Data to Decisions: Tools and Technology to Manage Wheel/Rail Interaction
WRI 2014 Heavy Haul: Part 1
by Jeff Tuzik
A lot has changed since the early days of wheel/rail interface management. New technologies present new opportunities and challenges, while legacy systems are continually honed and adapted to new practices. Automated inspection technologies and data management are only the latest in decades worth of innovation.
“There have been game changers, and there have been missed opportunities,” Mike Roney, Chair of CPCS, Transcom, and recently retired from Canadian Pacific, told participants at WRI 2014, the 20th annual Wheel/Rail Interaction Conference.
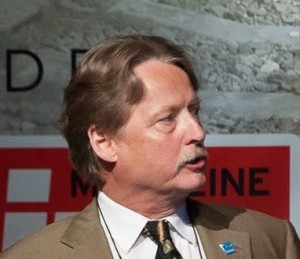
One of the most significant advances in wheel/rail management has been the widespread adoption and implementation of preventive rail grinding. By periodically grinding the rail in order to maintain conformal contact and proper profile, damaging conditions can be corrected before introducing further damage and wear into the system, Roney said. The move from reactive to preventive grinding is in part attributed to the work of Joe Kalousek, who coined “the magic wear rate” to describe the optimal frequency of rail grinding necessary to minimize wear.
Preventive grinding didn’t catch on immediately, but it has since become a common practice. “Joe Kalousek made a believer of me,” Roney said. “We learned our magic wear rate.”
Gauge face lubrication and automated lubricators have come a long way too. But they’ve yet to be perfected. “On a good day, 70% of my lubricators are working,” Roney said. While 70% may appear to be good enough, intermittent application of lubrication – a cycle of dry and lubricated rail – can be problematic. Dry cycles set up a matrix of small surface cracks which are susceptible to hydraulic cracking when lubrication is reintroduced to the system.
Top of rail (TOR) friction modifiers have a shorter history than lubrication, but are now a major component of wheel/rail interface management. TOR friction modifiers are designed to provide an 0.3 to 0.35 coefficient of friction at the top of rail – a “sweet spot” that maximizes traction and braking while mitigating damaging lateral forces. “There’s no debate any more about whether TOR reduces lateral forces. It does,” Roney said.
But TOR is not a cure-all for high lateral forces. The efficacy of TOR friction modifiers is dependent on many factors, including distance from the applicator, TOR material characteristics, and whether the wheels are in heavy flanging mode. The lateral force reduction that TOR provides is also largely dependent on the use of three-piece trucks. “Railroads around the world that use steerable trucks are probably not going to see the same benefits,” Roney said.
Automated measurement and monitoring systems are among the newer technologies in the heavy-haul environment, but their effect on maintenance and planning has been profound. These systems include:
- wheel impact load detectors (WILDs)
- truck performance detectors (TPDs)
- truck-hunting detectors
- hot/cold wheel detectors
- acoustic bearing detectors
- brake shoe wear monitors
- wheel tread profile monitors
These monitors and measurement devices, among others, began as additional layers in the safety net. They have over time evolved into diagnostic and planning tools, as well.
Wheel Impact Load Detector (WILD) data, for example, can be used to trend wheel wear to better schedule repairs. Track geometry data can be used to trend rail wear and predict renewal cycles, as well as simulate wheel performance, said Sean Woody, Manager of Track Inspection and Development for Norfolk Southern.
“We started out using this technology to catch catastrophic failures,” said Gary Wolf, President of Wolf Railway Consulting, who moderated a panel on automated inspection systems. “Now we use it to lower our asset lifecycle costs. We moved from reactive to proactive maintenance strategies.”
Automated inspection is still an important part of safety and regulatory compliance. And some automated systems in use today have a fairly straightforward alarm-type function, such as hotbox detectors, high- and wide-load detectors and dragging equipment detectors. The FRA requires automated crosstie inspection in concrete tie territory, as well as automated rail flaw detection.
But in cases in which it is not specifically mandated, use of automated technologies nonetheless is often the most cost effective and efficient way to achieve regulatory compliance, Wolf said.
Many of these “game-changing” technologies played a role in solving a problem of premature wheel wear on Amtrak, in the early 2000s.
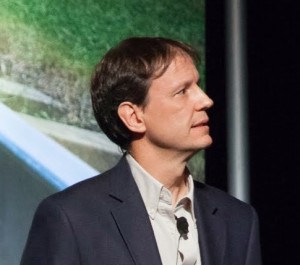
“The wheel-wear issues on Amtrak really gave us a good opportunity to take a systemic view of wheel/rail interaction,” said Eric Magel, Principal Engineer, Rolling Contact Fatigue at the National Research Council (NRC).
In 2003, after a series studies, the NRC provided Amtrak with five rail profile templates designed to improve contact mechanics and minimize wheel tread and flange wear. The new profiles were implemented gradually throughout the system, giving the NRC the opportunity to fine tune the profiles and rail grinding practices over several years.
“Wheels and rails will always be subject to plastic flow, rolling contact fatigue (RCF) and wear. They have to be maintained on a regular basis even with the best profiles,” Magel said.
Friction management was another part of the solution – both gauge face lubrication and TOR. The NRC evaluated lubricants and lubricant applicators. A study on the carry rate of different lubricants showed a wide variance in performance. One product carried only 1.9 miles, while another carried 5.6 miles. “It turned out that the most expensive grease was the most economical, because of the performance,” Magel said.
A system review of the track indicated that 25 lubrication applicators were optimal to treat 314 miles of track.
Then the NRC instrumented track in a 7-degree curve for several months in order to measure the effect of TOR and gauge-face lubrication on lateral forces and the lateral/vertical ratio (L/Vs). With lubrication alone, the data showed an increase in L/Vs and lateral forces. “The lubrication has reduced the steering moment,” Magel explained. The combination of TOR and lubrication, however, showed a reduction in lateral forces and L/Vs in comparison to both dry, and rail with only gauge-face lubrication.
The final piece of the puzzle was an optimized wheel profile design: the higher-conicity NRCC wheel.
“Before the NRCC, flange wear was a big problem. We had to re-true very frequently,” said Gary Jackson, Sr., Senior Engineer of Wheel Diagnostics at Amtrak. “After the NRCC, very little of the maintenance was due to flange wear.”
Field testing showed that the Amtrak Standard wheel had to be pulled out of service due to flange wear at 150,000 miles, while the NRCC wheel was pulled out closer to 300,000 miles. Implementation of the NRCC wheel had a profound effect on lifecycle costs. The Amtrak fleet went from seven months between truing cycles (with the Amtrak Standard wheel) to 14 months (with the NRCC wheel). In addition, truing the NRCC wheel required only half the metal removal versus the Amtrak Standard wheel, effectively doubling wheel life.
“Amtrak provided an opportunity to do a vehicle/track system optimization. It showed that friction management and selecting the proper wheel profile are very important,” Magel said.
The Amtrak experience highlights the synergy between technologies that has developed over years of use. But there are many new technologies on the scene that while promising, have yet to find their niche.
“Any new technology needs testing and investment to see the benefits,” Gary Wolf said. “We need some push there — grants and research money.”
The Draisine and the MRX Rail Surface Crack Measurement System are two relatively new RCF-related crack-measurement devices, both of which were the subject of recent validation studies by Norfolk Southern.
The Draisine uses eddy current to inspect rail flaws that are open to the surface. It measures crack length, then calculates the depth of the crack based on an assumed crack angle, which is operator definable. The Draisine’s four measurement probes are adjustable and cover about a third of the rail head, so knowing where to place the probes in order to find the worst cracks is critical, said Brad Kerchof, Norfolk Southern’s Director of Research and Tests.
The MRX measures using magnetic induction – artifacts in the rail are detected by their disruption of the induced magnetic flux. The MRX further differs from the Draisine in that it covers the entire railhead with a total of 19 probes, spaced 5mm apart.
In 2013, NS used the Draisine to measure RCF cracks in the low rail of a 5-degree curve. Using an assumed angle of 25 degrees, the Draisine indicated significant RCF, with crack depths up to 5 mm. NS then ground the rail, making five passes and removing 1 mm of material from the railhead. The Draisine’s post-grind results showed the RCF to be nearly eliminated, including the cracks that were described as having a depth of 5 mm. The discrepancy between measured damage depth and metal removed indicated a need for additional research, including how crack angle should be determined.
NS also used the Draisine on a high rail. After the crack measurements were taken, a rail section was removed from track, and cross sections cut and examined under an electron microscope. In this instance, the Draisine results compared favorably with actual crack depth measurements: the Draisine predicted a damage depth of 1.9 mm, close to the actual crack depth of 2 mm. This successful outcome was likely due to the actual crack angle measuring 25 degrees – the same as the assumed angle.
In 2014, NS provided a low rail for validation testing of both the Draisine and the MRX. Crack depth was measured by both devices, after which several rail sections were removed from track and taken to the lab for cross-section analysis. The success of the Draisine was determined by how close actual crack angles were to 25 degrees. One sample, which had similar angles, also had similar damage depth; the 1.8-mm crack depth reported by the Draisine was close to the 1.3-mm actual depth. With the second and third samples, the crack angles were significantly less than 25 degrees, and the Draisine over estimated damage depth: Draisine predictions of 3.5 mm and 4.8 mm were significantly greater than actual crack depths of 0.5 mm and 1.5 mm, respectively. One near-horizontal crack that was 8 mm in length was missed entirely by the Draisine, because its entrance at the rail surface was not within the active area of any of the Draisine’s probes. Additional probes can be added to alleviate this issue.
The MRX system examines the entire rail head and reports the deepest depth of artifact detected, Kerchof said. However, the results were difficult to validate. “It was unclear which artifact the measurements referenced,” he said. Like the Draisine, the MRX tended to over-estimate crack depth, in some cases significantly so. MRX results were compared to three of the cross-sectioned samples. In two cases the MRX predicted a crack depth that was two times the actual depth — 3 mm vs. 1.5 mm was typical. The third sample had a much greater difference — MRX reported 7 mm when the actual depth was 1.5 mm.
“The Draisine’s raw data predicted crack length, but that crack depth is a less reliable measurement when crack angle varies. And more work is needed with the MRX to correlate its data with actual cracks,” Kerchof said.
The ability to accurately measure RCF remains an issue of primary concern. All of the premium rails used in the Transportation Technology Centers Inc.’s (TTCI) Facility for Accelerated Service Testing (FAST) test track, for example, have now developed RCF. “So there’s room to improve,” Mike Roney said. And questions remain on how to best measure and characterize RCF cracks, whether by length, depth, density or angle.
New technologies like the Draisine and the MRX are at one end of a spectrum, but management of wheel/rail interaction doesn’t necessarily have to be a high-tech endeavor.
Low speed derailments in industrial yards are dangerous and costly events, but preventing them can be both low-tech and low-cost.
“If I had spent more time investigating every incident, I would have had less of them,” said Norm Hooper, Principal of Hooper Engineering. “This is some hard won knowledge.”
Some of the most dangerous yard derailments involve tank cars. Differences in track crosslevel are transferred corner to corner on tank cars and can completely unload a wheelset. Tank cars are particularly susceptible to this due to their stiffness and length, Hooper said. Tank cars are also vulnerable to rollover due to their double-shelf couplers, which are designed not to come apart in order to prevent inadvertent puncture of forward or trailing tank cars. The downside to the design is that if one tank car rolls, it can roll an entire string of cars.
One of the simplest ways to minimize rollover risk is to pay close attention to side bearings, which are a major contributor to wheel climb and gauge-spread derailments, he said. “When we went after wheel climb derailments on tank cars on my railroad, we bad-ordered 40% of the tank cars to fix the side bearings back to AAR standards.”
Poorly maintained switch points are another common cause of yard derailments. A Samson point switch with an undercut stock rail can reduce the risk of split-switch and wheel climb derailments. The combination of a new switch point on worn rail can leave the point exposed and vulnerable to splitting.
The list of fundamental steps required to improve wheel/rail interaction and reduce derailment potential includes a number of low-tech, but fundamental practices:
- Proper ballast
- Proper drainage of the trackway
- Joint bar and bolt inspection
- Clear flangeways at crossings
“Keep in mind that track in industrial yards probably has more curvature and more difficult geometry than the Class 1 that delivered the car,” Hooper said.
Big Data
The sheer amount of data that automated inspection systems now collect presents both challenges and opportunities. The opportunities lie in trending, automated analysis and informed decision-making. The challenges lie in moving, storing and simply knowing how to use the data.
Machine vision is one of the technologies at the cutting edge of automated inspection today and it cuts across track and mechanical departments. But machine vision and other imaging technologies can be difficult to manage due to the amount of data they typically generate. It’s not uncommon for a single vehicle with multiple inspection devices to generate 100gb of data per day, said Ryan McWIlliams, Chief Technical Officer of International Engineering.
The proliferation of new automated inspection technologies has also given rise a to belief that if something can be measured, it should be measured. “I don’t think that’s necessarily true,” said NS’s Sean Woody. “You have to know how to summarize the data first, how you piece it together from multiple sources.”
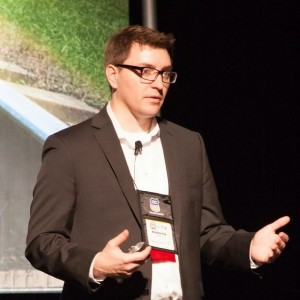
The difficulty of having so much data, is knowing how to turn it into actionable information, and how to make decisions based on that information. “Data and decision management are the biggest things we’re going to face for the next couple decades,” said Matthew Dick, Staff Technical Officer at ENSCO. “Ultimately this could lead to game-changing efficiency gains.”
One of the earliest examples of turning raw data into information was the development of the 90-kip standard for WILD systems. The standard was the result of attempts to quantify the amount of damage a high-impact wheel would cause, versus the cost of replacing the wheelset. “We found that 90 kips of wheel impact, loosely related to $432 worth of track damage, which was the average cost of replacing the wheelset,” McWilliams said. “Hence, it made sense to replace that wheelset at the 90 kip level and prevent additional track damage.”
CN leveraged data from its network of WILDs to develop an automated load imbalance or overload detection system, said Bill Blevins, Chief Mechanical and Electrical engineer at Canadian National. “Some of the automated messages are just alerts, other times we get stop alarms. We’ll stop the car en route when we get a stop alarm,” he said.
Another example of turning data into information was ENSCO’s development of an algorithm to predict potential derailment sites based on previously-collected data. “There was no added hardware, just software using data that was already there,” Matt Dick said. “We found a pattern of repeated low level exceptions of different types. So we wrote an algorithm that searches a huge database to try to find that pattern and report it back.” Shortly after its implementation, the algorithm predicted a derailment two weeks before it occurred.
The possibility that certain data may be able to predict catastrophic failure brings up issues of liability. With the overwhelming amount of data across so many systems, railroads have voiced concern that they could be held liable for failing to act on information they didn’t know they had. “If they have the data and don’t know what to do with it, could they end up in court?” asked McWilliams.
As the industry increases its use of automated inspection technology, the amount of data and the problems associated with data management and analysis will grow – a prospect that must be confronted in the near future, Matt Dick said.
All the information in the world is useless if it’s not in the right hands.
The question is: outside of conferences like Wheel/Rail Interaction (WRI) and publications such as Interface Journal, how does the information get out? One way is for two of the primary industry associations to get involved. The American Public Transportation Association (APTA) and the American Railway Engineering and Maintenance-of-Way Association (AREMA) took advantage of WRI 2014 to announce the renewal of their memorandum of understanding to jointly investigate the wheel/rail interface.
APTA’s, Passenger Rail Equipment Safety (PRESS) group began working with the Federal Railroad Administration (FRA) in the mid 1990s, publishing standards on:
- wheel profile and flange angle
- truck unloading and load equalization
- vehicle structural design
- crash worthiness
- couplers
- axles
The AREMA and APTA relationship developed when the APTA Track and Noise/Vibration Technical Committee within APTA began to examine urban track design. The group worked with AREMA to study issues like embedded track, sharp curves and special trackwork and clearance envelopes.
Years of study and analysis have gone into wheel/rail interaction in both the heavy-haul and transit industries. The APTA/AREMA relationship seeks to promote the exchange of information across industries. “There’s a lot of information in this [railroad] industry. I think we can share with the commuter rail world. Issues of wheel/rail interaction,” said Martin Schroeder, Chief Technology Officer of APTA.
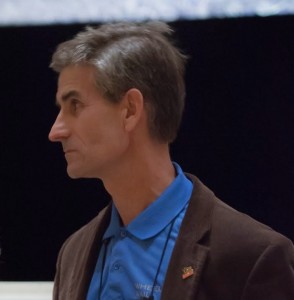
And the exchange of information flows both ways. “There’s a lot information, and not everybody knows what the other guy is doing. The more collaboration there is, the stronger the railroad is,” said Joe Smak, President of AREMA.
It is an often repeated mantra in the railroad industry that the compartmentalization or siloing of information leads to a weaker system overall. The WRI Conference has worked to break down that compartmentalization by providing a forum for discussing wheel and rail as a single system, said Gordon Bachinsky, President of Advanced Rail Management Corporation and founder of the WRI Conference. “We’ve tried for many years to have this conference be a place where we can come from our disparate places and discuss these issues.”
By that measure, the conference covered a lot of territory. But there’s still a long way to go.

Jeff Tuzik is Managing Editor of Interface Journal