Wheel/Rail Profile Optimization on Wiener Linien’s Vienna Underground line U6
by Jeff Tuzik
One of the surest and most common signs that something is amiss at the wheel/rail interface is accelerated wear of the wheels, rail, or both. Occasionally the solution to the problem is straight-forward and site-specific. But more often, abnormal wear appears as a symptom of fundamental, systemic wheel/rail dynamics gone awry. Correcting these types of problems is anything but simple and requires involved measurement, analysis and remediation — this is the situation in which Wiener Linien, operator of the Vienna Underground, found itself in 2022.
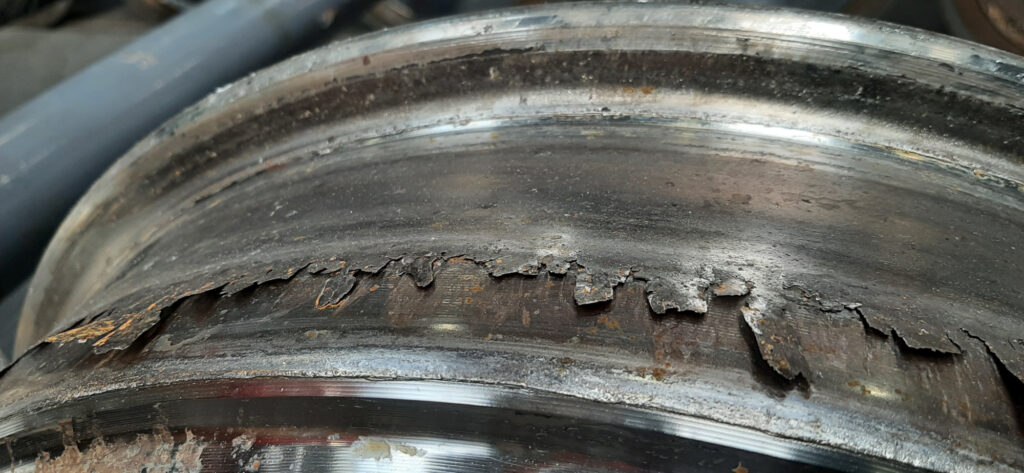
Wiener Linien began to encounter dramatically increased wheel wear on the Vienna Underground line U6 after a 2022 rail renewal and grinding/milling project. Figure 1 shows one such example of a heavily-worn wheel with significant rolling contact fatigue (RCF) damage as well. From the outset, it was clear that the scope of the problem (and ultimately, the solution) necessitated broad expertise, Lukas Prettner, Head of Track Systems at voestalpine Rail Technology GmbH, told members of the International Collaborative Research Initiative at its September 2024 workshop. This joint project ultimately drew on expertise from Wiener Linien’s engineering department, voestalpine Railway Systems, the Railway Infrastructure Design Institute at TU Graz, and engineering firm PJ Messtechnik GmbH.
A wheel/rail interaction project like this would be a complex undertaking on any rail line, but Line U6 provides some unique complications. The line itself was designed in 1890 for steam operation. It was converted to an electric tramway-like service after WW1, and now operates as a metro/mass transit line; it’s fleet of Bombardier Type T and T1 vehicles is classified as light rail vehicles and was designed specifically to be able to use Wiener Linien’s tramway network in order to access the shop. “This means that the vehicles and the wheels themselves have a quite specific design,” Prettner said.
The 2022 rail renewal, grinding and milling program was implemented to reprofile worn rail and to remediate defects found throughout the line, including significant corrugation and RCF at multiple sites and dipping welds. Some degree of rolling contact fatigue (RCF) development is unsurprising, Prettner said, given that line U6 has very sharp curves, including one with a 123-meter radius (14.3-degrees).
Prior to the rail renewal project in 2022, line U6 had less of an issue with wheel wear, Prettner said, as wheel and rail shapes have adapted to each other. Following the renewal, flange wear rose dramatically. Figure 2 shows a comparison of wheel flange width compared to wheel diameter in 2019 and in 2022. The high flange wear was accompanied by plastic deformation and spalling, as well. But the real question, Prettner said, was why the wheel wear problems began after the track was renewed and was thus in nominally ideal condition; “clearly something had gone wrong at the wheel/rail interface.”
voestalpine’s first step was a destructive analysis of several wheels. This revealed significant hardening of the wheel surface (from a baseline of ~283HB (Brinell) to as high as 341HB). There was also significant cold deformation and crack initiation found at the flange root (see figure 3).
Prior to the 2022 renewal project, voestalpine was also running a concurrent test on line U6 examining the wear behavior of higher hardness rail steel on the high rail in curves. The test was set up so that the high rail in the test site repeatedly alternated between steel types: 45 meters of 400 UHC® HSH® steel and then 45 meters of R350HT steel. The low rail was set up the same, but using 400 UHC® HSH® and R260 steels. Results indicated that the harder steel showed a 50 % reduction in terms of both wear and RCF and reduced corrugation to a minimum. These results convinced Wiener Linien to adopt R400HT steel, specifically the 400 UHC® HSH®, as the standard for high and low rails in curves during the 2022 renewal. But the presence of harder rail in some curves should have had no bearing on the increase in wheel wear that later occurred, Prettner said, as the test trials have just been conducted in a single curve. In the discussion Prettner added that it has also been proven several times that hard rails have no negative influence on wheel wear.
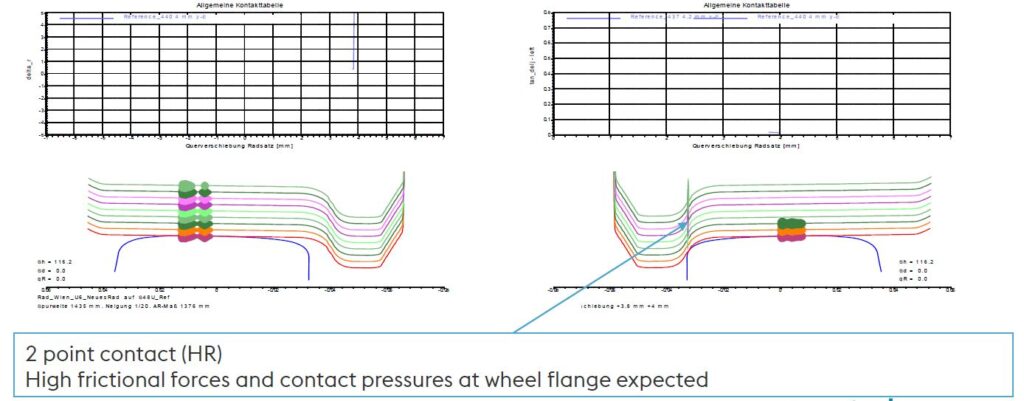
The investigation into the cause of accelerated wear began at Wiener Linien’s Engineering Department with a preliminary analysis of the nominal (as of 2022) wheel profiles on nominal rail profile S48U and the design of a new wheel profile. This analysis showed contact conditions that indicated two-point contact on the high rail, with likely very high forces at the gauge corner/flange root and face (see figure 4). “It’s easy to imagine from this image that you’re going to get high friction and contact pressures in keeping with the flange wear we were seeing,” Prettner said.
The team then prepared a more sophisticated analysis in the form of a multi-body-simulation (MBS) model. This allowed them to model the dynamic behavior of the specific car and train configuration that runs on line U6. The Bombardier Type T/T1 is a 3-car multiple-unit with motorized two-axle bogies at the front and rear of the consist, and two unpowered single-axle bogies in the intermediate car that are steered according to the articulation angle (see figure 5). Once the model was developed, voestalpine simulated tangent track and multiple curves ranging from 123 m radius (~14.3 degrees) to 800 m radius (~2.2 degrees).
“When you’re dealing with very complex simulations like this, you need data from the field to know you can trust the model,” Prettner said. The team set up a wayside measurement site to do that, collecting lateral and vertical loads for comparison to the MBS results. The results were encouraging. Maximum lateral force was simulated 9.8 kN and measured at 11.2 kN. Maximum vertical loads were simulated 42.8 kN and measured at 42.5 kN. “Jointly, we decided that the model was accurate enough to move forward with.”
Wiener Linien also designed a new wheel profile to specifically avoid the deleterious contact conditions causing accelerated flange wear. The new wheel (see figure 6) had a number of geometry changes, but the primary differences were that the new wheel provided single-point contact; the flange root radius was increased from 10 mm to 14 mm; and the flange was made thinner, effectively providing more clearance between the rail gauge corner and the flange root and a better steering behavior in the curve. The team provided Wiener Linien with their measurements, simulations of dynamic behavior, and recommendations to optimize the design, especially regarding contact pressure and switch/crossing interaction.
On the rail side of the equation, voestalpine provided updated rail profiles with increased relief at the gauge corner (again, to reduce the propensity for flange wear) and a slight flattening of the field to help reduce the development of hollow worn wheel) (see figure 7). “The biggest change overall was the shift from 2-point contact to single-point contact. [Wiener Linien] has already started to implement the new profiles and should be seeing the benefits shortly, if not immediately.”
Simulations of the new wheel and rail profiles compared to the old ones indicate that the overall wear reduction should be significant. The combination of improved curving, a repositioned contact patch, and reduced contact at the gauge corner and flange root provided a 3x improvement in simulations. “The wear number [a summary expression of traction and creep forces at the contact patch] went from 655 to 221—a three-fold improvement—under the new conditions in tight curves,” Prettner said.
Wiener Linien is still (as of September 2024) in the process of implementing these changes, but all parties involved in the project are confident that significant wear and damage reduction will be realized, Prettner said. He also pointed out that material design (like wheel and rail metallurgies and hardness) only plays a part in engineering an optimal wheel/rail interface. “You can do a lot with material alone, but if you want the best performance, other factors like complimentary wheel and rail profile designs are critically important.” The project also showcased how engineering know-how of transportation companies can successfully be supplemented by the expertise of external partners in a concurrent process of teamwork.

Jeff Tuzik is Managing Editor of Interface Journal.
This article is based on a presentation made at the 2024 International Collaborative Research Initiative.