MRS Logística: A History of Innovation and Optimization
by Jeff Tuzik
Some challenges in the railroad industry are local, some are universal. Brazil’s MRS Logística has met its share of both. Their efforts to maintain, modernize, and optimize their network over the past 30 years highlight the importance of approaching all challenges from a system-wide perspective, and of leveraging every resource at their disposal.
The Brazilian freight railroad industry is in the midst of major growth: speeds and axle-loads have both increased, driving a systemwide production increase of 30% in the past five years. In the next five years, MRS will increase axle loads from 32.5 metric tonnes (38.8 US tons) to 36 tonnes (39.7 US tons), increase consist size (to 272 cars), increase train speeds by 25%, and begin to roll out hybrid locomotives, Antonio Merheb, consultant to MRS Logística, and Chairman of the International Heavy Haul Association, told delegates at the 2023 Wheel/Rail Interaction Heavy Haul Conference.
MRS Logística’s operations account for 30% of Brazil’s national railway production, and links the country’s three largest seaports. The most immediate challenges that MRS faces are due to the age of the infrastructure. “The majority of our track was laid more than 100 years ago,” Merheb said. MRS also operates in Brazil’s most densely populated areas, passing through many cities. “Much of our operation is in tight corridors, very close to commercial and residential areas,” he said.
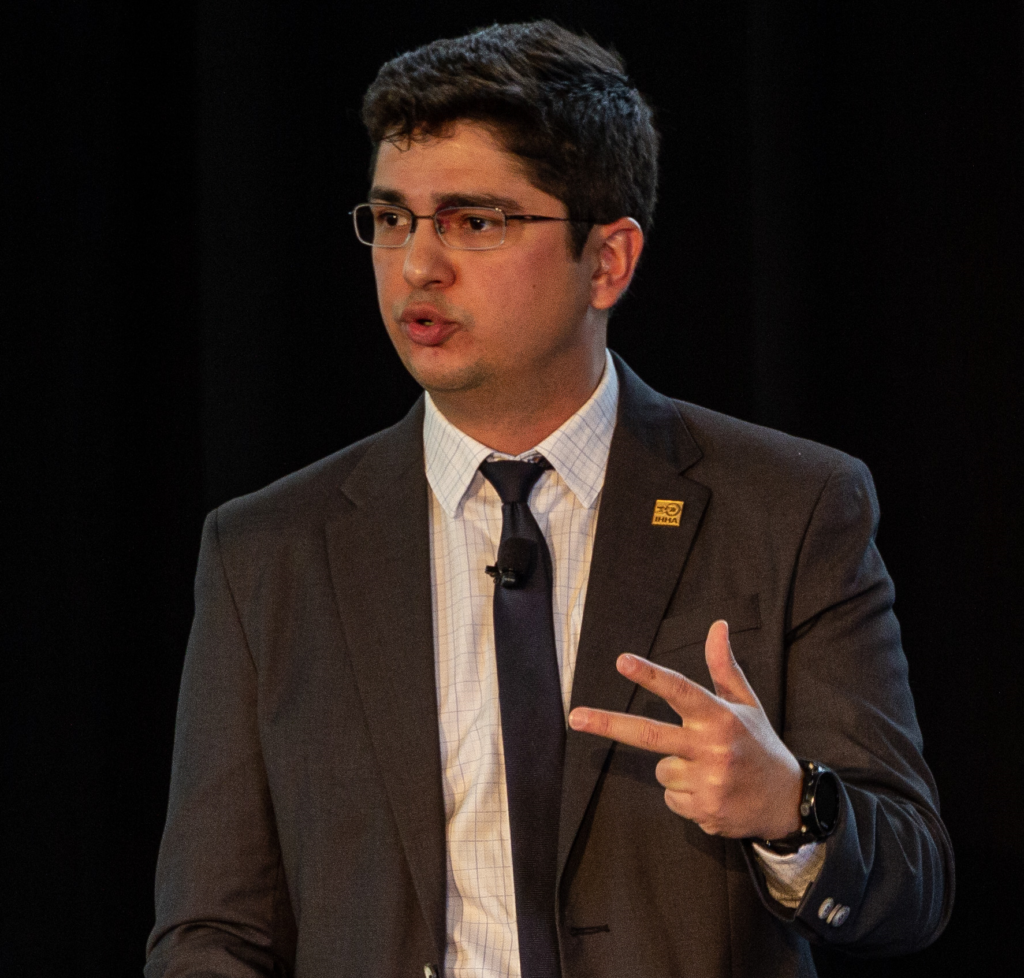
MRS divides its 1,680 km network into 4 divisions and 20 subdivisions, many of which feature particularly challenging conditions and constraints. The Ferrovia do Aço division is a 357-kilometer, 170-MGT line that was built primarily in the late 1980s and early 1990s. It has 50 km of bridges; 45 km of tunnels, up to 600 m-radius (3-degree) curvature, and a 1.2% maximum grade.
The Serra do Mar subdivision, part of the Rio de Janeiro division, is a 96-kilometer, 190-MGT subdivision that was built in the 1880s. has 4 km of bridges, 10 km of tunnels, up to 150m-radius (11.5-degree) curvature, and a 2.2% maximum grade.
“As you would expect, due its age, this is a uniquely-challenging operating environment,” Merheb said.
The Cremalheira subdivision, part of the São Paulo division, is a 95-km, 10-MGT subdivision that was built in 1960. It has 2 km of bridges, 200m-radius (8.7-degree) curvature, and a maximum grade of 11.8% that requires specially designed rack and pinion locomotives to negotiate the 8 kilometers 1600-mm gauge “rack track” on the electrified line between São Paulo to the port of Santos.
“The Cremalheira Sub doesn’t see a lot of tonnage, but the 11.8-percent grades are challenging,” he said.
The 4th division, Minas Gerais, which runs 45 MGT, moves general cargo to and from the ports, and the track on which the empty wagons return to the iron mines.
Because of vastly different operating environments like these, MRS has had to develop a flexible and agile approach to problem-solving and optimization.
Since MRS Logística began operations in 1996, it undertaken several major development programs. Notably, in 2008, MRS worked with the Canadian National Research Council Canada (CNRC) to develop a comprehensive wheel/rail optimization program. This came about after years of attempts to curb rampant rolling contact fatigue (RCF), shelling and spalling, and generally rapid track degradation. This project helped break down barriers within the organization, between departments, Merheb said, and to build a culture of collaboration on systemwide improvements. “We didn’t get the results we wanted until we brought operations, track, and rolling stock [departments] together to look at full system interaction.”
To that end, MRS implemented several ongoing improvements including:
- Adoption of matched wheel and rail profiles
- Expanded use of premium rail steels
- Deployment of gage-face lubrication and TOR friction modifiers
- Deployment of wheel impact load detectors (WILDs)
- More frequent preventive grinding cycles
- Adoption of flash-butt welding
Merheb credits this collaborative, system-wide approach for much of MRS’ subsequent successes and system optimizations. The results are evident in track condition improvements, for example. From 2012 to 2022, high-priority defects dropped from 720 to 100. Average rail life over the same period increased from 381 MGT to 829 MGT. And the number of derailed cars on mainline track dropped from 142 to zero. These achievements are particularly notable given the unforgiving conditions of the Serra do Mar subdivision, Merheb said.
In 2017, MRS once again brought the departments together to investigate dynamic forces throughout the system. Specifically, the goal was to increase tonnage per axle from 32 metric tonnes (38.8 US tons) to 36 metric tonnes (39.7 US tons), (to while decreasing dynamic loads.
The first part of this project was the development of an instrumented consist made up of a locomotive and 16 cars. The cars were split into four groups: a control group without apparent defects or lading deviations, and three groups with known defects or variations such as uneven tonnage per axle, wheel defects, and damaged springs. As this train circulated through the system, MRS developed a map of dynamic forces across the network to determine where their maintenance/optimization resources would have the most impact in reducing these forces.
Based on the data, the first priority was the rolling stock; MRS adjusted wheel inspection cycles, and renewed pads and springs fleet-wide. The second priority was bridge transitions; many of these transitions were reinforced or replaced. The third priority was track; rail grinding and tamping cycles were adjusted to better allocate resources to more problematic areas, Merheb said.
During this same period (2017 – 2020) MRS also launched a track modulus investigation that ultimately mapped its entire system. All these projects and studies generated a lot of data – too much data to sift through manually. “We ran into a bottleneck in processing and analyzing all the data we were collecting, so we were always a step behind when it came to implementing strategies based on the data,” Merheb said. Datasets were all stored and analyzed in isolation; correlations drawn from the data were done so manually and, therefore, slowly, he said. It’s hard to know which datasets are relevant enough to each other to warrant correlation or analysis, in the first place.
In order to address their big data problem, MRS looked to outside expertise to help restructure their entire data workflow. Beginning in 2019, MRS has worked with Visiostack to overhaul and streamline every aspect of their data handling. Data from all sources, such as track geometry cars, instrumented wheelsets, VTI monitors, ultrasound inspection, and many others, now flows into a data lake repository, where it is accessed and filtered by an asset management platform, from which action plans can be generated, Merheb said. “The same analyses that once took days of manual work, now happen automatically.”
Consolidation of the data has also allowed for more sophisticated analyses, which have led to more sophisticated maintenance strategies. “It’s much easier now to prioritize maintenance work,” Merheb said, because all relevant data is aligned, correlated, and overlayed as a matter of course. This has also enabled MRS to fine-tune renewal and replacement strategies, based on predictive analyses of the data. “Once we had confidence in the analytics [of the asset management platform], we felt comfortable using these predictions to inform our maintenance decisions.”
MRS’ big data overhaul has already been successful. In 2021, the railway realized an 8% savings in its track maintenance budget; in 2022, another 6%, Merheb said. This is reflective of a smarter, more targeted approach to maintenance, as well as a shift toward a preventive rather than reactive maintenance mode.
MRS has evolved over the past 20 years to meet the challenges of a modern freight railroad. One of the most important steps in this process has been the collaboration of operations, track, and rolling stock departments to address maintenance and optimization at a systemwide level. This collaborative mindset extends to data, too. By enabling its “big data” to work together, MRS has refined its approach to maintenance and planning and reaped the benefits along the way. For any railroad, much less one running, in part, on track laid 140 years ago, the results are remarkable.

Jeff Tuzik is Managing Editor of Interface Journal.
This article is based on a presentation made at the WRI Heavy Haul 2023 Conference.