WRI 2015 — Heavy Haul Part 2: A Proactive Approach to Asset Management
By Jeff Tuzik
The benefits of taking a proactive approach to wheel/rail interface management are well known. Year after year at Wheel Rail Interaction conferences, speakers have extolled the benefits of moving away from costly reactive maintenance strategies. The “firefighting” method of moving from one critical exception to the next, means that there is never enough money or time to optimize the system as a whole.
New technologies make it easier now than ever to get ahead of the maintenance curve and move into a more proactive, and predictive, model. One such technology is machine vision.
Machine vision systems show great promise in their ability to assess system health (including track, ties and fasteners, wheels and bogies, wayside equipment) at speeds and accuracy rates greater than human inspectors are capable of. But like any emergent technology, there are many challenges in implementing and optimizing current systems.
“The thing to keep in mind,” said Kambiz Nayebi, President of Beena Vision, “is that good data is hard to get and harder to process; what you see is not what a computer sees.”
The human eye is very good at pattern recognition, and walking inspectors are very good at spotting flaws and defects, but there aren’t enough inspectors to inspect the entire system, all the time. Machine vision systems can do just that, said Kim Bowling, Director of Advanced Engineering at CSX Transportation, but there are significant challengers in data storage and processing. Some newer vision systems generate as much as a terabyte of data per train pass. “It’s far too much data for a person to sort through,” she said.
One approach to tackling such large datasets is to process the raw data as soon as possible on-site and send only relevant condescend and processed data to the home server for human review and storage. “A system like that,” Nayebi said, “requires significant processing power at the wayside, however.”
In addition to the logistical challenges of data processing and storage, there are challenges in how the data is processed in the first place. “Your data is only as good as the algorithms that sort through it,” Bowling said. Algorithms that process machine vision data are typically designed to sort exceptions and issue alarms based on varying predefined levels of severity. Because of the tremendous amount of data generated, even performing a human review of every alarm is often unfeasible, she said.
As a result, algorithms have to be able to reliably prioritize high-severity alarms for human review. Systems known to generate more false-positives and false-negatives also have to be prioritized for review.
Machine vision systems are a relatively new tool in terms of wheel/rail asset management. At their current stage of development, these systems perform a first-pass review. They’re not capable of completely removing the “human bottleneck” from the data processing equation, but they do provide a greatly expanded frequency and depth of inspection versus manual inspection alone.
Deeper Inspection
Machine vision systems aren’t the only relatively recent addition to the railroad industry’s arsenal of inspection technologies. Systems designed to detect surface cracks related to rolling contact fatigue (RCF) are gaining traction throughout North America.
Norfolk Southern is conducting ongoing validation of eddy current and magnetic induction technologies – the results of which have appeared at previous WRI conferences and in Interface Journal articles (see Measuring With Eddy Current). These studies have helped to identify the strengths and shortcomings of eddy current and magnetic induction measurement devices, and have helped to define their role in the North American environment.
Part of defining the role of RCF / surface crack measurement devices in the heavy-haul industry, is knowing how to apply the data they generate to rail grinding and renewal programs, said Brad Kerchof, Director of Research and Tests at Norfolk Southern. To that end, the NS study aimed to answer the following questions:
- What is the best way to characterize cracks? Is it by depth, length, angle or density?
- At what stage of crack development is rail grinding advised?
- Should grinding be done to remove all present cracks?
The National Research Council of Canada (NRC) has also studied the application of electromagnetic surface crack measurement technologies – specifically, how the technologies can be used to quantify RCF and the “magic wear rate.”
Prior to the advent of eddy current/induction measurement, there was no way to non-destructively measure surface cracks and crack growth rate, NS’ Kerchof said. As a result, rail grinding done to mitigate RCF has typically been based on an educated, but subjective, assessment of surface damage based on pre- and post-grind visual inspection.
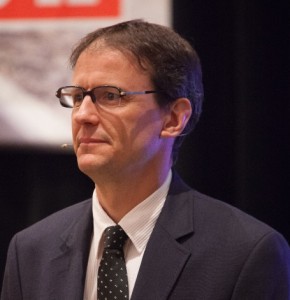
Both NS and the NRC hope to better understand how to leverage the measurements provided by eddy current/induction devices to provide a more accurate, data-based approach to maintaining the magic wear rate. “The key is to catch cracks during the period in which they’re growing very slowly; grinding truncates the crack and restarts the crack growth model,” said Eric Magel, Principal Engineer, Rolling Contact Fatigue, at NRC.
The NS study used three primary methods of validating crack measurements: rail cross sections, incremental milling, and dye penetrate testing. Milling validation (in which the rail surface is incrementally removed until the target crack is no longer present), noted Kerchof, is the most accurate way to measure crack length and depth. Cross section validation can be very accurate, but depends on the rail being sectioned at the deepest point of the crack in order to take an accurate measurement.
Dye penetrate validation was used to determine the presence (or absence) of cracks in rail following rail grinding. “The data showed that crack measurement devices can distinguish between rail with and without cracks,” Kerchof said. A strong electromagnetic response typically demonstrates the presence of significant RCF.
Earlier phases of testing by NS have shown that both eddy current and induction measurement devices can accurately measure crack length, but that crack depth measurements are less reliable. These results, combined with the results of the post-grind dye penetrate validation seem to indicate that surface crack measurement technologies like eddy current could be a useful addition to rail grinding programs. “The exact measurement numbers are off, but the trend exists and can be used in prioritization of grinding,” Kerchof said.
“If we can use [eddy current/induction measurement] just to tell where RCF is heavy, moderate, or absent,” added Eric Magel, “that’s already more information than we have now.”
Questions remain, however, on how important it is to completely remove all surface cracks during a grind cycle – “Moving to a ‘remove-all-cracks’ model of grinding is a very significant expense,” Kerchof said.
Eddy current and induction measurement devices will continue to improve, and validation studies are ongoing at NS and the NRC. Several companies are developing hi-rail versions of these technologies, as well as systems that combine eddy current, induction and ultrasonic measurement capabilities into comprehensive rail inspection packages.
From the Ground Up
Proactive management of wheel/rail assets encompasses more than monitoring and measurement devices. From ballast drainage to train operations, every part of the railroad system that is optimized in its own right contributes to an optimized wheel/rail interaction.
Bridge ends and the transition zones leading to and from bridges are one area in which a proactive maintenance and design strategy can result in tremendous long-term savings in terms of rail, tie, and fastener life, said Darrel Cantrell, Vice President, Cantrell Rail Services.
Due to significant differences in track modulus between bridges and bridge-ends, transition zones can be a source of very high lateral and vertical forces. “When a locomotive hits a low bridge end, you can literally see it bounce,” Cantrell said. That kind of high impact loading often initiates corrugation that continues across the bridge. The resulting cyclic pounding damages concrete piers, ties, fasteners and the rail itself.
Some of the problems associated with bridge-end transition zones can be corrected by properly maintaining the track in the lead up to the bridge end. “Poor drainage and fouled ballast are some of the biggest problems at bridge ends,” Cantrell said.
There are also technologies that can help balance track modulus between bridges and bridge ends and can damp L/Vs generated at transition zones. CN recently tested the Amsted RPS’s Loadmaster resilient tie plate on several “problem” bridges – bridges that were known to generate excessive track forces, and that had very short replacement cycles.
The Loadmaster resilient tie plate uses rubber springs to damp track forces and spread loading across multiple ties and tie plates. “We determined the damping effect to be 30 to 40 percent” Cantrell said. CN’s testing also determined that the reduction in dynamic loads afforded by the resilient tie plates continued past the bridge ends, through the transition zone and into the track for several hundred yards.
At one test site, CN concluded that the installation of the damping resilient tie plates, combined with remedial ballast and drainage work in transition zones resulted in over $100,000 per year savings in bridge maintenance, rail replacement deferral, and spot tie replacement, said Tom Bourgonje, Regional Chief Engineer of CN’s Southern Region.
Bridge ends and transition zones represent one potential problem area for high L/Vs and dynamic loads, but there are many others. As rail steels themselves have become harder and rail life has increased over the years, weld locations in continuously welded rail (CWR) can end up being a weak link in the system.
“Rail life is starting to exceed weld life,” said Rich Kral, Engineering Manager, Research and Development, at Holland LP. Defects often occur at flash-butt or thermite weld locations due to wheel/rail contact at the softened zone of the weld, he said. One strategy to address the problem is to try to make the softened zone as small as possible. Techniques used to do that, however, often result in high residual stress in the weld, which can lead to other problems, Kral said.
Another strategy is to decrease the number of welds in CWR. In practice, this means laying longer rail lengths. Until recently, the longest rail available in North America was rolled in 80-foot lengths. Recently, however, oversees rail manufacturers have begun producing 480-foot lengths. These 480-foot rails require only 17% of the welds-per-mile that 80-foot lengths require, Kral said.
Bringing 480-foot rail lengths to North America is no easy task. Holland, as part of a joint project with UP recently completed construction of a specialized port facility and welding plant designed specifically to accommodate 480-foot rail.
The new rail lengths have only recently begun to be processed at the Holland plant, but railroads are already looking forward to the cost savings associated with fewer welds and fewer incidences of weld-related damage and fatigue.
On the Surface
One of the most important parts of wheel/rail interface management is maintaining an optimized rail profile. Rail grinding can correct and maintain optimal wheel/rail contact, but it’s a technology that requires a careful and nuanced application. NS recently conducted a rail grinding study that explored wheel/rail contact conditions on canted rail.
The study looked at rail that was canted outward and as a result, over a number of years, had worn to develop conformal contact. When the cant was corrected, because of gauging or new tie installation, the profile that was conformal at the canted position became problematic, Kerchof said.
NS found that canted, worn-in rail developed high head slope angles and low base/height values (both major concerns in rail rollover potential) as a result of having been ground while in a canted position. “If the rail were to stay in this canted-out position, you probably wouldn’t have a problem,” Kerchof said. But NS did correct the cant, and there were problems.
Following a number of rail rollover derailments, NS developed a program to further analyze curves with worn high rails with the following characteristics: low base/height ratios, head slope of 5 degrees or more, cant close to 3 degrees. It turns out that rail meeting these criteria were likely to have wheel contact to the field side of rail once cant was correct, Kerchof said.
To solve the problem, NS worked with Loram to develop grinding patterns specific to the canted scenario. NS compared post-grind and post-cant-corrected profiles to profiles taken from rail rollover derailments. “One of the most noticeable differences was that the rollover profiles all had a high field side,” Kerchof said. So a primary aim of the modified grinding pattern was significant field-side relief.
After applying the modified grinding pattern to canted rail, NS then corrected the cant and found that the primary contact patch was shifted to the gauge-side of center, and that there was no field-side contact. The corrected rail did not meet any of the danger criteria for rollover risk. “We made the right decision to change the profile in advance of gauging; otherwise, the gauging and tie installation work would have resulted in field-side tread contact,” Kerchof said.
Rail profile and track geometry are a big part of the wheel/rail interaction system. Friction management is, too. And friction management, like all parts of the wheel/rail system, doesn’t just benefit the track, it benefits wheel life, too.
A recent UP study explored and attempted to quantify the benefits of using a train-mounted top-of-rail friction modifier (TOR FM). The program studied two coal utilities with nearly identical fleets, using 90% identical track. One utility operated with train-mounted TOR FM, the other without.
UP measured the performance of the two utilities using wheel impact load detectors (WILDs) and by measuring wheel tread wear. Cars operating with TOR FM showed a significant reduction in the number of impacts exceeding the 90-kip standard.
The study also looked at other thresholds (60,70,80 kips) and these echoed the reduction in the 90-kip threshold exceedance when TOR was used, said David Elvidge, Principal Development Engineer at L.B. Foster. In addition, wheels operating with TOR, if they did exceed kip thresholds, tended to do so later in their service lives. In terms of wear reduction, the utility operating with TOR FM showed a 53% reduction in wear rate versus the utility without.
The WILD data and wear analyses were then compared to UP car repair billing data. The car repair billing data agreed with the wear and WILD measurements, said John Peters, Manager of Operating Systems and Technology at Union Pacific Railroad. Car repair billing data showed a reduction in wheel changeout rates due to wear, shelling and spalling, and 90-kip threshold exceedance, he said.
The benefit of TOR friction modifiers is by now well-documented and widely accepted. But studies like the one conducted by UP help to quantify those benefits, which in turn help to build a better business case for the use of friction modifiers.
Operations and Carbody Dynamics
Nearly every force in the railroad system eventually makes its way into the wheel/rail interface. Forces generated by operating practices are no exception. Railyards, for example, often use humps or flat switching to accelerate cars to relatively high velocities. And while Operations attempt to keep these velocities to a minimum, impacts are often higher than desirable.
Depending on the type of coupling system (draft gear or end-of-car cushion unit), damage to the railcar can occur at these velocities, said John Deppen, Director of Engineering at Amsted Rail.
Damage can occur in-train too. Train length, gross rail load, and locomotive inputs are the initial sources of in-train shock forces, and these forces are magnified by free slack between cars and in automatic couplers. “Slack is the enemy,” Deppen said, “One or two inches of slack in a coupler may sound small, but multiplied across the entire train, it adds up fast.”
As a slack wave propagates through a train there can ultimately be a several mile-per-hour difference between the front and back of the train, Deppen said. The high lateral, longitudinal and vertical forces generated by carbody collisions and slack run in/run out events ultimately feed into the wheel/rail contact patch, he added.
Cushion units and draft gear can help mitigate carbody stresses associated with impacts and slack events, but ultimately train operations are the origin of those stresses in the first place. “It’s better to try to manage the forces that go into the system, rather than having to manage excessive forces,” Deppen said.
The extreme dynamic forces generated by slack runs can, in certain scenarios, have catastrophic results. A series of NS case studies help to illustrate the relationship between force, slack and track geometry. In one case, the rapid application of dynamic braking, combined with the train makeup and coupler type caused a massive slack run-in that derailed the train. “It was so severe that the cars pitched and bounced off the track,” said Walter Rosenberger, Operations Engineer, Research and Tests at Norfolk Southern.
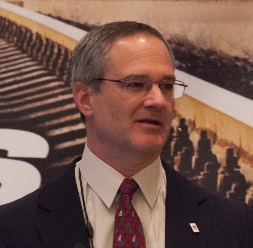
In the case of the slack run-in derailment, the train had a large number of cushion unit-equipped cars, followed a large number of heavy double-stack cars. End of car cushion units, noted Deppen, have a long travel and significant slack take-up in order to protect on the typically delicate cargo. In addition, the train was not equipped with distributed power to help mitigate slack. Therefore the train that derailed in this case was essentially set up for massive slack run-in potential, Rosenberger said.
A second NS case study illustrates another type of adverse relationship between force, slack and track geometry that can develop. In the second case, slack run-in wasn’t the culprit, but rather a steady-state buff force.
When a multilevel car is in buff force, or steadily braking, to the point where it has compressed its cushion unit, the couplers push to one side of the coupler pocket and get “locked” into angular misalignment, Rosenberger said. This angular force makes its way into the rail and can cause the rail to roll outward. When this happens in front of a switch point, a derailment can result. The second NS case was once again a worst-case scenario. There were two cars in buff force curving in opposite directions while entering a turnout – a worst-case scenario, given the buff force/long coupler combination. The result was a steady-state force that rolled the rail enough for a lead wheel to split the switch and derail.
These case studies make it clear that even seemingly disparate elements of the railroad environment like train makeup and operations play a significant role in wheel/rail interaction. And the interplay of all these elements highlights the necessity of approaching each element with a holistic, non-siloed mindset.
A proactive approach to asset management is not the sole purview of the rail grinder, the track inspector, the engineer, or any one department or technology. Speakers at WRI 2015 stressed that every optimized asset on the railroad is a benefit to wheel/rail interaction and that optimizing wheel/rail interaction benefits nearly every asset.

Jeff Tuzik is Managing Editor of Interface Journal.