Rail Corrugation: A Problem Solved?
by Jeff Tuzik
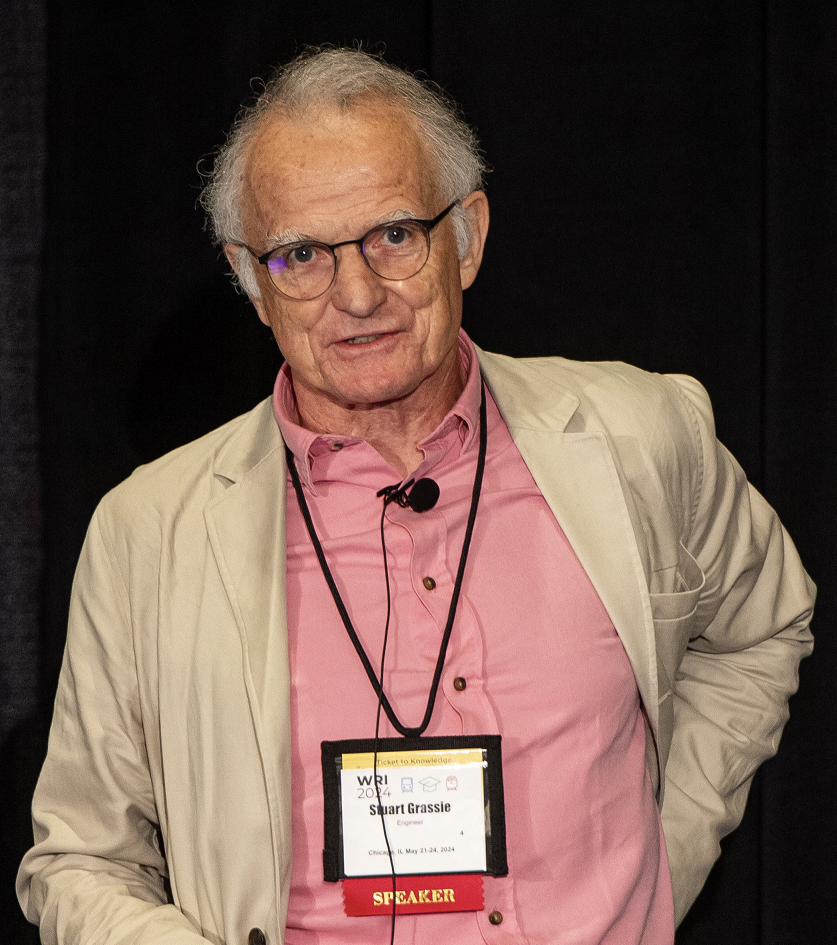
Rail corrugation is a common phenomenon. It’s found on both freight and transit lines around the world. The mechanisms behind corrugation are well understood, and there are many tools and techniques available to mitigate and remedy corrugation and its underlying causes. But this hasn’t always been the case.
“When I started working on rail corrugation 45 years ago, we knew almost nothing about the causes,” Stuart Grassie, Principal of Rail Measurement Ltd. and Stuart Grassie Engineering Ltd., told delegates at the Wheel Rail Interaction 2024 Rail Transit Conference. “Today, I think it’s safe to say corrugation is a solved problem.”
Some of the problems caused by rail corrugation are associated with a specific form or frequency; shorter-wavelength corrugation tends to cause excessive noise, while longer wavelengths tend to transmit ground-borne vibrations into the track and surrounding structures. Regardless of the wavelength, all forms of corrugation are associated with accelerated fatigue damage to wheels, rail, and other vehicle and track components.
A seminal paper published in 1993 by Stuart Grassie (SL Grassie and J Kalousek, “Rail corrugation: characteristics, causes and treatments”, Journal of Rail and Rapid Transit, Procs of I mech E, 1993, 207F, 57-68), the recipient of Wheel/Rail Seminars’ 2024 Worth Award, and Joe Kalousek, the now retired Senior Scientist at the National Research Council of Canada (and the first recipient of the annual WRS Worth Award), defines a mechanism for corrugation formation in which a wavelength-fixing mechanism such as traction or friction generates dynamic loads which impart damage (wear) to the rail and, thus, alter the rail profile. This creates a feedback loop where changes to the rail profile and dynamic loads increase in magnitude over time (see Figure 1).
All wavelength-fixing mechanisms are constant frequency phenomena — resonances and anti-resonances, Grassie said. The wavelength of the corrugation that appears on track is a function of train speed and the frequency of the wavelength-fixing mechanism. The reinforcement or repetition of this mechanism is why corrugation develops more quickly on transit lines, and especially on transit lines that use Automatic Train Operation (ATO), where there is little variance in train speed and handling (from train to train), he said.
Rail transit systems predominantly encounter four types of corrugation as classified by their wavelength-fixing mechanism; these are P2 resonance, trackform-specific resonance, pinned-pinned resonance, and rutting.
P2 resonance is the result of an un-sprung mass (primarily the wheelset mass) “bouncing” as it moves down the track. This type of resonance occurs in both ballasted and non-ballasted track, and is heavily influenced by the characteristics of the baseplate or under-tie pads, or the ballast itself. The frequency of P2 resonance is typically 50-100 Hz. “Given average transit speeds, this gives rise to corrugation of a few hundred millimeters wavelength,” Grassie said. This type of resonance exists on all types of railways, but it doesn’t always form corrugation. This makes mitigation a challenging prospect. “Since P2 resonance is based on the trackform, if you get this wrong and later find P2 resonance corrugation in one place, it means you’re going to get it everywhere,” he said.
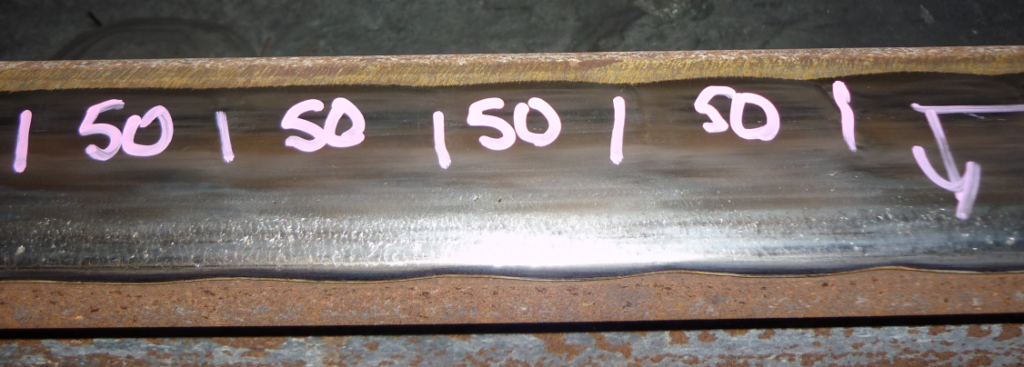
Trackform-specific resonance corrugation is something that has become increasingly common over the past 30 years, and is particularly prevalent on some Chinese transit lines, Grassie said. Some of this corrugation is so severe that it causes plastic flow with the same periodicity as the corrugation (see Figure 2). This type of corrugation is also notable for developing very quickly. For example, Figure 3 shows a comparison between track with trackform-specific resonance (A), and an adjacent track with a standard trackform (B). In only 57 days after grinding, track A has developed corrugation of greater than 10 times the amplitude of that on track B.
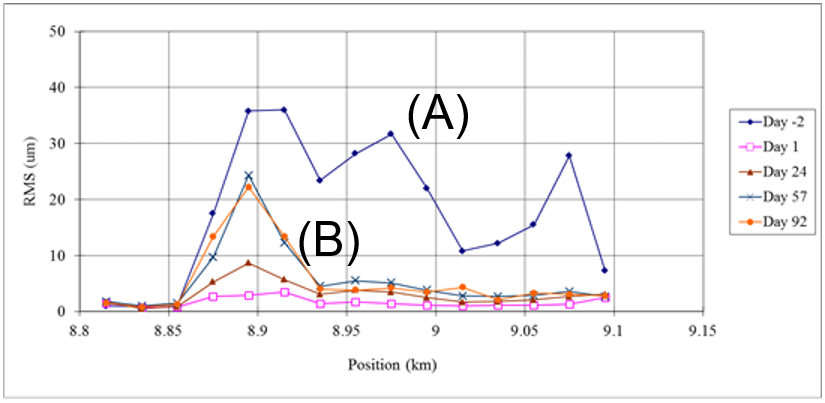
“At this time, very little is known about why trackform-specific corrugation develops, or why trackforms of the same general type don’t always corrugate,” Grassie said. And because the mechanism behind the corrugation isn’t well understood, no targeted preventive measures have been identified. There are, however, some commonalities between sites that show severe corrugation of this type, notably the presence of a high-mass baseplate combined with a resilient pad between the rail and baseplate; this combination can produce high dynamic loads that could be the culprit, he said.
Pinned-pinned (p-p) resonance corrugation is typically found on high-speed lines, and usually represents the highest frequency resonance (shortest wavelength) that gives rise to corrugation. This type of resonance occurs as a result of the rail vibrating between fasteners/ties. Conceptually, the rail operates like a guitar string, and the fasteners like frets, Grassie explained. In this scenario, between the fasteners there is relatively easy movement of the rail under load, but at the fastener itself, the rail is much stiffer. The cyclic dynamic loads that occur as wheels pass over points of varying stiffness initiate corrugation. “P-p resonance does appear on some transits like BART and London Underground, but it’s fairly uncommon in that environment,” he said.
Finally, there is rutting. Rutting is a type of corrugation very common on transit systems, Grassie said. It is typically associated with the low rail in curves, but it can appear on the high rail as well. The wavelength-fixing mechanism for this type of corrugation is flexural resonance of the wheelset. Due to the fundamental design of wheelsets rigidly attached to axles, there is a resonance inherent to the bending of the axle. This resonance is typically in the 100-Hz range (similar to P2 resonance). The reason this type of corrugation typically manifests in curves is that lateral creep and high angle of attack are typically responsible for exciting flexural resonance. As a result, techniques that improve steering and reduce lateral creep forces, like optimized wheel and rail profiles, also help to mitigate rutting. However, the most successful mitigation measure is the use of friction modifiers, he said. Friction modifiers reduce the stick-slip action of wheels navigating a curve and reduce the overall excitation of wheelset flexion. While this doesn’t eliminate the resonance, it significantly reduces the damage it imparts.
Grassie’s recent work on the Kajang Line of Kuala Lumpur’s Mass Rapid Transit (MRT) (see Figure 4) represents a culmination of corrugation mitigation theory and praxis — a corrugation-free rail line. This is particularly noteworthy because the Kajang line has several features that are conducive to corrugation formation, including:
- Short distances between stations
- Entirely non-ballasted track
- Automatic Train Operation (driverless, computer-controlled trains)
- Steep gradients of up to 3.5%
- Tight curves of up 150-meter radius (~11.7 degrees), often at station exits and approaches.
“A train under full traction in a 150-meter curve is a challenging scenario when it comes to corrugation,” Grassie said. This, combined with little-to-no variation in traction, speed, or braking due to ATO is a combination of factors all but guaranteed to cause corrugation in the absence of mitigation efforts.
The Kajang Line project was also uniquely challenging in that the track specification included stipulations that the contractor(s) produce a report indicating they had “considered all known corrugation forming mechanisms and taken due mitigation measures for each” and that “where corrugation mechanisms are discovered due to omission or error […] they shall be rectified by the contractor at his own expense.” From a practical standpoint, the stipulations meant that the contractor was responsible for mitigating corrugation in the design, construction, and operation phases of the project. “I haven’t seen requirements like these in a contract before or since,” Grassie said.
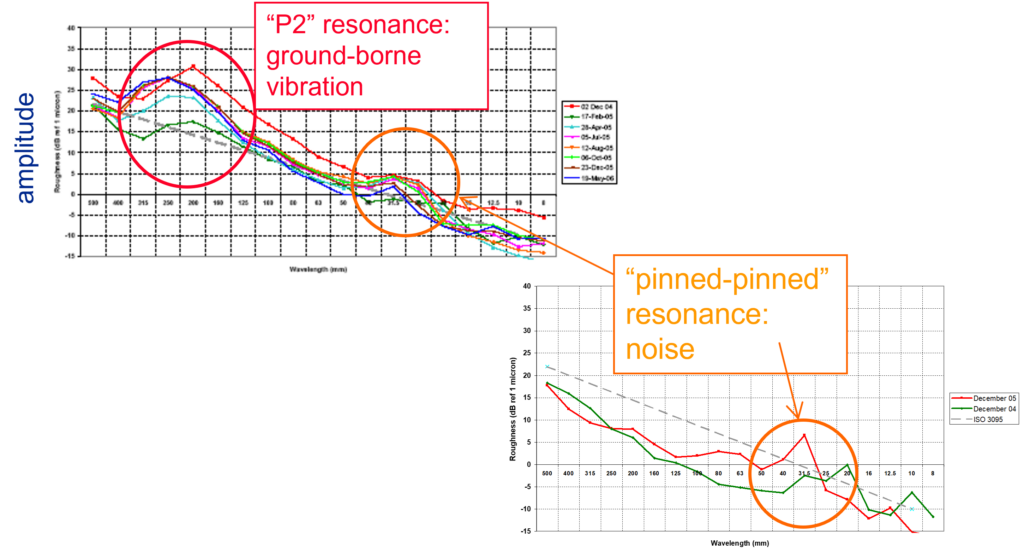
The results of previous studies also helped guide trackform selection for the Kajang Line, including one conducted for the Transportation Research Board in the 1990s (see: SL Grassie and JA Elkins, “Corrugation on North American transit lines”, Vehicle System Dynamics Supplement, 1998, 28, 5-17 and BJ Brickle, JA Elkins, SL Grassie and SJ Handal, “Rail corrugation mitigation in transit”, Research Results Digest, Transit Cooperative Research Program, National Research Council, USA, number 26, June 1998). In this project, it became apparent that the presence or absence of P2 resonance corrugation depended critically on the stiffness of the trackform. From data on four North American transit systems, it was deduced that P2 resonance corrugation did not occur on trackforms with a support stiffness of less than 40MN/m per meter of track. These findings were confirmed in another study undertaken on London Underground, in which a section of track between two stations was of particular interest because it had both a traditional trackform (timber ties cast in concrete) and a very-resilient trackform (Pandrol Vanguard) abutting one another. P2 resonance corrugation was pronounced here on the traditional trackform but absent on the section with the Pandrol Vanguard fastening system (see Figure 5).
The TRB study looked at the presence or absence of P2 resonance corrugation on four systems with varying fastener stiffnesses, damping, and spacing. These results showed that stiffer trackforms were more likely to develop P2 resonance corrugation, Grassie said. The study concluded that in general, a fastening system stiffness of 40 MN (meganewtons) per meter, per meter of track (40MN/m2) or less should not be at risk of inducing P2 resonance corrugation.
Prevention of trackform-specific corrugation on the Kajang Line largely came down to experience and engineering judgement, Grassie said. It was also important not to inadvertently replicate any of the specific conditions known to be associated with trackform-specific resonance. “This hasn’t been tested before, so in some ways Kuala Lumpur was an experiment,” He said, “It worked, but that’s a very expensive experiment to get wrong.”
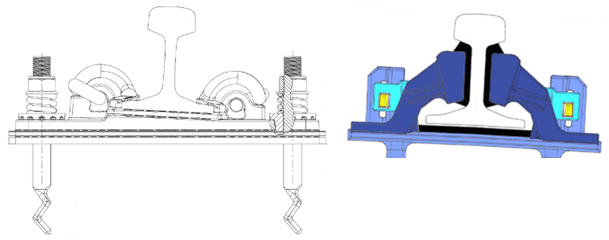
Based on this data and experience, two trackforms were selected for the Kajang line. The Pandrol Vipa was selected as the “standard” trackform. It was configured to have a high-stiffness rail pad between the rail and base plate, and a relatively low-stiffness baseplate (installed under the base plate). For noise-sensitive sites, the Pandrol Vanguard was selected. The Vanguard supports the rail by the web, rather than the foot, and thus has a very low vertical stiffness. Additionally, previous studies have shown that the Vanguard has a negligible effect on P2 and trackform-specific corrugation, Grassie said.
Avoiding p-p resonance was a more straightforward task. The primary variables at play are the bending stiffness of the rail and spacing of the fasteners. “The goal is to ensure that the p-p resonance is sufficiently high so that any corrugation that developed would have a wavelength of similar size to the contact patch,” Grassie said. In practical terms, this means that getting the p-p resonant frequency to 20mm or below (the size of the contact patch) effectively eliminates the potential corrugation. As an example, for a train traveling at 100km/h on standard 60kg/m rail, a fastener spacing of 0.7m (or less) is sufficient to eliminate p-p resonance corrugation, Grassie said.
Because the Kajang Line has so many sharp curves, especially near stations, it was suspected that rutting could develop. Altering the geometry of the track wasn’t an option, so Grassie’s proposal was to wait until the line went into service and then, if rutting developed, to target only the affected sites with wayside friction modifier installations. Thus far, no rutting has developed, and no friction modifier applications have been necessary.
As the design and build phases of the Kajang Line project came to an end, Grassie’s team established nine sites to monitor potential corrugation development. Monitoring occurred twice annually, starting before the introduction of revenue service traffic, and continued for two years of revenue service. The monitoring sites were chosen based on characteristics conducive to corrugation formation (station exits, sharp curves, high speeds, and steep gradients). All sites were 500m long and included locations with both trackform—Vipa and Vanguard (see Figure 6).
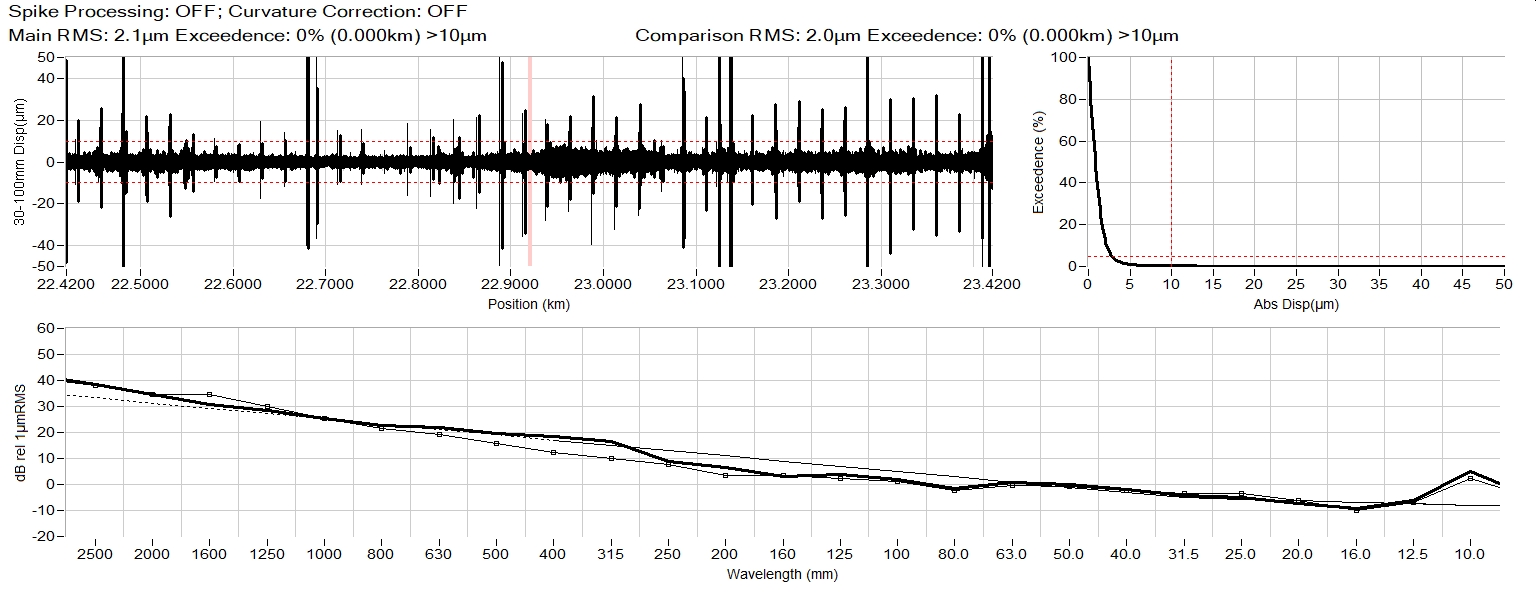
The results from one of the sites are indicative of the efficacy of Grassie’s work. This site includes several sharp curves, a transition from tunnel to elevated track, a station exit, and both trackforms. After two years of service traffic (25 MGT per year) the site showed insignificant corrugation. Corrugation Analysis Trolley (CAT) readings of surface roughness showed results mostly in the +/- 10-micron range (see Figure 7). The lower graph shows 1/3rd octave band roughness curves for the site after two years of traffic, compared to an example acoustically-ground rail. “After all this traffic, we have rail that’s as smooth as acoustically-ground rail.” Grassie said.
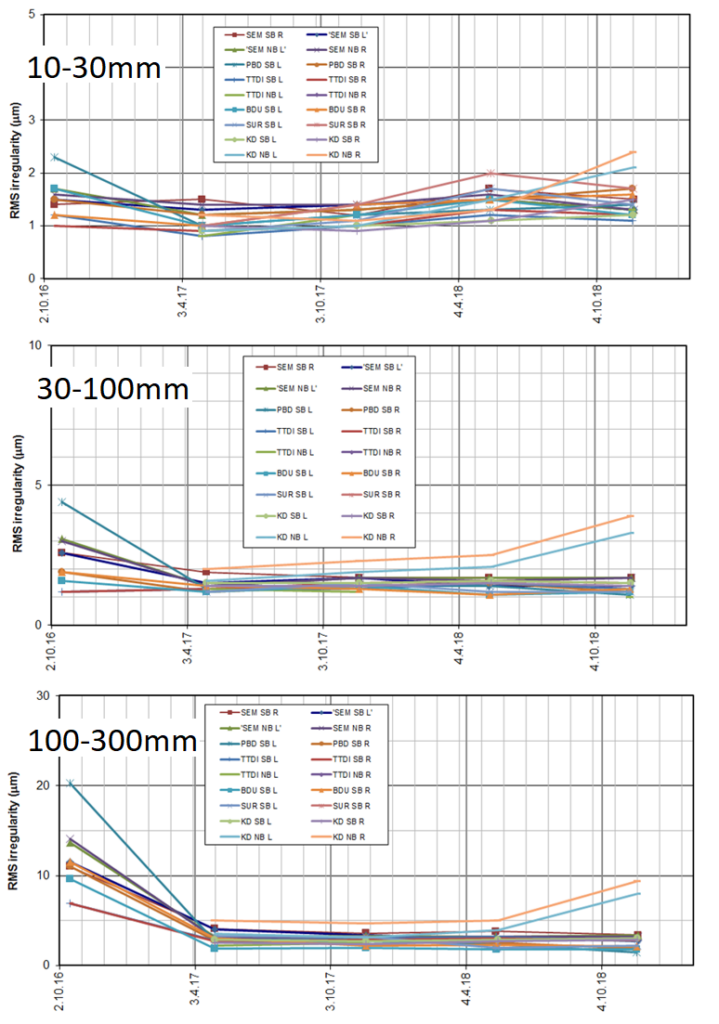
Figure 8 shows 2 years of surface roughness data from all nine sites for different wavelength ranges: 10-30mm, 30-100mm, and 100-300mm. For each wavelength range, all sites remained below the surface irregularity threshold for acoustically-ground rail (4 microns RMS, 4 microns RMS (root mean square), and 12 microns RMS, respectively).
“As far as I’m aware, this is the first and only time a metro system has been built with a requirement that no rail corrugation should occur,” Grassie said, “much less done so successfully.” Monitoring after two years of heavy service traffic indicates that not only is a corrugation-free rail line possible, but that the criteria for design and construction are not especially onerous. The success of the Kajang Line was built on decades of experience and knowledge gleaned from hard-won battles with rail corrugation in all its forms. It’s also a testament to the importance of all parties — the trackwork contractor, transit agency, consultants, and sub-contractors working collaboratively and pulling in the same direction. “Mitsubishi [the trackwork contractor] deserves a lot of credit for having faith in our proposals,” he said. When all these factors fall into place, it appears that corrugation is a solved problem.
Eric Magel, Principal of EM-WRI Consulting Inc., and former Principal Engineer at the National Research Council of Canada, and internationally recognized expert in wheel/rail interaction and remediation made note of the accomplishments on the Kuala Lumpur system. As a consultant examining maintenance and wheel/rail-related issues on Kuala Lumpur’s Kajang Line, Magel noted that despite some issues, the system had no corrugation. “I was frankly astounded,” he said, “Corrugation is usually everywhere.” But through measuring and modeling numerous components, their masses, stiffness, resonances, and other parameters, he said, Stuart Grassie demonstrated that a system can be designed to be corrugation free.

Jeff Tuzik is Managing Editor of Interface Journal
This article is based on a presentation made at the Wheel Rail Interaction 2024 Transit conference.