Vehicle, Track and Wheel: Safety and Efficiency at the Wheel/Rail Interface
WRI 2014 Heavy Haul: Part 2
by Jeff Tuzik
Wheel/rail interaction impacts virtually every aspect of railroading, including operational safety and efficiency, the effectiveness of vehicle and track maintenance and maintenance planning. WRI affects the bottom line, too. When things go wrong, the culprit is often somewhere within the interface. Part 1 of this article explored the tools and technologies of wheel/rail interface management. Part 2 looks at the ways in which all parts of the system must work together, and what can happen when they don’t.
“Looking at wheel/rail interaction, we have to keep in mind that the suspension, bogie, vehicle and track are all a system,” said Jay Monaco, Vice President Engineering, Amsted Rail. “Each of those systems has to be balanced against the others in order to optimize the whole thing.”
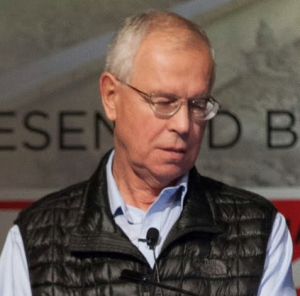
Joe Kalousek, former principal researcher at the National Research Council of Canada, presented at the first WRI conference 20 years ago. (Photo courtesy of Jack Lindquist.)
Twenty years ago, at the first WRI Conference, Joe Kalousek, former principal researcher at the National Research Council of Canada, laid out the complexity of wheel/rail interaction. His work over the years has influenced the discussion of wheel and rail wear, rail grinding, profile design, friction management and, as a result, the system as a whole.
Preventive rail grinding (See Part 1) has dramatically affected the way railroads manage wear and rail life. The “magic wear rate,” coined by Kalousek, is the guiding principle for that type of grinding. The magic wear rate is the rate of wear at which any rolling contact fatigue (RCF) cracks in the initial stages of development are removed, either by wear or through preventive grinding. “The lower the natural and artificial wear that controls rolling contact fatigue, the greater the rail life and the magic,” Kalousek said.
Kalousek was among the first to research and champion the use of the use of top-of-rail (TOR) friction modifiers to help manage wear and achieve the magic wear rate. Their use has since become ubiquitous.
“As far as I’m concerned, Dr. Joe Kalousek is the father of TOR friction modification,” said Don Eadie, Vice President, Technology and Innovation at LB Foster Rail Technologies Corp. “Joe pointed out the potential opportunities and benefits in the early 1980s.”
The history of TOR friction management is not a long one. The first commercial application was in 2000, with Kelsan’s family of Keltrack materials. Railroads were skeptical at first, particularly with regard to braking and safety concerns. Class 1 railroads also had difficulty figuring out where TOR fit into their operating budgets. Canadian Pacific determined that it could make a business case for TOR friction management, and allocated money saved from fuel conservation from the fuel budget to pay for a TOR program, Eadie said.
Over the past few years, the benefits have become widely accepted and the safety concerns have all been addressed. The challenge of TOR friction management today is in increasing efficiency and lowering costs.
When wayside TOR was first deployed, applicator units were typically placed at two-mile intervals, Eadie said. Further spacing means better economics, but the ability to do so and retain the benefit of friction management is dependent on the efficacy of the material.
Today there are three broad types of TOR materials. Water-based “dry film” (which make up the vast majority of use), oil-based, and hybrid materials. TOR friction modifiers, unlike lubrication, are design to achieve a certain coefficient of friction, typically between 0.3 – 0.4 and maintain it at that level.
Lubricants have a much lower coefficient of friction and, as a result, a much higher carry-rate. So one way to get a higher carry rate on a friction management product is to lower the coefficient of friction. But there are tradeoffs in safety and performance, Eadie said.
The primary way TOR friction management performance is measured in the field is by lateral force measurements, typically done on instrumented curves. Lateral and track-spreading forces are proportional to the friction on the top of the low rail, Eadie said. As the friction is reduced, these forces are reduced together. As a result, the coefficient of friction between the wheel and rail can be directly inferred from lateral force measurements.
Field evaluation of TOR friction management also takes into account:
- Frictional curving force
- Flanging force
- Centrifugal force
- Buff & draft force
- Coupler force
- Truck hunting
- Track geometry forces
One evaluation performed by LB Foster on a 7-degree curve with no significant gradient compared an advanced dry-film friction management product to an advanced oil-based one. Data showed that the dry-film TOR achieved a carry rate of 4.1 miles while maintaining a significant reduction in lateral forces. At the same site the oil-based product showed the potential to carry 8 miles with a reduction in lateral forces.
L.B. Foster also evaluated these products in closed-loop testing to examine different application rates and their impact on lateral forces. One material, for example, may produce the same lateral force reduction as another, but at a significantly lower application rate; in other words, the material has a higher retentivity.
A dry-film friction modifier, for example, tends to plateau; as the application rate increases, the friction level stays about the same. On the other hand, oil-based products drive the lateral forces and friction down faster and more efficiently. This can make it easy to overshoot the sweet spot of an 0.3 coefficient of friction. “Any deviations in application rate will result in too-high or too-low friction,” Eadie said.
TOR friction management can also play an important role in the generation of RCF. One thing to consider with non-drying or less-drying (oil and hybrid) materials is the possibility for the material to get into cracks and hydro-pressurize. Joe Kalousek pointed out that oil and water inside cracks is known to produce very high crack propagation rates. Water pressurizes the crack tip when pressure from the wheel is applied. Oil accumulates in cracks causing them to propagate very quickly. This could pose a problem for oil-based friction modifiers, he said.
“We have to understand the full implications of new technologies as we continue to work on them,” added L.B. Foster’s Don Eadie.
While an important part of wheel/rail interface management, TOR friction management is only one piece of the puzzle. A recent project undertaken in Saudi Arabia by Canarail and the NRC – CNRC highlights the way TOR friction management, preventive rail grinding, profile design, lubrication and other aspects of the wheel/rail interface are all part of a system.
The railroad, which is part of a mining operation, is made up primarily of tangent track, with two low-degree-of-curvature loops at the mine and at the port. There’s not much opportunity for the wheelsets to displace through their full flangeway clearance, so there should have been little flange contact, said Robert Caldwell, Senior Engineer, Rail Division at the Centre for Surface Transportation Technology. Nonetheless, the railway had a significant flange wear problem. In addition to flange wear (some of wheel flanges were worn to vertical), there was also major tread hollowing. The aggressive wheel wear was accompanied by corresponding rail wear.
At only 2 MGT there was visible head wear and the beginning of gauge-face wear. “We estimated the wear rates (gauge and head) be 18 to 24 times greater than those of a North American heavy-haul line without friction management,” Caldwell said.
Many wheels were so hollow worn that they wrapped around the gauge corner and down the gauge face. High coefficient of friction values (0.52 – 0.8) on the top of rail combined with a high angle of attack were causing large enough lateral forces to drive the wheels into hard flange contact in curves, he said.
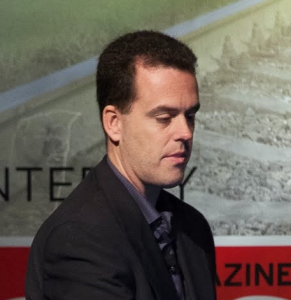
Robert Caldwell, Senior Engineer, Rail Division at the Centre for Surface Transportation Technology. (Photo courtesy of Jack Lindquist.)
With no TOR friction modifier, and being located in a desert environment, sand was causing significant abrasive wear. The sandy conditions also seemed to be contributing to high angle of attack values by interfering with centerbowl rotation. The NRC measured truck rotation and found that the trucks did not always return to their tangent running position after leaving a curve, and sometimes overcorrected.
Aside from sand infiltration, other factors, such as improperly adjusted side bearings and a lack of truck stiffness, may have contributed to rotational resistance. “The cross bracing on the trucks in service may not have offered adequate restraint to prevent relative displacement of the side frames,” Caldwell said. The analyses resulted in a list of remedial actions:
- Lubrication at curves.
- Turning trains to distribute wear.
- Matching wheel diameters.
- TOR friction management at curves.
- Asymmetric grinding on tangent track to distribute wear more uniformly across the tread surface and delay the onset of hollowing.
“The railway took a smattering of the NRC’s recommendations and implemented them, but not all of them,” said Thomas Hewitt, Rolling Stock Project Manager for Canarail Consultants Inc.
As a result, the interval between wheel truing increased from 25,000 km to 40,000 km. Wheels are wearing symmetrically. And fuel consumption has dropped by 28% due in part to implementing TOR friction management and moving to distributed power, Hewitt said.
A similar list of remedial actions helped a railroad in Australia, not to reduce wear, but to manage a noise problem.
During the 2000s Australian railroads were dealing with the growing incidence of squeal noise near residential areas, said Dave Anderson, Director of Acoustics Studio Pty Ltd. Despite TOR friction management application at the problematic sites, the noise only worsened.
A research project made up of freight operators, network owners, universities and consultants was launched to better understand the causes of and solutions to curve noise. The team instrumented a 6-degree curve and ran a series of tests over the course of nine months. “On average, we got one squeal event peaking at 120 db per freight train,” Anderson said.
Early on, the data showed that 90% of the squeal events on the instrumented curve were generated by the high wheel against the high rail. This implied a gauge-corner, high rail problem, rather than a top-of-rail, low rail problem, he said. As a result, the gauge-face lubrication regime was revamped and modernized. The initial results were very encouraging: a roughly 80% reduction in severe squeal events. Then the rail was ground.
The lubrication regime that had been so effective relied on conformal contact. Unfortunately, grinding took too much gauge corner relief and left the curve with heavy two-point contact. “Noise levels went through the roof,” Anderson said.
So the research team dug deeper and examined the underlying cause of the squeal problem: truck steering and angle of attack.
The data showed that the standard three-piece truck performed in a highly variable manner, ranging generally from +15 mRad to -15 mRad, and occasionally reaching as high as the 50 mRad range. “It was clear that getting above 20 mRad, positive or negative, greatly increased the probability of an extreme noise event,” Anderson said.
While the data showed that only the very high angles of attack caused squeal events, it didn’t show that all very high angles of attack caused them. But it was clear that getting rid of the poorly steering trucks would reduce or eliminate the probability of a noise event.
“The data shows that the type of truck and truck performance are the biggest factors,” Anderson said.
Like the case in Saudi Arabia showed, high rotational stiffness and low warp stiffness is a recipe for severe angle of attack.
Truck design and specification
The AAR M-976 bogie specification, issued in 2003 and effective in 2004, aimed to address high angle of attack issues, among other things. The spec focused on steering and high-speed stability, damping of lateral/vertical forces and bogie squaring.
“Bogie design has three dials to turn: curving, stability and vertical performance. Turning one dial changes all the others,” said Amsted’s Jay Monaco. “It’s a challenge to make subtle changes to these components.”
In order to address steering and stability, many of the designs in the M-976 spec use elastomeric pads and a special adapter. These allow the axle to take the proper angle of attack going into a curve, and then push the axle back into place when it enters tangent track. In the past, three-piece bogies without these pads could stick due to friction and maintain a high angle of attack after coming out of a curve, causing tremendous wheel and rail wear.
Elastomeric pads exist in varying levels of hardness. Stiffer materials have lower latitudinal and longitudinal deflections and more closely mimic the behavior of a standard steel adapter. Harder pads offer an increase in hunting threshold, while softer pad materials can deflect more, but have a lower hunting threshold. A squaring mechanism, such as a transom spring plank or frame bracing represent alternatives that can mitigate hunting, Monaco said. “But they add cost and maintenance issues.”
The Association of American of Railroads (AAR) and the Transportation Technology Center Inc. (TTCI), with supplier input, are currently working to determine the next generation of the M-976 specification. The demand in the industry is for common, interchangeable components, Monaco said. The challenge ahead is to balance cost and performance.
A big part of optimizing efficiency and performance is understanding the other side of the coin: wear and failure modes.
Vertical split rim (VSR) failures are one of the more catastrophic types of wheel failures that railroads encounter. VSR failures start with tread damage – shells and spalls. As this damage accumulates it applies increasing stress on the wheel, until a long circumferential section of the front rim breaks off. A wheel with a VSR failure then has the potential to drop into the gauge side of the track.
Amsted Rail is conducting ongoing studies into the causes of VSR failures and the kinds of stress patterns, particularly residual axial stress, that lead to failures. “First you have tread damage, then cracks propagate,” said Cameron Lonsdale, then Vice President of Research and Development for Amsted Rail’s Griffin Wheel Division. “There is a highly compressive axial layer that must be balanced by axial tension below the surface. When cracks propagate into the tensile zone, they can make VSR failures more likely.”
The Amsted study looked at the effects of work-hardening, out-of-roundness, wheel truing, brake dragging or heating, and drop hammer testing to focus in on the cause of VSR failures. One of the more promising finds thus far was that wheel truing, in addition to removing the tread damage that can initiate a VSR condition, also reduces the magnitude of sub-surface axial tensile stress, Lonsdale said.
The TTCI contributed to the study, helping to determine how quickly axial residual stress returns after wheel truing. That portion of the study found that after only 3,600 miles the stress pattern began to return to its pre-truing state.
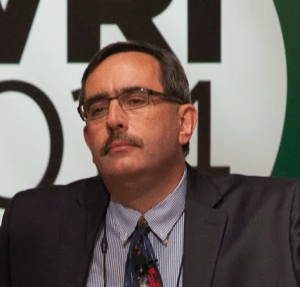
Cameron Lonsdale, former Vice President of Research and Development for Amsted Rail’s Griffin Wheel Division. (Photo courtesy of Jack Lindquist.)
The brake dragging portion of the test is still underway. This involves dragging a hand-braked car around a test track at 20, 40, and 60 mph. This generates wheel rim heat peaking at 900 degrees. After the test, the wheels will undergo X-ray diffraction testing to map the induced stress pattern.
Though the running conditions that can lead to VSR failures are not fully understood, there is strong motivation to find and treat them. “In one case we cut open a VSR-failure wheel and found another VSR failure inside it. If cracks reach that zone of tension beneath the surface, it can be catastrophic,” Lonsdale said.
Rail management
Rail is no less prone to defect and failure. Railroads routinely monitor their track with a variety of geometry, machine vision, laser profile and ultrasonic systems as part of a preventive maintenance regime.
Canadian National employs a pair of geometry vehicles to monitor its track. The self-propelled CN-1501 tested 25,000 miles of track in 2013. And the CN-15008, a pull-behind unit, tested 35,000 miles. “The self-propelled car is a blessing in the sense that it can operate when we don’t have a transportation crew and power – so you can test every day. But it can’t cover the amount of mileage the pull-behind unit can,” said Kevin Day, Assistant Chief Engineer, Technology, Testing and Standards for CN.
A recent $10-million investment in a variety of safety measures on CN includes enhancing the current geometry programs. The CN-15008 will soon be retired and replaced with a model that includes an optical system and gauge restraint measurement system.
CN also contests the idea of stopping its geometry cars after a certain number of “manageable” defects have been detected (see Automated Inspection and the Power of Data). “I’ve heard it said that transportation would park your cars based on the number of exceptions found. We don’t do that,” Day said. We run the cars no matter how many defects we find. We know that data is going to allow us to do proactive maintenance.”
The data collected from these cars is used first for immediate review by field personnel and for dealing with critical issues as soon as possible, and second, for longer-term preventive maintenance and planning using Holland LP’s Rangecam maintenance-planning software.
Using Rangecam and the data collected by their geometry cars, CN is able to plot historical data to estimate future rail wear. “We can look at a combined wear of 18 mm of wear, for example, and turn that into a rate of change of 3 mm of wear per year,” Day said. This allows CN to determine whether something must be done to mitigate current wear patterns immediately, or if it’s better to plan for future rail renewal work.
Day noted that two important things for data accuracy are the number of geometry runs, and the threshold limits that are manually entered into the system. A threshold limit for either gauge-face wear or top-of-rail wear, alone, may not accurately capture wear conditions as well as a combined wear metric.
Moving forward, CN hopes to use additional software and available technologies to automatically determine rail type during track testing runs. “We’d like to know, across the system, what size rail we have. We don’t have that information at our fingertips, but it’s something that would make a big impact,” Day said.
Even the best measurement and monitoring technologies can miss things. A 2013 derailment on Norfolk Southern shows how a perfect storm of events led to the derailment, and how the testing regime failed to see the problem brewing.
After the derailment, the investigation team recovered 19 of 21 pieces of broken rail. “This rate of broken rail piece recovery is unprecedented,” said Brad Kerchof, Norfolk Southern’s Director of Research and Tests. Six of the rail fractures showed surface shells, and five of those shelled rails had transverse defects (TDs).
The first questions the team set out to answer were: which fracture broke first, and why? To determine this, they took rail end batter, wheel flange marks, and internal defects into account. The team concluded that the first break caused an impact which accelerated a defect further down the rail, causing another break, resulting in and 11-inch piece of rail that was broken but remained in place. This piece was subsequently knocked away and the wheels began to batter the rail exposed by the gap – a process that continued in a chain reaction of rail fractures, Kerchof said.
The next question the team asked was: what hints were there of a developing rail integrity problem? Visual inspection showed that the rail surface condition was not particularly poor. Prior to the derailment, there had been two tests for internal defects using ultrasonic induction, as well as two tests by cars equipped with machine-vision systems.
One of the limitations of ultrasonic induction testing is that certain conditions can cause a “loss of bottom” or loss of data, Kerchof said. A loss of bottom can be caused by rail surface conditions, the presence of a bolt hole, or loss of the seal between the transducer and rail. In the event of a loss of bottom, the standard is for the car operator to do a manual test to look for a vertical defect.
The investigation team compared loss of bottom reports to the fractures from the derailment; it turned out that they lined up. “The take away is that a clean rail could be hiding a shell, and there may be a TD beneath that,” Kerchof said.
Most railroads have now adopted a standard procedure for a loss of bottom report in a turnout. The current standard on NS is that a loss of bottom of 3 inches or greater in a turnout is considered a defect. “We need to apply that standard to open track as well,” Kerchof said.
This is important because shells initiate roughly 0.25 in. below the gauge corner on the high rail, and typically grow 2 – 3 in. longitudinally, before breaking out. The appearance of shells is important because they can block an ultrasonic signal and compromise an internal defect test, Kerchof said. And they can initiate transverse defects. Closely spaced shells that result in TDs can lead to broken rails.
TDs originating at the gauge-face in curve-worn rail are also known as reverse TDs. Most curves can develop gauge-face wear to the degree that there are ribbons of overflow peeling off the bottom of the gauge, though not necessarily to the detriment of rail integrity, Kerchof said. However, when reverse TDs appear, they typically appear in clusters. And when one reverse TD breaks, the impact causes the next to break – again starting a chain reaction that breaks out pieces of rail, as in the case of the 2013 derailment.
The NS derailment case shows that no one tool is a silver bullet, and that in terms of the tools and technologies of rail testing, there is always room for innovation.
The demands on the railroad industry are always increasing — heavier loads, higher speeds, longer trains. Close attention to wheel/rail interaction, and innovation at the interface are necessary to meet these demands in a safe, efficient, and cost-effective way. There is work to be done, but the industry has shown that it’s up to the challenge.
Jeff Tuzik is Managing Editor of Interface Journal