad-gage lines tended to have generally more wear and surface defects, but that the root causes for this are not fully understood at this time.
The grinding program that DMRC and Loram developed also included a measurement component; they selected multiple representative track locations in tangent and curved track to take pre- and post-grind profile measurements. These measurements, which indicate the amount of metal removed by the grinder and the differences between the pre-grind, post-grind, and target profiles, form the basis of a Grind Quality Index (GQI).
“At first, we saw the GQI steadily improve after each grinding cycle, before becoming flatter as the rail profile was corrected,” said Venket Rao, Senior Vice President of Vandhana International PVT. LTD. This is also an indication of moving from a corrective grinding mode to a preventive grinding mode. The DMRC saw immediate improvements in wear rates and defect growth rates after only the first cycle, Rao said. The DMRC continues to operate this grinding program today.
Owing to the positive results of the program, the DMRC purchased another 16-stone Loram grinder in 2017. This machine is now dedicated to broad-gage lines, while the other handles standard gage. The doubling of grind capacity has also enabled the DMRC to get closer to their target grind frequencies, although narrow maintenance windows continue to be the limiting factor in the operation.
The DMRC is currently working with the data they’ve collected to determine the quantitative rail life increase they’ve achieved since the grinding program was implemented in 2009. Preliminary data obtained from MiniProf measurements indicate that natural wear on tangent track, and mild and sharp curves has been reduced since the grinding program was initiated.
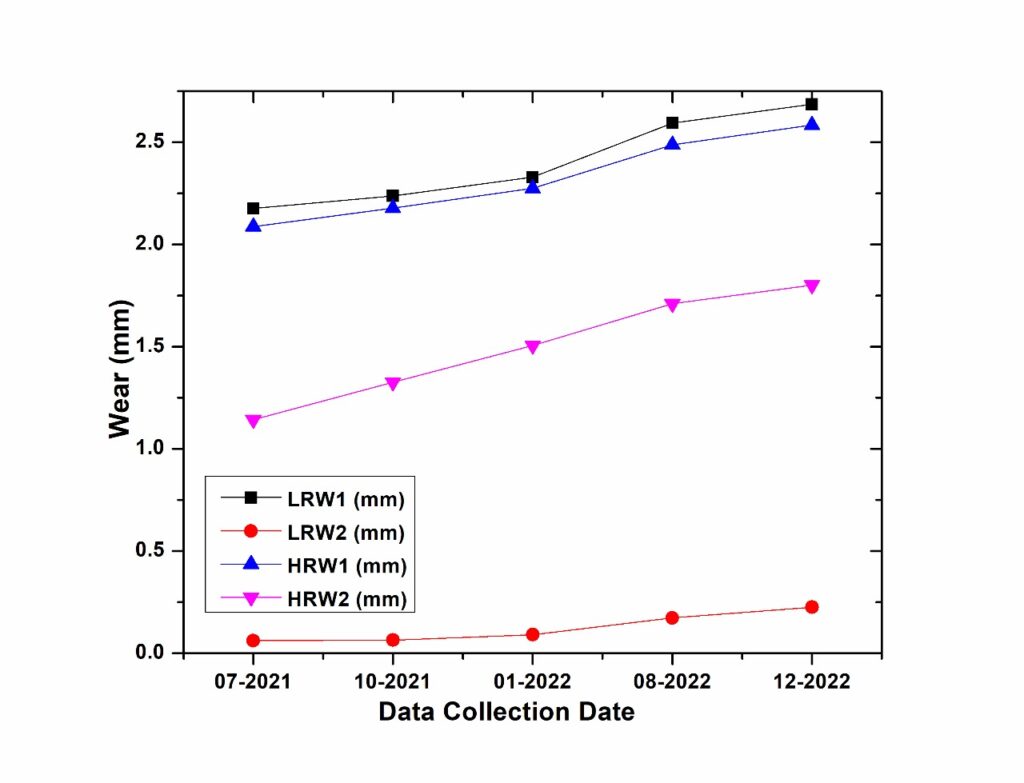
“We know that the rail has improved greatly in terms of surface condition, but we need more data still to be confident about rail life results,” Rao said.
Measurements and GQI data also indicate that shape of both right and left rail profiles are better matched and closer to the desired profile, which has led to better wheel/rail dynamics, which has reduced wheel wear.
While the current rail grinding strategy is yielding positive results, DMRC realizes that due to its limited maintenance windows, more innovative efforts will have to be implemented to maximize the potential of its grinding program. As DMRC continues to accrue rail grinding data and experience, they expect to see further year-over-year improvement in grinding production, rail wear, and surface defect growth.

Jeff Tuzik is Managing Editor of Interface Journal.
This article is based on a presentation made at the 2023 WRI Rail Transit Conference.