Management and Maintenance: Capitalizing on Friction Modifiers
by Jeff Tuzik
Steel-on-steel friction is tricky. Frictional forces mediate every interaction between the wheel and rail. Too much friction, and the system wears too quickly; issues like noise, truck-steering, and wheel-climb become more prominent. Too little friction, and traction and braking are negatively affected. Friction Management (FM) is the art and science of finding the balance between these extremes; capturing the benefits of a low-friction operating environment with the fundamental requirements of traction and braking.
The early 2000s was a busy time for friction management. Many class 1 railroads ran their own internal economic validation studies on various friction modifiers. These studies provided favorable data, but in many cases didn’t translate well to large scale adoption and application, Marco Santoro, Global Friction Management Applications Manager at L.B. Foster, told those assembled at the WRI 2024 Heavy Haul Wheel/Rail Interaction conference. And in other cases, where larger FM programs were implemented, the programs weren’t always run and maintained to the requisite level (empty tanks, units not reinstalled after trackwork), leading sub-optimal performance. “In the industry, this raised a lot of questions about the efficacy of FM, itself, rather than the implementation and maintenance of the programs,” Santoro said.
In 2009, Mike Roney, then with Canadian Pacific, presented CP’s wholistic approach to “total friction management” to the International Heavy Haul Association (IHHA) This program looked at the costs and benefits of FM through a systemic rather than a departmental or adversarial lens. “This was the start of a better approach to FM on a large scale,” Santoro said.
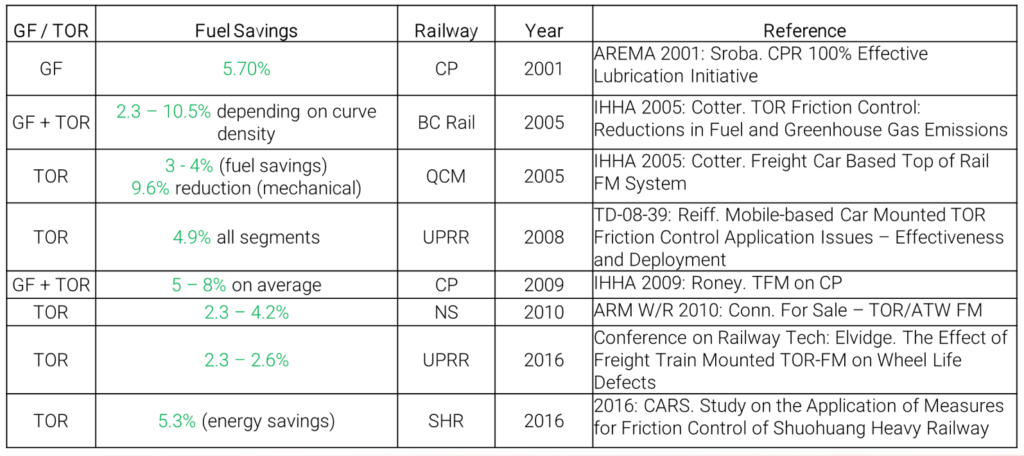
Since the early days of FM, multiple large-scale studies from various railroads around the world have shown the benefits of FM programs (see figures 1 and 2). These include fuel savings (typically in the 2% – 8% range, depending on baseline conditions), rail wear reduction (typically in the 20% – 50% range depending on measurement [top of rail, gage, or combined wear] and baseline conditions), lateral force reduction (typically in the 24% – 40% range), and a reduction in derailments per MGT.
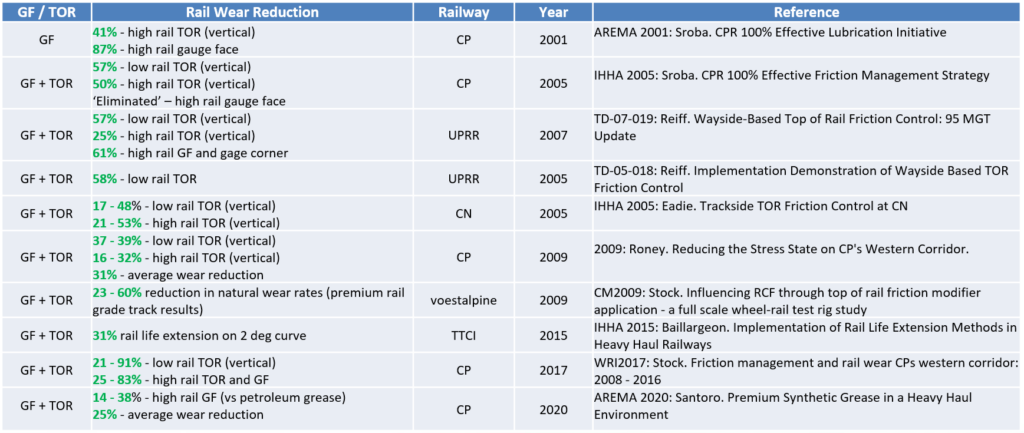
These are benefits that any railroad would appreciate. But, as Santoro said, friction management is not a set-and-forget solution. To realize the full range of benefits, the program must be managed, optimized, and maintained. And as many railroads can attest, there are challenges to implementing these large-scale programs, especially over the long-term.
One of the first challenges of implementing an FM program is securing the personnel required to inspect and maintain the applicator units. Some railroads dedicate personnel specifically to the FM program/wayside equipment, but often the task is given to track maintenance or track inspectors, on top of their many other duties, Santoro said. In such cases, it’s easy for FM equipment to be neglected as it’s often considered non-critical, and the benefits it provides are measured in a long time-frame; additionally, benefits such as fuel savings and lower lateral forces are effectively invisible to the maintenance worker. “When it comes to allocating manpower, short-term thinking tends to drive results,” Santoro said. Personnel assigned to the FM program also require training, specialized tools and equipment, and vehicles. This is a significant investment, and if the FM program lacks good management and a champion within the organization, it too, is often neglected.
Another challenge is the logistics of maintenance and track access. Often, wayside FM equipment is spread across hundreds of miles of track. It may be in difficult to access locations requiring long-distance hi-rail driving.
On the planning side, selecting the right FM product for the right location and environment is critical. Product characteristics like temperature tolerance, carry-down rate (the distance from the applicator at which the friction-modifying properties remain effective), and the rate at which it’s applied by the applicator are fundamental to the success of the program. “The product properties have much more of an effect on the long-term economics than the price of the product itself,” Santoro said.
Many railroads have now had FM programs in place for 15+ years. This has, relatively recently, brought up the challenges that come with repairing and replacing aging equipment in order to sustain optimal performance. “There are FM units out there that are up to 25 years old; those aren’t performing like they used to, and they’re definitely not performing like we expect a modern unit to perform.” These aging applicators require disproportionately more maintenance to provide comparatively poorer performance than their modern counterparts, effectively stunting the efficacy of the FM program as a whole.
Applicator pump assemblies, in particular, wear out over time. Their diminished output/application rate isn’t necessarily visible; so, without a plan for updating or replacing units and components, performance can suffer long before the unit fails, Santoro said. As part of a recent study presented at the International Collaborative Research Initiative (ICRI), L.B. Foster monitored top-of-rail (TOR) applicator output rates at the test locations. They found that on average, these units were applying product at roughly one tenth the target rate due to worn-out pump assemblies and applicator bars. “This isn’t providing a benefit in this state, yet it’s still taking up resources,” he said.
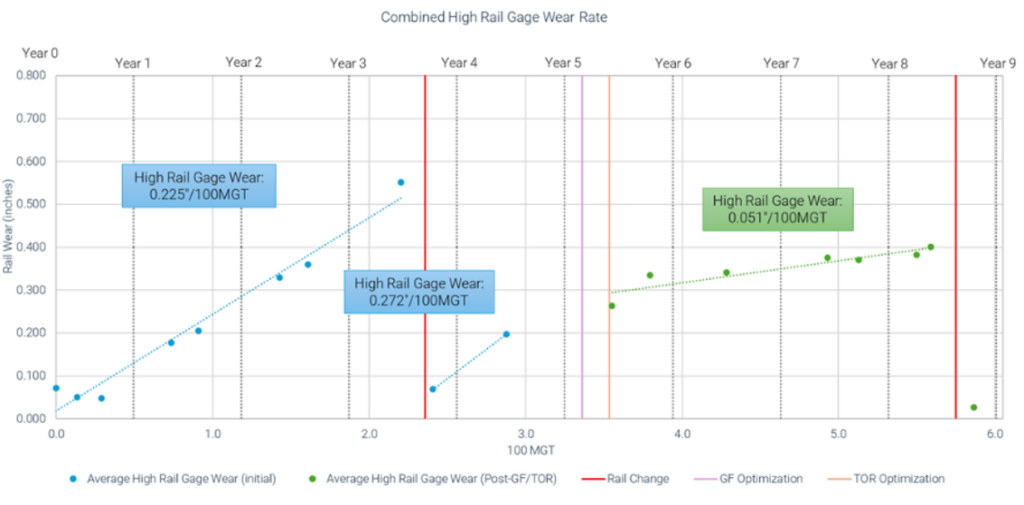
More modern applicator units partially alleviate this issue by monitoring (and remotely reporting) application rates. Remote performance monitoring allows maintenance personnel to know when a weak pump needs to be replaced, but also to adjust performance parameters as pumps wear out to ensure consistent application rates. Figure 3 shows example remote monitoring data from a class 1 railroad of applicator reservoir levels over time. The shallow slope of the blue line indicates a low application rate due to a worn or failing pump. The vertical purple line indicates maintenance intervention, and the green line indicates the corrected reservoir-depletion/application rate. This coincides with Figure 4, which shows wear rates on the gage face of the high rail at the same site. The correction made to the application rate lines up with a significantly decreased rate of wear on the gage face of the high rail. “Simply fixing the application rate dropped horizontal wear to a fifth of what it was,” Santoro said. “Whether it’s done remotely, or in the field, monitoring application rates should be part of routine maintenance.
Program Design
A commonality that the most successful FM programs share is a centralized team (or person) that takes ownership of friction management and can demonstrate and articulate the systemic impact of the program, Santoro said. “[The team] has to account for budgets, labor, equipment, validation—every part of the program—to make sure all the stakeholders are aligned.” Historically, railroads have done all of this, including maintenance of the applicator units, in-house. This approach has had varying degrees of success. “If you have somebody like Mike Roney looking over things, you can get great results. If you’ve got local section personnel who are bidding off the FM jobs, and no oversight, it’s not going to go well.” This variance in the efficacy of different FM programs has historically led some organizations to view friction management as insignificant—a belief that doesn’t benefit railroads or suppliers.
More recently—mostly within the past 10 years—railroads have begun to contract out portions of, or the entire FM program. These contracted programs are typically structured around one of three models.
The first is the use of third-party labor. Here, the contractors/laborers are fully trained in the refilling, maintenance, and installation of the FM equipment, but the program, equipment and inventory (such as FM consumables and applicator spare parts) is managed entirely by the client railroad. These arrangements lend themselves particularly well to large scale operations like bulk-filling numerous applicators, or working in tandem with railroad track gangs to uninstall and reinstall wayside FM equipment, Santoro said. To achieve the best results, this also requires a dedicated friction management team within the railroad that can manage logistics and monitor the program.
The second is the all-in model. In this case the contractor provides the labor, equipment, consumables, and monitoring of unit performance and up-time. The railroad still manages the program, but the contractor is responsible for applicator performance and up-time.
The third is the outside-management model; The contractor directly manages the FM program, including relevant railway personnel, in order to deliver a contractually stipulated FM unit uptime. The contractor is responsible for scheduling maintenance, inventory control, reporting and validation, training railroad personnel, and coordinating with track work and other activities that affect wayside and track-mounted equipment.
Regardless of which of these models a railroad uses, or if they choose to bring the program fully in-house, they should all involve performance monitoring and reporting, Santoro said. In addition to ensuring that the equipment is working properly, this data can also be used to identify and mitigate the causes of applicator down-time. Figure 5 shows a breakdown of system-wide applicator down-time for a class 1 railroad. This chart represents the roughly 15% of the time during which the units are not functional. Some of the down-time causes are largely immutable (track maintenance [44.0%], equipment damage [5.2%]) but others such as the low lubricant (16.5%) and equipment maintenance (21.0%) sections, for example, can be targeted and optimized, he said.
The benefits of a well-managed FM program versus an under-performing one have been documented in a number of case studies, including at previous WRI conferences. A 2017 study on Canadian Pacific’s Western Corridor (based on data collected from 2008 to 2016) compared wear on the high rail in curves within CP’s “Total Friction Management” (TFM) program to similar curves that were nominally equipped for friction modifier application, but weren’t monitored and maintained to the same level. In one instance, the high rail of a 6-degree curve within the TFM program (with TOR and gage-face FM) showed a 38% decrease in vertical wear and a 50% decrease in gage wear versus the non-TFM 6-degree curve (with only gage-face FM).
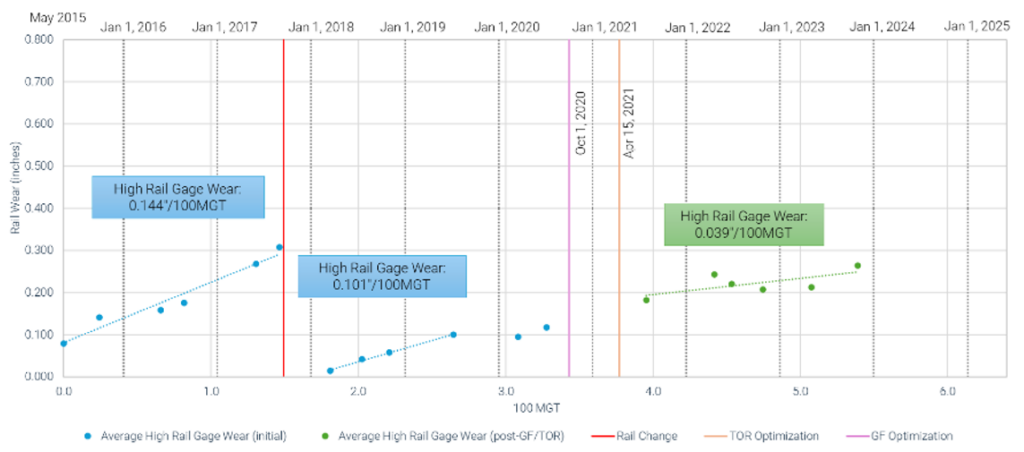
Since that study, the previously non-TFM curve was brought within the TFM envelope; the curve now has TOR friction modifier, gage-face lubrication, and is maintained to above 90% up-time. Figure 6 shows wear rates for this curve both pre- and post-TFM implementation. Prior to TFM implementation, gage wear was ≈0.14 inches per 100 million gross tons (MGT). Post-TFM, the wear rate dropped to ≈0.04 inches per 100 MGT.
Friction management programs have a lot of moving parts; they can be difficult to implement and perhaps more difficult to maintain. Nonetheless, data supports the effectiveness of these programs and class 1s are taking advantage of them. The key to maximizing the benefits is to understand friction management as a part of the system, rather than an ancillary component. Like any other part of the railroad, its optimization requires proactive management and maintenance.

Jeff Tuzik is Managing Editor of Interface Journal
This article is based on a presentation made at the 2024 Wheel Rail Interaction Heavy Haul conference.