A First Look at Rail Milling in North America
By Richard Stock
Rail Milling technology, which was introduced by Linsinger about 25 years ago, has been widely used in Europe, Asia, and Australia. It was recently introduced in North America. Unlike other maintenance technologies, rail milling is a non-abrasive cutting process where material is cut from the rail surface in the form of chips. A typical milling machine utilizes one to four cutting tools per rail (depending on the size of the machine); a subsequent polishing unit is used to create a smooth, high-quality surface finish. The by-products (chips) are collected on the machine and can be recycled, providing an added environmental value to the technology. Linsinger machines can be equipped with state-of-the-art measurement technology such as transversal profile, metal removal, longitudinal profile and electromagnetic crack measurement systems. Linsinger rail milling machines are self-propelled and come in various sizes and configurations to meet customer-specific requirements from light rail to heavy haul.
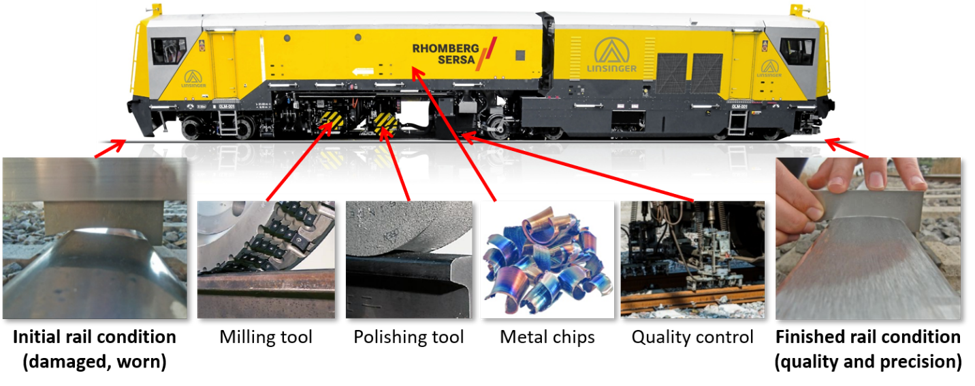
Figure 1: Key components/steps of the milling process, Linsinger high capacity transit milling machine SF02T-FS.
Rail milling has a number of advantages over conventional rail maintenance technologies. Due to the variable low to high one-pass metal removal capability – as little as 0.1mm (0.004in); as high as 10mm (0.4in) dependent on machine size – rail damage can be completely removed, and the profile can be fully restored. The spark- and dust-free process creates a very accurate rail profile with a high-quality surface finish and leaves no metal chips or other waste material on the track. Despite its ability to remove relatively large swaths of metal in a single pass, the milling process imparts little heat into the rail; the heat is absorbed by the chips and the cutter heads. As a result, the rail surface experiences no significant increase in temperature, which prevents unwanted material transformations such as bluing and the formation of martensitic layers. Rail milling can accurately produce any type of required rail profile. Milling operations using multiple profiles, such as CPC, CPG, CPF, have been performed on railways in Australia and North America. It is also possible to treat switches and crossings along with mainline track with the same milling machine, eliminating the need for a dedicated switch and crossing machine.
A key feature of the milling technology is the high output in feet/minute of finished and regenerated track. Other maintenance technologies might operate at a higher speed per pass, but they require a multitude of passes to finish a specific track segment, thereby drastically reducing the overall output in feet/hour. Rail milling can regenerate the track in one or a maximum of two passes, resulting in a high output of finished feet/hour. Railways around the world have established specifications for milling that are dependent on the required metal removal. These specifications usually do not consider other factors like the elimination of fire danger and the absence of any dust emissions — considerations that favor the use of rail milling over other technologies, especially in tunnels, stations and on bridges / elevated structures.
Rail Milling in North America
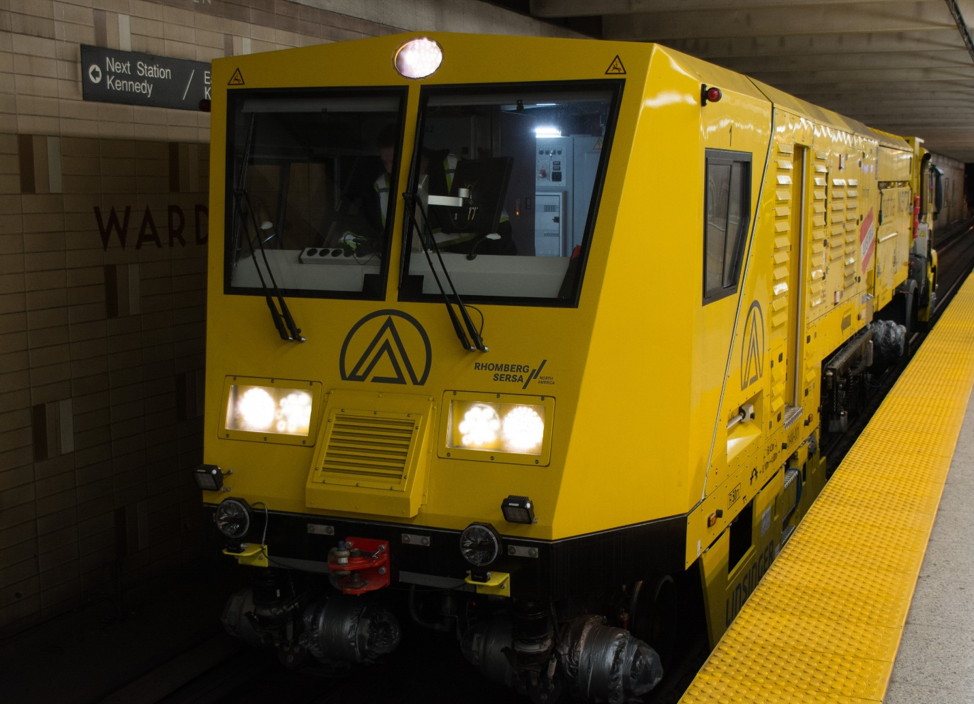
Figure 2: Linsinger milling truck SF02W-FS operated by Rhomberg Sersa North America at Warden station in the TTC subway.
The Toronto Transit Commission (TTC) operates four subway lines with a total system length of 48 miles. More than 220 million passengers used the network in 2018. The TTC assessed milling technology for several years before publishing the first milling service tender in North America in late 2017. With respect to rail milling, the TTC is targeting locations that have not been ground or could not be corrected by grinding for various reasons. Like many rail transit systems, the TTC’s primary issues relate to corrugation, rolling contact fatigue (RCF), and profile degradation. The use of a spark- and dust-free technology was an important benefit for TTC. The need to clean up stations, and the delays or shutdowns due to potential fires after rail grinding could be completely avoided by rail milling.
In mid-2018, the TTC awarded a five-year milling tender to Rhomberg Sersa North America, which is part of the Swiss-Austrian Rhomberg Sersa group. With the award of this tender, Rhomberg Sersa ordered a specifically adapted SF02T-FS railbound milling machine from Linsinger. This high-capacity transit milling machine, which was specifically adapted to fit most of the North American tunnel clearances and is equipped with the latest diesel-electric milling technology, can remove as little as 0.004 in. (0.1mm) and as much as 0.06 in. (1.5mm) of material in one pass. The chip bunker capacity is designed to operate continuously for six hours without the need to empty the chips. The machine can also carry several spare pairs of milling tools and allows for tool changes in less than 10 minutes. As this machine will not arrive in North America before November 2020 (it will be on display at the Innotrans trade show in Berlin in September 2020), Rhomberg Sersa leased a SF02W-FS milling truck from Linsinger to start the milling work at the TTC in December 2018. The truck (as well as the train) had to be equipped with a re-railing device to quickly put a derailed machine back on the track in the space-constraint tunnel environment of the TTC. The machine was also equipped with a coupling adapter to tow the machine in the event of a breakdown. The street wheels as well as some side covers had to be removed from the truck in order to fit within the TTC’s third-rail clearance profile.
For the milling operations, the TTC reduced the number of rail templates used on the system from five to two — tangent and high rail curve templates designed by the National Research Council of Canada (NRC) — for the first year of milling operations. The milling tool (also called the cutter head) is designed to provide conformity to the profile template. Unlike rail grinding, a 100% match between the resultant rail profile and the rail template can be achieved with milling technology. Sensors on the milling machine determine the highest point on the rail and the gauging point. The cutting tool is adjusted in reference to these two points to achieve the desired metal removal, restore the rail shape, and prevent any unwanted gauge widening. Even severely deformed/worn profiles can be efficiently treated with this technology.
The TTC determined the locations and the required profiles for the milling program based on the existing track condition data. The focus in year one was to remove damage and establish the appropriate profile by treating entire segments between two stations. Since the milling truck was not equipped with onboard measurement technology, the milling work was performed in a one-pass operation with 0.8mm metal removal, with spot checks of the profile done behind the milling machine. Sites requiring a second pass will be addressed in subsequent years. Following this strategy, a full or partial profile cut was performed, depending on the existing profile conditions. At locations where two passes would be needed, the first pass would restore the general profile shape, the second pass would remove the remaining damage and achieve the final profile. A special milling procedure was used to optimize the shift output and to avoid the need for milling tool changes during the shift. On shifts in which the milling head for tangent profiles was being used, for example, track segments requiring the high rail template were skipped. The skipped sections were then milled during a subsequent shift when the milling head for the high rail template was in place.
Several challenges had to be addressed during the first year of rail milling at the TTC. These include:
— There is a tendency to try to make an “apples-to-apples” comparison between milling and grinding. It’s important to understand that milling is fundamentally different from grinding technology, and planning and operation practices will be different.
— Rail milling is a uni-directional process. This must be considered when planning the equipment’s approach to a work site when continuing on from where the previous shift’s operation had stopped.
— The planning process went through several optimization steps to deal with last-minute program changes and the fact that milling can efficiently treat whole track segments and not just work on hot spots (as rail grinding typically would be used).
The first milling operation in North America completed 36 shifts during the first year at the TTC, despite losing about two weeks of shifts due to extremely cold weather (and the TTC cold-weather protocol). About 11.1mi (17.2km) of track were successfully treated. Due to capacity constraints at the TTC, year two of the milling program was postponed and will be added to the work scheduled in year three, at which point the new SF02T-FS milling train will be available. Expectations are that year three of the TTC contact will be complete by mid-year 2021, after which the milling train will be available for further work in North American transit systems and Class 1 railroads.

This article is based on a presentation made at the Wheel/Rail Interaction 2019 Rail Transit Conference.
All photos and graphics courtesy of LINSINGER.
Richard Stock is Milling Technology Manager for LINSINGER Austria and LINMAG Rail Milling.