Examining Autonomous Track Geometry Testing and Instrumented Revenue Vehicle Technology
A pair of speakers from different continents discuss the benefits of autonomous track geometry collection and the advantages of monitoring revenue-service vehicles’ response to track conditions in this first installment of topics covered at this year’s annual Wheel/Rail Interaction Conference in Vancouver, B.C., Canada.
By Bob Tuzik
Brad Kerchof wasted no time, kicking off the 2022 Wheel/Rail Interaction conference with the $64-million-dollar question: “What is the most controversial and consequential legislative initiative before the FRA regarding the freight industry right now?”
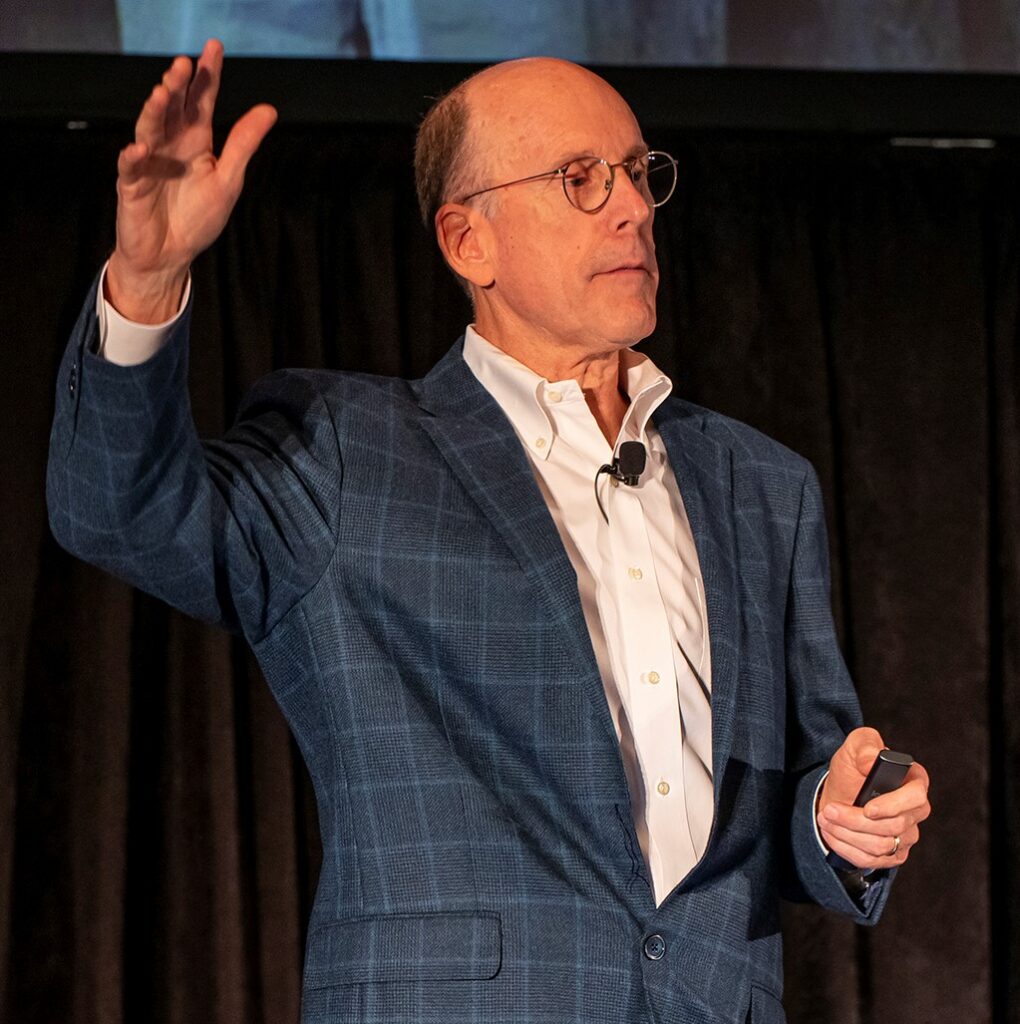
Kerchof, Senior Track Engineer at Advanced Rail Management, a Global Rail Trust company, and former Director of Research and Tests at Norfolk Southern, followed up with a pair of equally pointed and related questions: Can autonomous track geometry inspection replace traditional manual track inspection? And why has the Federal Railroad Administration backed off from its previously wholehearted support of increasing the ability for autonomous testing?
Kerchof laid some groundwork and covered the fundamentals of track inspection before coming up with answers. Manual or visual track inspection is done by a person either walking the track or riding in a hi-rail vehicle, he said. Two types of vehicle-mounted technology that measure various track geometry parameters have evolved over the years: manned geometry cars, which are staffed with an engineer and maintenance-of-way people, and, more recently, autonomous, or unmanned, systems that operate within a train consist.
Automated systems measure or evaluate standard geometry parameters, such as gauge, curvature, crosslevel, surface, and alignment. The more sophisticated systems can also measure rail profiles and wear. Machine vision systems, which look at the condition of rail running surface, types of fasteners, joint bars, and clearances, are also in use.
In 2018, BNSF proposed a new operational approach to track inspection. The concept was to increase the frequency of automated track inspection with autonomous vehicles, then decrease the frequency of manual inspections. The second step would be to determine what the most effective combination of those two inspection methods would be. BNSF petitioned the FRA for a temporary suspension of track inspection regulations. The other large Class 1s followed.
The FRA’s ‘temporary suspension of track inspection regulations’ allowed railroads to not comply with a specific part of the track safety standards in order to perform a test. The FRA grants the short-term pilot tests with a waiver of compliance, which allows a railroad to not comply with a specific part of the track safety standards over a longer period. “We tend to use the terms ‘temporary suspension’ and ‘waiver’ interchangeably,” but in FRA parlance, there is a significant difference between them,” Kerchof said. In both cases, FRA’s ongoing approval is often dependent upon the railroad meeting specific performance requirements.
Railroads have invested heavily in autonomous testing. BNSF, which tests more miles than anybody else, has four passenger coaches dedicated to autonomous testing. While the passenger coaches are unmanned, they are coupled to a locomotive with the train crew. Other railroads do it differently. NS mounted autonomous equipment on revenue-service locomotives. CN uses 10 of the Ensco-developed automated systems mounted in boxcars that operate in revenue service. CSX employs five of the box car systems, with three more being built; UP uses two box car- and three locomotive-mounted systems; CP uses three box car-mounted units.
While railroads can perform autonomous testing without FRA approval, they cannot reduce the number of manual inspections that are required without FRA approval. An FRA suspension or waiver is required to supersede FRA safety standards. The pertinent parts of Part 213 (Subpart F – Inspection) of the FRA track safety standards indicate that:
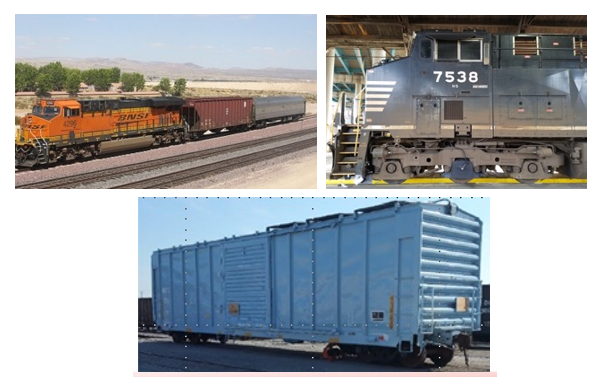
- Each main track must be traversed by the vehicle or inspected on foot at least once every two weeks, each siding must be traversed by the vehicle or inspected on foot at least once every month
- Each track inspection shall be made in accordance with the following schedule:
- Class 1, 2, and 3 track – weekly, or twice weekly if the track carries passenger trains or more than 10 MGT
- Class 4 and 5 track – twice weekly
“Mainline track is class 3, 4, or 5 and requires twice weekly manual inspection,” Kerchof said. A second provision says that you must either walk or ride over every main track once every two weeks and sidings once a month.
During the petition process, railroads justified the automated operational approach to FRA by touting its safety benefits, essentially saying that:
- Automated testing is more effective than manual inspections at finding geometry exceptions.
- More frequent automated inspections means that geometry defects will be found sooner (and exist in track for a shorter period).
- Using geometry data to find conditions that are getting close to defect level means they can be repaired before they become defects (a process known as “preventative intervention”).
Decades of automated track geometry collection have shown that automated testing is more effective than manual inspections. “I think everybody agrees with that,” Kerchof said. “Geometry cars take measurements every foot. Measurements are more precise and, unlike manual/visual inspections, are taken under load.”
Other benefits/justifications for autonomous measurement include:
- Additional safety considerations: Reduced exposure to on-track accidents (with trains and vehicles at grade crossings) due to fewer hi-rail and walking inspections.
- Improved track maintenance: Resources deployed more effectively; inspectors can spend more time fixing exceptions rather than conducting inspections. “With this approach, finders become fixers” Kerchof, said. “Inspectors can spend more time fixing defects rather than conducting redundant inspections that are driven by regulatory compliance, but do not add value.”
- Improved operations efficiency: Fewer inspection trips means less interference with trains and improved network fluidity. “On a busy mainline, a track inspector is an unnecessary interference from the point of view of the train dispatcher,” Kerchof said. And once the track inspector secures track time, he is motivated to get on track and to his destination as quickly as possible. “So, you can comply with the regulation, but the quality of your inspection is not as good as it really needs to be, in many cases.”
While not extensive, there is precedent for using automated inspections in place of manual inspections. Since 1975, the Long Island Railroad has operated under a waiver that allows a single weekly walking inspection while performing quarterly automated geometry inspections.
Making the case
Did anyone argue against the FRA granting a temporary suspension of track inspection regulations?
Rail labor (BMWED & BRS) made two arguments. One argument is that inspectors look for conditions, such as drainage/vegetation, defective rails, stripped joints, broken joint bars, ballast and tie conditions, worn and broken switch points and frogs, missing and broken fasteners, which are not detected by autonomous geometry cars. They also argued that geometry defects can develop quickly, sometimes in between twice-a-week inspections, which can be a problem if automated tests are made weekly or less frequently.
An important consideration that rail labor did not mention is: Jobs. Of course, railroads didn’t discuss the potential for work-force reductions associated with fewer manual inspections in the application process, either. And while the desire to ‘turn finders into fixers’ may be legitimate, Kerchof said, “if there’s an opportunity to reduce headcount, it’ll happen.”
How did FRA and railroads agree to measure performance? There are two concepts: The unprotected defect and baseline. Unprotected defect is a condition requiring immediate remedial action, either repair or a slow order. “A good way of describing or defining an unprotected defect is to describe what an unprotected defect is not,” Kerchof said. A defect found during an earlier inspection and properly slow ordered is not considered an unprotected defect for subsequent inspections. The baseline is the number of unprotected defects found by an automated geometry car at the start of the test program. Both of these measurements or metrics are normalized to defects per 100 miles.
The object is to monitor the unprotected defect rate as the test progresses. “If the unprotected defect rate declines during the course of the test, we’re enhancing safety and we can call our test a success,” he said. A second measure of performance is the two or more class drop, which BNSF has used to great effect.”
Let’s say, for example, a variation of crosslevel defect of 1.85 inches over 62 feet is detected on Class 5 track. When the system looks at the exception limits for Class 3, 4, and 5 track, a deviation of 1.85 inches would comply with Class 3, but would show as an exception of class 4 and 5. The remedial action would require a Class 3 slow order, which represents a multi-class-drop, Kerchof explained.
A multi-class drop is considered to be a more severe defect than a defect that would require only a one-class drop. BNSF touted the reduction in multi-class drops as an indicator of the success of its autonomous testing program and included it in their waiver request to the FRA. BNSF has since achieved zero multi-class drop defects along their waiver routes, which had never been done before, during two months in early 2022.
“It’s likely that when the FRA finally does end up with enabling legislation for this initiative, a number of years from now, that it will have two metrics,” Kerchof said. “One would be unprotected defects per mile. The other would be multi-class-drop defects per mile.”
Phased implementation is a is an important concept for how this program has been executed on the Class 1s.
NS manages its locomotive-mounted autonomous track geometry data by sending class 4 exceptions, along with 1,000 feet of track data to the back office by modem. Defects that are validated by the track geometry staff are emailed to field personnel to be repaired. NS’s commitment to the FRA was to do all of this within 24 hours.
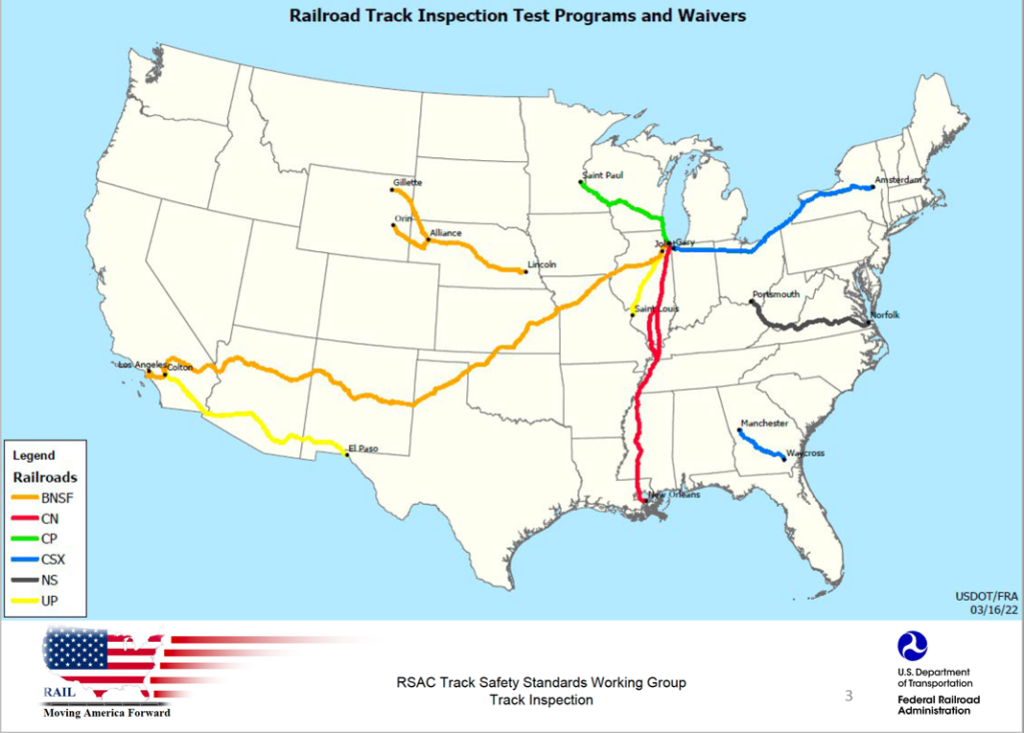
At NS, phase one was scheduled to last three months. “We would maintain our manual inspection to twice a week, maintain our monthly walking turnout and joint inspections, and we committed to inspecting autonomously three times a month on main lines and one time a month on sidings. During those three months, we would establish our baseline defect rate. During phase two, which would be the next three months, we reduced our manual inspections to once a week. The walking turnout and joint inspection remained at a monthly frequency, and our autonomous testing remained the same, as well, three times a month on the mains, once on the siding. Then we compared our actual defect rate to the baseline and if we showed an improvement, a decrease in defect rate, we would seek permission to proceed to phase three,” Kerchof said.
During phase three, which lasted six months, manual inspections were reduced to twice a month. “That’s once every two weeks for a guy out there on hi-rail truck riding his territory,” he said. Everything else on NS stayed the same, i.e., monthly inspections of turnouts and joints and the same frequency for the automated testing. “If the automated schedule could not be met, and a track or siding in multiple-track territory was missed, or if there was a problem with the equipment or data, manual inspections would resume per the track safety standards until the automated system could again meet the required schedule,” he said.
From there, the idea was to again compare the defect rate to the baseline and, if there was continued improvement, to ask the FRA for an extension of the phase three, which NS did once and received permission for the extension.
There are, of course, challenges to autonomous testing. Getting Transportation to commit to reserving a locomotive with the locomotive-mounting autonomous testing equipment to the designated test route, or boxcar-mounted equipment on a train traveling the designated route, and ensuring that the test train is routed to the correct track in multiple track territory, takes effort. And then going through dispatching records to confirm which track the geometry car or test trains ran over the entire route to make sure that the required testing frequency was met, can be a laborious task, he said.
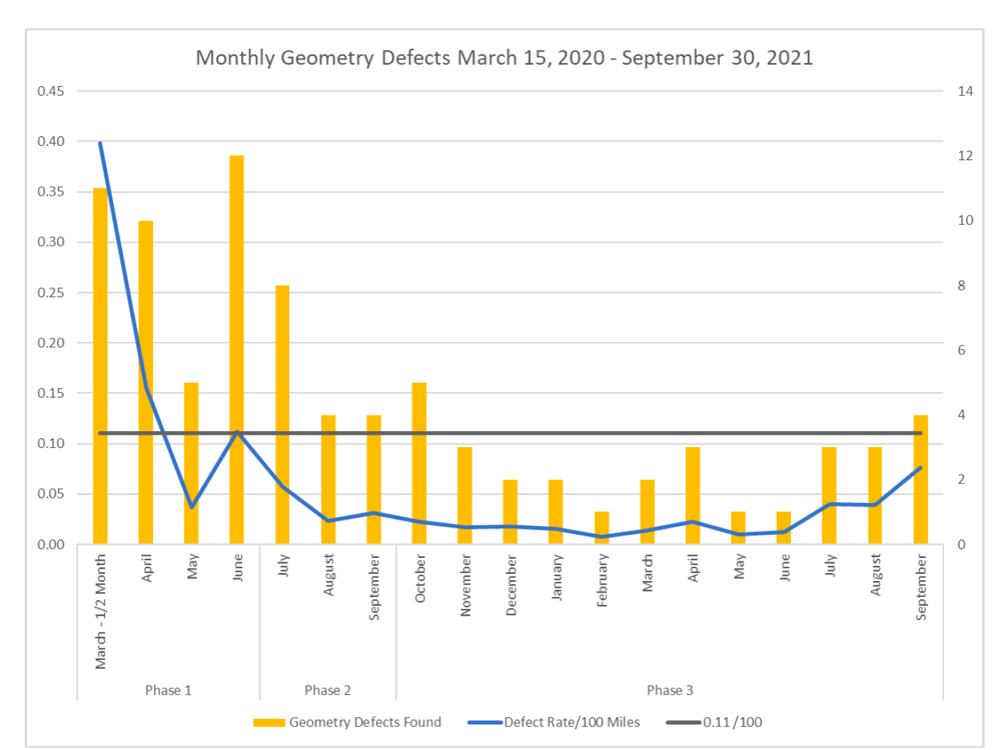
“We hope that GPS becomes sophisticated enough to distinguish the location difference between tracks 1 and 2 on multitrack lines.” During winter testing, snow can interfere with optical gauge measurement. “If we can’t measure gauge, we’re not collecting all the data required to satisfy a 24-hour response commitment. On NS, at least, geometry data must be reviewed twice a day, seven days a week on those days that a test vehicle is operating.”
Public information presented during Railroad Safety Advisory Committee (RSAC) meetings showed the following defect rate detected by the automated system during the waiver period (rates are shown as defects/100 miles): Phase 1 (baseline): 0.11; Phase 2: 0.04; Phase 3: 0.02. “This is a remarkable performance,” Kerchof said. Each of the other five railroads achieved similarly impressive defect reduction rates. “So, in terms of reducing geometry car defects, this has been an extraordinarily successful program.”
The way forward
So, where does the FRA stand regarding expanding autonomous inspection?
In the January 2020 letter approving NS’s petition for suspension to conduct a test program, FRA’s Karl Alexy wrote:
”FRA has already seen the safety and operational benefits of using automated track inspection technologies, and data has shown that automated inspection technology is more effective in detecting track geometry conditions than visual inspections by track inspectors. Furthermore, evidence suggests that these new operational approaches may be as or more effective at detecting track defects while also decreasing service interruptions and reducing safety risks to railroad employees.”
Ron Batory, the FRA administrator between 2018 and 2020, was solidly behind the initiative. But, FRA support for automated testing evaporated in 2021 with a change in FRA administrators and executive administration. Currently, FRA is allowing railroads to complete their current test programs, but will not approve or extend the temporary suspensions or any long-term waivers. At present, the NS test program is complete; the waiver expired in 2021 and NS has resumed manual inspections. The FRA has refused to extend waivers on CN, CP, CSX, and UP. Their test programs are due to end Nov 23, 2022. Only BNSF, which completed its pilot and phased-implementation test, requested a waiver early enough to obtain a long-term waiver. BNSF is now operating under a long-term waiver in the Powder River basin and on its entire southern transcontinental line.
Regardless of what comes out of the ongoing RSAC meetings and developments at the FRA, railroads will continue to expand their autonomous tasting capabilities, Kerchof said. They’ll do so because it enhances safety, and because railroads want to be prepared to substitute automated testing for manual inspections when FRA’s position finally evolves. “The data is irrefutable,” he said. “It’s just a matter of getting comfortable with the political aspects or implications of the change.”
A different perspective
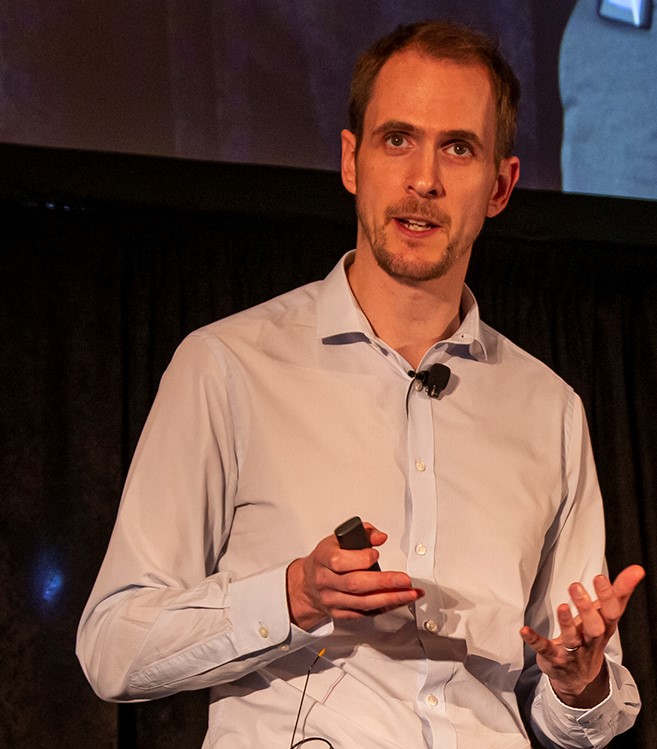
Unencumbered by the types of political and other issues faced in the states, autonomous testing has taken root on Asia-Pacific properties, where the Monash Institute of Railway of Technology (IRT), based in Melbourne, Australia, develops and deploys instrumented revenue vehicle technology.
“We are based within the university, but we’re not academics,” said Rob Lambert, Monash-IRT Senior Business Manager. “All of our work is commercial contracts with industry partners.”
Monash IRT developed and operates more than 100 IRVs across Australia and in Southeast Asia. The IRV systems, which represent an autonomous structural health condition monitoring system, are typically mounted on ore or coal cars to measure the response of the vehicle to track; track conditions are inferred from that. Data is delivered in near-real time where communications are available.
One of the most important lessons IRT has learned over 20 years of developing and deploying these systems is how rugged they must be, especially on the lines serving the iron ore mines in the Western Australian outback where temperatures reach 45 degrees Celsius (113 F). The duty cycle for passenger systems isn’t as demanding, but the challenges associated with the railroad environment remain.
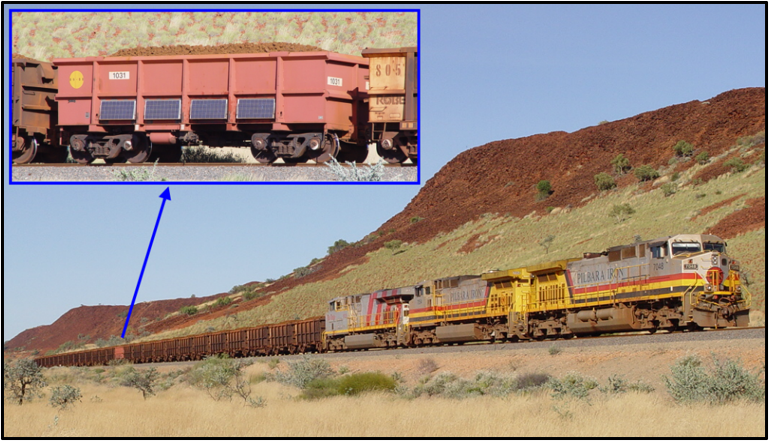
IRT typically mounts sensors on the side frame and axle box to record the accelerations that are being experienced by both the carbody and the wheelset; instrumented springs on each of the four corners to monitor what the suspension is doing. Lateral accelerometers on the bolster centerplate identify hunting, and bogey-rotation sensors monitor how the bogey is steering on tangent track and through curves.
IRVs collect the same type of data collected by track geometry cars, including surface, lateral alignment, twist, curvature, etc. “But since we’re measuring the response of the vehicle, we can capture more information than a track recording vehicle going down the track,” Lambert said. While some customers may have one or two geometry cars trying to cover a huge amount of their network, others have up to 30 IRVs running in revenue service on the network. “That generates a huge amount of data that allows for data analysis and trending.”
Data is processed at the IRT facility in Melbourne for some initial analysis to see if any of the results exceed exception limits. If so, the customer receives a severity report identifying the problem and location. Measurement data that is within the threshold parameters goes into the database for trending analysis.
“Understanding the difference in those responses and, therefore, what’s actually occurring in the track is really important,” Lambert said. Whenever there’s a different suite of vehicles operating on a track, we try to instrument at least one of each so we can measure the difference in responses. “A very high suspension travel or suspension compression on one vehicle, might not necessarily be same response on another vehicle.”
The high volume of data from revenue service vehicles allows for very good forecasting. It’s easy to trend vertical acceleration data, for example, and to plan the appropriate maintenance before reaching severity limits.
In-train forces
IRT has also developed an instrumented draft pack to measure and monitor in-train forces. IRT also does strain gauging of solid couplers to obtain real data from those components. In-train force data collected by the instrumented couplers can be loaded into a model to identify where the maximum damage is being done within the consist. IRT can simulate different axle loads to determine the effect that increased axle loads will have on components. It can also simulate the effect of upgraded components or adjustments in parameters to components, such as friction wedges, to optimize draft behavior.
IRV technology can also identify weld conditions by identifying deviations in top-of-rail longitudinal measurements. “We see a peak on the rail surface every 18 meters where a weld was made,” Lambert said. From that, IRT can review a railway’s entire weld population, the peak-to-trough difference at each weld, and the vehicle’s response to it. By using the dip height and angle from the actual longitudinal profile, IRT can determine each weld’s profile gradient, or ramp angle, which can generate vertical accelerations that can lead to instability and potential wheel unloading and flange climb.
IRT also developed and installed a dynamic track gauge system for passenger operations. The laser-based system measures track gauge, along with the other data streams, during normal traffic hours on a revenue vehicle traveling at typical operating speeds. “When you get a bad vehicle response, you can see what is happening regarding rail wear and track geometry, including cant, rail roll, and track gauge, at a specific location,” he said. “This is now standard operation at MTR Hong Kong, where two of these vehicles operate every day on every line of their network.”
While originally designed to look only at track gauge, MTR also wanted the equipment to measure and monitor rail wear. Since MTR is 24-hour operation, access to track for testing or maintenance is severely limited. “They just don’t get access to run a track recording vehicle down the track,” Lambert said.
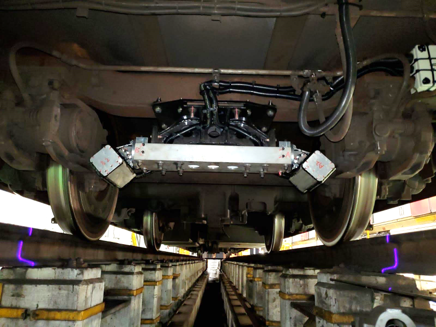
Laser profile data is collected and aligned against the appropriate right and left rail templates; side and top wear and rail angle are calculated on board in real time to minimize the amount of data that must be uploaded or transferred. By collecting rail wear data during revenue operations, MTR can use their precious maintenance windows to do engineering / maintenance work, rather than taking measurements.
MRT is also working with IRT on the development of a bespoke rig at Monash that is fitted with two pieces of rail that are mounted on electric servos that move up and down and from side to side (eventually it will be able to incline, as well) to simulate any piece of track, with any gauge, superelevation, or other geometry parameters. The rig can simulate anything that is encountered in track and can be used to validate new or existing pieces of measurement equipment to determine if the equipment is measuring “what you think you’re measuring and if the measurements are what you’re expecting,” he said.
IRT is working on an axle-powered system to replace or augment the trailing-wire and solar/battery-powered instrumentation systems on the iron ore car fleet. The axle-powered system, which has been deployed for nearly a year, generates about 350 watts at 80 kph (solar panels provide power when the car is not moving). Since the railway was concerned about what might happen to the axle or wheels if the generator seized, IRT designed a failsafe nylon bearing. “If the generator seizes, the nylon will effectively strip away and fall out, and you’re back to free running with no danger to the vehicle,” Lambert said. In the end, it’s all about providing a low-cost, rugged revenue vehicle monitoring system that can provide near real-time data on what is actually happening to a vehicle, and what track work is required to improve its performance, Lambert said. “What we’re really trying to move toward is a performance-based set of standards that identify the parameters that are actually impacting the performance of vehicles.”

Bob Tuzik is Editor-in-Chief of Interface Journal