New Approaches to Dynamic Wheel Force Measurement – Part 2
by Jeff Tuzik
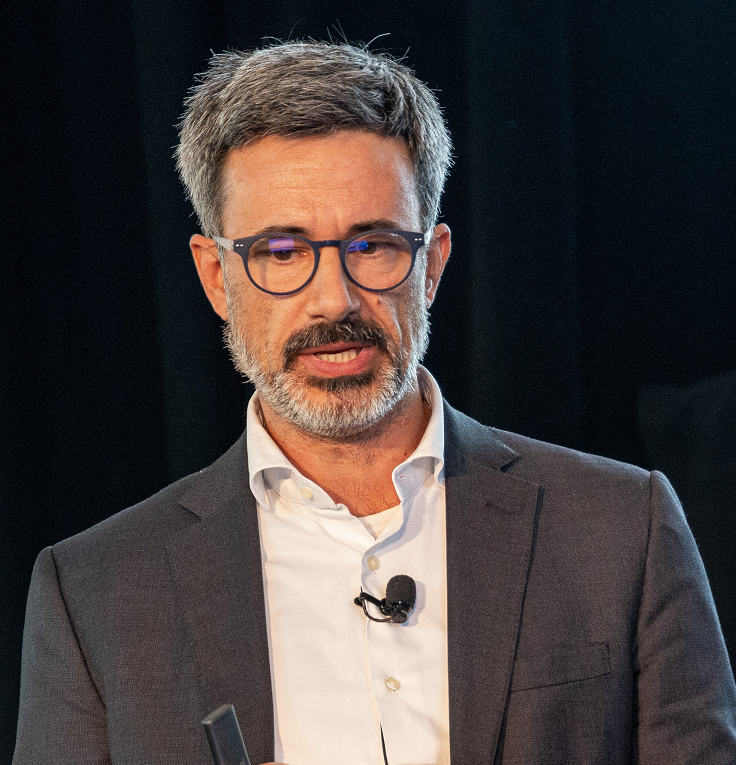
Part 1 of this article focused on past and present research into wheel condition and behavior monitoring via wayside-based continuous measurement systems. Using an overlapping combination of strain gauges and load cells, such systems can measure a wide range of dynamic wheel forces, and parameters like wheel circumference and out-of-roundness. Some of this data can also be gleaned through specialized analysis of strain gauge data without requiring additional hardware – a technique called the Composite Unit Method.
Other wayside measurement devices take a different approach to measuring parameters like wheel out-of-roundness and lateral stability/hunting propensity by way of equivalent conicity (EC). Mermec, for example, has developed several optical/laser-based continuous measurement devices capable of performing many of the same functions as the Train Performance Detection System (TPDS) that MxV Rail’s Yuqing Zeng detailed in part 1.
Calculating equivalent conicity requires a number of data points on various wheel and track parameters. These include: left and right wheel profile, back-to-back distance, wheel diameter and diameter difference, rail profile and track gage. “A single wheelset with a high EC value is unlikely to cause hunting, but multiple wheelsets [in a consist] with high values are a strong predictor of hunting,” Enrico Betterle, Product Manager of Wheelset Monitoring Equipment and Data Analysis at Mermec, said at the 2023 Wheel/Rail Interaction conference. This highlights the importance of capturing data on every wheel that passes through the wayside unit, and ensuring that there are no “dead zones” or gaps in the data.
Based on this information, Mermec developed a hunting prediction indicator (see figure 6) based on the percent of wheelsets with EC values exceeding a given threshold (based on operating speed and other operational parameters). This predictive indicator has been validated by one case study in 2022; additional studies are currently underway, Betterle said.
Mermec has also applied its optical wayside system to monitoring wheels for early signs of out-of-roundness. There are many ways to measure OOR wheels, including force detection/ WILD systems like those detailed by Zeng, contact-probe systems like underfloor wheel lathes, and machine vision tread-imaging systems. One drawback of force detection/WILD systems when it comes to OOR measurement is that if a defect occurs outside of the contact band of the wheel, the system can’t detect it, Betterle said.
An alternative method under development by Mermec employs an optical profile-based method to gather in-service OOR data. This method is based on a statistical, cumulative buildup of full circumference data over the course of multiple passes through the inspection unit, Betterle said. Each wheel that passes through the unit is measured at 4 random points around the circumference; after 15 passes, 70% of each wheel has been measured; after 20 passes, there is 80% coverage, and after 45 passes there is greater than 95% coverage. Because this is a statistical method, the final OOR value is the maximum value detected over a certain number of inspections. “The limitation of this approach is that the measurement unit must be installed somewhere that sees very frequent train passages,” Betterle said. The strength of the system, on the other hand, is that measurement covers the entire transversal tread profile, making it easier to locate defects occurring outside the contact patch. Betterle also cautioned that at this stage, this method should not be considered a substitution for established OOR detection practices, but rather an additional dataset that can be integrated with other wheel condition data.
A New WILD
In addition to the ongoing refinement of continuous measurement systems like those developed by MxV Rail and Mermec (and others), the railroad industry has also sought development and validation of alternative WILD technologies in recent years. A June 2021 update to AAR S-6101: Detector Validation and Calibration Requirements specified onboard measurement of wheel impact loads using instrumented bearing adapters. This specification is based on AAR member experiences with carbody dynamics testing and based on the assumption that reaction at the bearing adapter should equal force at the wheel/rail contact patch.
Figure 7 shows the layout of the instrumented bearing adapter, which features four parallel load cells. After adding half of the axle weight, the sum of the load cells represents the wheel load, Zeng said. Each instrumented adapter was connected to one high-impact wheel, and the test consist was made up of both loaded and unloaded cars.
Test results (see figure 8) showed that axle static loads (adapter force in kips) matched scale weight within approximately 5%, but that onboard peak loads were well below the high-impact wheels’ historical WILD data. To determine the reason for this large discrepancy, a free boundary 4-degrees-of-freedom model was built; “Based on the model, you can obtain the transfer function from the force on the wheel/rail contact patch to the bearing adapter, and the measured value can be corrected based on that function,” Zeng said. But the transfer function is dependent on many vehicle characteristics, and this method provided inconsistent results, he added.
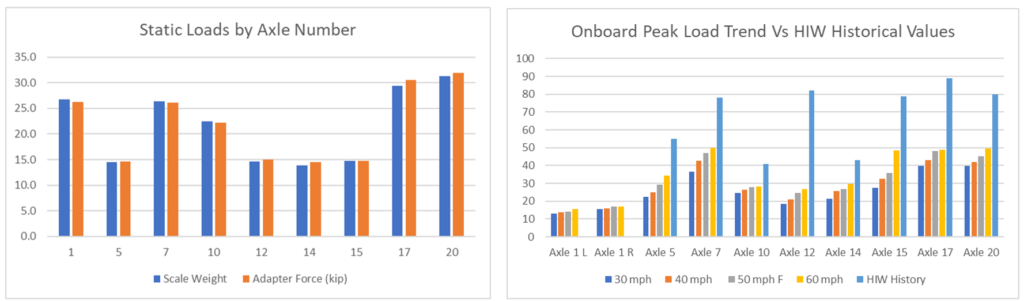
This is an ongoing project and MxV Rail continues to refine their bearing adapter measurement concept based on their experience with IWSs. One step that could help set a baseline for measurement and validation of the instrumented bearing in the future, is to engineer a specific high-impact wheel whose specific characteristics could be benchmarked with IWS and wayside measurements, Zeng said. This would help eliminate some of the variables that complicated initial testing. It’s also important to determine the extent to which bearing adapter force data corresponds to the likelihood of component damage and failure rates in the way WILD data does.
Wayside measurement systems have become increasingly sophisticated over the years. While the traditional WILD continues to be an invaluable tool, the development and implementation of continuous wheel/rail force measurement technology promises a tremendous amount of useful data on wheel condition and on wheel/rail interaction. While such systems may never fully replace the reliable WILD, it seems likely that they will continue to expand their niche as they become more sophisticated and more economical.

Jeff Tuzik is Managing Editor of Interface Journal.
This article is based on a presentation made at the WRI 2023 Heavy Haul conference.