WRI 2015: Transit — Maintenance and the State of Good Repair
By Jeff Tuzik
Maintaining a state of good repair (SGR) weighed heavily on the minds of those in attendance at the 2015 Rail Transit Wheel Rail Interaction Conference, as transit properties will be required to meet requirements established by the Federal Transit Administration as early as next year. SGR – a state in which assets function to their purpose – is influenced by a long list of design and maintenance decisions made throughout the life of a system. The ramifications of these decisions often play out at the wheel/rail interface. Speakers at WRI 2015: Rail Transit examined the full purview of SGR – from data collection and analysis to maintenance planning and implementation – and presented a map to navigate the state of good repair.
The first step to maintaining a state of good repair is knowing the condition of the system. The Washington Metropolitan Area Transit Authority employs two types of automated inspection vehicles to monitor the condition of its track and structures; the Track Geometry Vehicle (TGV) and instrumented revenue vehicles, which provide different but complementary approaches to automatic track inspection.
The TGV measures a wide range of track geometry parameters and produces detailed reports identifying locations at which conditions do not meet WMATA’s maintenance and safety standards. The TGV is equipped with high-resolution cameras to inspect the right-of-way and tunnels, infrared cameras to monitor surrounding temperatures, and an ultrasonic rail flaw detection system to identify potentially dangerous internal defects. The vehicle also measures track gauge, alignment, cross level and rail profile. Since WMATA uses automatic train control (ATC), the TGV also inspects rail circuits and transmitters.
The newly introduced Kawasaki 7000 (7K) series revenue service vehicles are instrumented much differently and take a different approach to automatic inspection. The 7K Series, which operates in 4-car consists, employs a series of accelerometers and ENSCO’s Vehicle Track Interaction dynamic monitoring system (V/TI), with the primary goal of identifying poor track conditions and ride quality issues. Each of the 7K’s accelerometers (mounted on the car body, truck and axles) has a specific threshold and any event that exceeds that threshold generates an exception. The deployment of the 7K car series is recent enough that ENSCO is currently in the process of fine-tuning the precise exception thresholds.While the 7K Series lacks the depth and detail of measurement provided by the TGV, it has the benefit of running during revenue service. The TGV, on the other hand, requires track time and runs typically four to five times per year.
“[The TGV and 7K Series] complement each other,” said Ravi Amin, WMATA’s Assistant Chief Engineer. It’s a lot of data to use, but this data can be used for wear prediction and forecasting.
“The challenge is how to bring all the data together and use it on a daily basis,” said Kevin Moore, President of Net Consulting Group, Inc., which is working with WMATA to extract more useful information from the data. In order to reach that goal, WMATA developed the Corridor Infrastructure Management (CIM) Solution. Automated Condition Assessment data (which includes track geometry, third rail geometry, tie condition, ultrasonic testing and rail profile data) all feed into the CIM. The goal is to analyze the data in one central repository in order to prioritize work, Moore said.
This approach allows multiple datasets and multiple historical measurements to be overlaid in order to pinpoint areas of primary concern and to chart the rate of change in terms of wear. As more and more historical data accumulates, the prediction models become more accurate. By looking at a curve, for example, it’s possible to project the date at which rail wear will exceed tolerance and plan maintenance accordingly.
The importance of pulling all the data into one centralized system is that it allows for intelligent prioritization of maintenance work, rather than simply chasing down exceptions.
Rail Grinding
Working as part of a team of engineers and consultants, the National Research Council of Canada (NRC) recently undertook a project at Dubai Metro to investigate rolling contact fatigue (RCF), gauge corner cracking (GCC), wheel climb risk, bogie hunting, rail corrugation, improved friction management practices and, primarily, the state of current rail grinding practices.
Rail grinding is a critical part of rail transit maintenance and WRI management. Grinding affects and is used to address nearly every aspect of wheel/rail and vehicle/track interaction. including corrugation, noise concerns, ride quality, mill scale, ride quality, and rail and wheel wear.
Due to a hard deadline for the initial opening of the metro, a comprehensive grinding strategy was never fleshed out, said Victor Kushani, Chief Track Specialist, Dubai Metro. “While I was looking into GCC grinding, Interface Journal put me in touch with the NRC,” he said.
The NRC and Sroba Rail Services were brought in to evaluate the grinding program, and specifically to determine whether the grinding machine provided by the contractor was fit for purpose. “Fit for purpose can be open to interpretation,” said Patrick Cullen, Project Engineer, National Research Council Canada. You can have a situation where the owner, operator and maintainer all have a different idea of what fit for purpose is,” he said.
The NRC’s multi-pronged approach to evaluating the Dubai Metro system involved:
- Instrumented cars to measure wheel/rail profile
- A review of inspection procedures regarding classification of RCF and gauge corner cracking
- A review of grinding implementation using the current rail grinders
- An assessment of the finished grinding results
- An assessment of the rail grinder’s ability to implement a preventive grinding strategy
The NRC’s initial assessment found evidence of inefficient grinding practices, such as grinding out RCF and GCC that was not severe enough to warrant it. The NRC also questioned the use of a fire blanket to protect the Automatic Train Control (ATC) cable during grinding. “They sometimes spent more time installing the fire blanket than actually grinding,” Cullen said. “Spark guards on the grinder carriage could do away with this.”
The NRC also found inefficiency in the grinding strategy. “There was no target profile; their idea was only to grind out cracks,” Cullen said. The grinder was “fighting fires” by jumping around the system and spot-grinding without a strategy or specification. The NRC proposed a preventive grinding regime, but it became clear that the existing grinder lacked the metal-removal capacity to realistically achieve preventive grinding, Cullen said. It was simply not fit for purpose.
This led to the NRC’s recommendation to procure a new grinder, capable of maintaining a preventive grinding program, with the following specifications:
- Minimum of 8 electric motors capable of grinding between 30 degrees field and 60 degrees gauge
- 30 HP motors required for the use of harder stones
- Minimum metal removal rate of 3 mm² per pass at 10 km/h
The NRC further determined that implementing a preventive grinding program could improve overall rail life nearly 60%.
An effective grinding program requires an appropriate specification. As the Dubai Metro example illustrates, grinding without a specification or template is an exercise in “fighting fires,” making it impossible to get ahead of the damage. “The specification is how you measure success and how you know when you’re done,” said Charles Rudeen, Transit Project Manager at Loram Maintenance of Way.
A detailed wheel/rail interaction study is often an important part of determining the grinding specification. A WRI study can identify custom profiles for tangent track, and high and low rails in order to optimize contact mechanics across the system.
The specification is also important for addressing quality-control and consistency issues. A specified tolerance for deviation between the template and the post-grind profile is the typical metric of success. This is not the only measure of success; corrugation, or longitudinal profile, surface roughness, measured depth-of-cut (in cases of grinding for defect removal) and facet width are all commonly used metrics and are often included in the grinding specification, Rudeen said.
Executing a grind specification first requires a suitable grinder. Even a simple or well-specified grind will suffer if executed with a grinder that lacks the optimal capacity. Additionally, mill scale removal, profiling, and metal removal do not occur at the same rate – a factor that must be considered in determining grinder productivity and track time requirements.
Friction Management
Grinding, of course, isn’t the only tool available for optimizing wheel/rail interaction. Friction management is another tool that transit properties use to maintain a state of good repair. Top of rail (TOR) friction modifiers (FM), which are designed to maintain a steady coefficient of friction (typically around 0.35), have been in use on both freight and transit properties for years; they are a powerful tool for managing wheel/rail interaction.
In the transit setting, TOR FM is employed for several benefits it affords. One of which is rail corrugation management. Like in heavy haul, corrugation on transit systems manifests in three types, each with its own signature wavelength range:
- Pinned-pinned corrugation: rail oscillation between restraints
- P2 resonance: vehicles “bouncing” on track
- Rutting: roll-slip oscillation between the low and high rail
Because the mechanisms of corrugation formation form a feedback loop, a minor corrugation issue can quickly become a major problem, said Richard Stock, Rail Technology Manager, LB Foster Rail Technologies Corp. As a result, effectively managing corrugation requires intervention that breaks the feedback loop. The positive friction control that TOR FM provides minimizes the wheel stick-slip that initiates (and exacerbates) rutting corrugation. LB Foster has performed a number of case studies on metro and commuter systems, examining corrugation growth in the presence of its KELTRACK TOR FM. These studies show that TOR FM can reduce the growth rate of short-wave (rutting) corrugation by an average factor of 11, Stock said.
Friction management works best when used in concert with other rail-management tools. A TOR FM regime that slows the development of corrugation, combined with a grinding program that eliminates corrugations when they begin to develop can dramatically extend rail life.
Rail grinding and friction management are tools that fall under the umbrella of maintaining a state of good repair (SGR). Back in the United States, the transit industry is looking at an $85 billion backlog in the state of good repair, said Martin Schroeder, Chief Technology Officer at the American Public Transportation Association. With one third of transit assets in marginal or poor state of repair, and track and structures making up the largest portion of this one third, catching up to the backlog is no small task.
Heavy and commuter rail represent the largest segment of rail transit systems in need of SGR remediation, Schroeder said. Part of the economic assistance for achieving and maintaining SGR will be provided through grant mechanisms in the Moving Ahead for Progress in the 21st Century (MAP-21) program.
As part of the program, all MAP-21/FTA SGR grantees and their sub-recipients will soon be required to report on:
- the condition of their system
- any change in condition since the last report
- targets set under the above performance measures
- progress toward meeting the performance targets
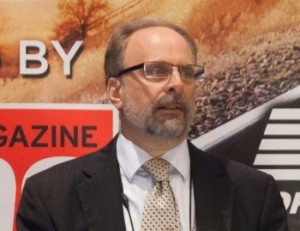
Martin Schroeder, Chief Technology Officer at the American Public Transportation Association. Photo courtesy of Jack Lindquist.
In developing SGR benchmarks and condition-monitoring criteria, the FTA queried “what exactly is SGR?” APTA suggested: “A condition in which assets are fit for the purpose in which they were intended.” Each particular agency, structure, track must, in turn, define that SGR specifically, Schroeder said. This must also include a reporting mechanism to provide the information to a national transit database, which the FTA will use to evaluate the program in years to come.
The first step in monitoring SGR is to categorize the relevant assets. APTA suggested five example assets: fleet, facilities, rail guideway, systems, and stations. These categories can be further broken down, for example: fleet → revenue car → car type → individual car → car components. Once the categories are defined, the next step is to determine how to measure and evaluate them. This is where automated inspection systems like WMATA’s come into play. With so many assets at play and so many measurements to take, the data can become overwhelming.
Last year’s Wheel/Rail Interaction Conference (WRI 2014) looked at big data – how to manage it and how to leverage it. “Like last year, the message here is the same. Integrated data is the key,” Schroeder said. Maintaining SGR requires a top-down view of the entire system, but with the ability to drill down and determine the condition of the smallest component.
“Whether regulation requires it or not, measuring the condition of assets and sub-assets is good practice,” said Bill Doran, Planning Manager for Asset Data at the Southern California Regional Rail Authority’s (SCRRA) Metrolink.
Accurately monitoring SGR status requires a nuanced system of measurement and grading, he said. Track geometry reporting is an area in which this nuance can be difficult to achieve. Current FRA reporting is based on a pass/fail assessment. Using a pass/fail system, the precise condition of the asset can remain largely unknown, and trends are not readily discernible. Comparisons of the same or similar segments of track over time are also sometimes not available. Like with rail profile measurement and analysis, it is desirable to have a means of quantifying and predicting changes over time, to program maintenance before a reactive response is required, Doran said.
To help monitor the SGR on Metrolink, The SCRRA adopted a condition scale ranging from 50 to 100:
- Excellent (90+) – An asset that exhibits no conditions of wear or degradation, essentially a “like new” condition.
- Good (80 to 89) – An asset rated as good that will require maintenance but is not expected to require replacement for the next five years.
- Fair (70 to 79) – An asset rated as fair is in serviceable condition at the time of the rating, but will require replacement within 5 years.
- Poor (60 to 69) – An asset that is operating at less than full capacity (e.g. a speed restriction is imposed) and that will require replacement of at least one component to return to full capacity.
- Critical (59 or below) – An asset requiring rehabilitation within the year in order to continue operating.
APTA’s Martin Schroeder pointed out that the FTA SGR program is expected to adopt a five-point grading scale, as well. “Our current practice should mesh well with that,” Doran said.
Automated data collection and analysis is another critical aspect of the SCRRA’s (and many other transit properties’) asset monitoring. Automated inspection not only collects more data in less time (than manual inspection) but it can also free management to focus on planning and prioritization. Regardless of whether the assessment is taken from a direct measurement or involves additional analysis, the FTA SGR requirements for measuring condition and reporting changes in condition can be met most efficiently through automated inspection and analysis systems, Doran said.
Laser-based rail profile is one of the automated tools that Metrolink uses. SCRRA uses Holland LP’s Rangecam software to analyze rail profile measurements and to generate wear trends. The profiles are typically taken at 10-foot intervals and indexed by location. The wear measurements are calculated and compared to threshold ranges. The wear determines the classification of the rail. The system also allows the user to develop a trend line using previous (historical) measurements. SCRRA uses Rangecam for both rapid identification of potential problem areas and for predicting when a segment of rail will reach a particular wear limit. “This is the kind of trending data that streamlines SGR evaluation,” Doran said.
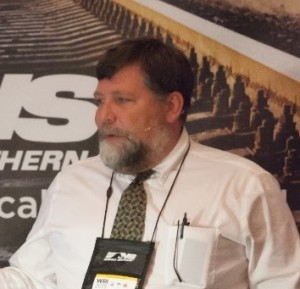
Teever Handal, Senior Engineer Vehicle/Track Systems at Advanced Rail Management Corporation. Photo courtesy of Jack Lindquist.
Los Angeles Metro’s Blue Line has also undertaken a project that aims to take a proactive approach to maintaining SGR. The LA Metro’s wheel/rail interaction issues, and subsequent optimization in the 1990s, have become something of a case study in wheel/rail interaction and design (See Managing Wheel/Rail Interaction on Rail Transit Systems). Having achieved wheel life and ride quality goals, the LA Metro’s current project aims to prioritize maintenance on special trackwork.
The goal of the project was to identify areas that were problematic (or would soon become problematic), despite not currently being safety or slow-order issues. In doing so, LA Metro hoped to identify high-priority targets for proactive maintenance.
“We wanted to know where to spend our time and money in preparation for FTA/MAP-21 requirements,” said Wyman Jones, LA County Metro Transit Authority’s Director of Rail Operations Engineering and Strategic Planning.
When the LA Metro joined the Blue Line to the Expo Line, via an in-street junction, signs of premature vehicle wear began to appear. First there was a journal bearing failure, then the Mechanical department found hairline cracks in the motor mounts of new cars. The LA Metro brought in Advanced Rail Management Corp. (ARM) to measure the Blue Line and find the problem areas. ARM’s first step was to provide a baseline dynamic assessment. “We needed a baseline not just of the vehicle or the track, but of the entire system,” Jones said.
ARM instrumented the two car types (Nippon Sharyo P865 and Siemens P2000) operating on the Blue Line and measured the entire line. “Our primary goal was to gather the data with minimal instrumentation that would still provide an accurate representation of operating conditions,” said Teever Handal, ARM’s Senior Engineer Vehicle/Track Systems. Both car types were instrumented identically with the following:
- truck-mounted tri-axial accelerometer
- truck-mounted video camera
- under car audio
- string potentiometer to measure rotation
- car-mounted video camera of the center truck
- GPS
- cab camera
- carbody accelerometer
ARM focused its analysis on track perturbations, and processed the collated data in order to develop a single “severity index” value for each piece of trackwork in the Blue Line. “The baseline severity index gave us an overall sense of the [Blue] Line’s condition in relation to state of good repair,” Wyman Jones said.
After measuring a baseline, ARM was able to measure for anomalous events and noted three specific sites whose severity index dramatically exceeded the baseline. On inspection of the physical sites, certain issues became clear. One site had a number of rotten ties, another had poor ballast drainage, the third had geometry design issues. None of the sites, even those with the highest severity indices met any safety concern or slow-order thresholds. Yet, all three sites were clearly causing excessive wear and ride quality issues. “These sites might not be critical now, but three years down the road you’re going to pay for it,” Jones said. “Meanwhile you’re damaging the wheel and rail.”
By pinpointing sites that, while not critical concerns, were problematic and likely to become more so, the LA Metro gained a more accurate sense of the current SGR as well as the upcoming requirements necessary to maintain and improve the SGR.
Noise and Vibration
Like other symptoms of sub-optimal wheel/rail interaction, noise and vibration can be an indicator of SGR condition. The techniques used to mitigate noise and vibration are often not specific to noise and vibration, but rather affect the wheel/rail interface as a whole. These include wheel and rail profile optimization (grinding and truing), friction management, car design, rail fastener design, purpose-built vibration dampers, among others. Noise and vibration indicate an issue at the wheel/rail interface. An issue at the wheel/rail interface indicates a shortcoming in the condition of SGR. Like corrugation development, it can be a kind of feedback loop.
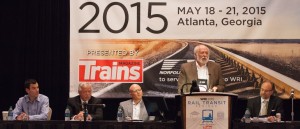
The WRI 2015: Transit panel on noise and vibration. (Matthew Doyle, Mike Holbrook, Bryce Dudgeon, Gary Click, and Martin Schroeder). Photo courtesy of Jack Lindquist.
The Vancouver, B.C., SkyTrain’s early attempts to control corrugation-induced noise via rail grinding didn’t make much progress. By inadvertently using the “fire-fighting” model of spot-grinding the worst offenders (the noisiest locations, in this case), SkyTrain in fact saw the problem get worse. “We were flattening our rail and basically encouraging corrugation growth,” said Matthew Doyle, Mechanical Engineer at BC Rapid Transit Company. Noise got worse and rail damage began to accrue at an increasing rate.
The solution to reining in its noise problem has proved elusive. SkyTrain is currently reviewing both wheel and rail profiles, as well as its grinding practices in an effort to find a lasting solution to corrugation development and the attendant wear and noise issues.
Friction management is also used to help mitigate noise and vibration. While the economic impact of noise and vibration can be harder to quantify than corrugation development (See Dave Anderson’s presentation in WRI 2014 : Transit), an economic impact certainly exists. “The ability to lubricate constantly and effectively reduces noise and wear and it’s cost effective,” said Mike Holbrook, Senior Manager in the Dallas Area Rapid Transit system’s Track and Right of Way Dept.
In addition to corrective/preventive approaches like grinding and lubrication, a number of considerations go into special trackwork to mitigate noise and vibration. These include design considerations such as the elimination of bolted joints (known to generate high noise and vibration) and elastomeric grout backfill. Some noise and vibration design considerations have a direct effect on wheel/rail interaction such as crossover geometry and frog design.
Significant noise and vibration through a crossover or diamond could be an indication of improper gauge, poor steering, or other wheel/truck issues, said Gary Click, Technical Director, voestalpine Nortrak North America. “We do a wheel/rail interface study to determine what flangeways and gauges should be. It’s got to be optimized.”
Vehicle design also has a significant impact on noise and vibration generation and therefore on wheel/rail interaction. General design philosophy, said Bryce Dudgeon, Sr. Mechanical Engineering Manager at Siemens Rail Systems, is to:
- minimize the unsprung mass in order to minimize impact to track and ground-borne vibrations
- provide low-stiffness primary suspension that is stable in tangent track at high speed
Resilient wheels and vehicle-mounted flange lubricators (which perform the same function as wayside lubricators), which are common noise and vibration damping elements, also dramatically affect wheel/rail dynamics.
All of these noise and vibration management techniques reinforce the fact that every aspect of the health of the wheel/rail interface can function as an indicator of SGR condition. As transit properties consider the FTA SGR reporting requirements, perhaps the biggest take-away from the WRI 2015 Transit Conference is this: Establishing a verifiable SGR is important, but it’s possible and beneficial to maintain to an even higher internal standard. And effectively managing wheel/rail interaction and planning for proactive maintenance can make maintaining assets to meet the State of Good Repair requirements a lower bar to clear.
Jeff Tuzik is Managing Editor of Interface Journal